Экструзионный пенополистирол
Экструзионный пенополистирол (экструзия, XPS)
Экструзионный пенополистирол, также как и обычный пенополистирол, состоит из пенополистирола, но отличается технологией создания гранул. Обычный пенополистирол создается путем «пропаривания» микрогранул водяным паром их гиперувеличения под воздействием температуры пары пока не будет заполнена пеной пенополистирола вся форма. Экструзионный пенополистирол производится методом экструзии. Экструзионный пенополистирол получают путём смешивания гранул полистирола при повышенной температуре и давлении с введением вспенивающего агента и последующим выдавливанием из экструдера. Внутри самого экструдера созданы специфичные условия для начала активации процесса преобразования полистирола. Экструзия заставляет полимер преобразовываться по другим механизмам и задает ему иные свойства и строение структуры. В частности, сначала происходит плавление гранул, и образуется однородная вязкая масса – сырье из твердого состояния переходит в вязко-текучее.
Экструдированный пенополистирол имеет прочную, цельную микроструктуру, представляющую собой массу закрытых ячеек, заполненных молекулами газа. Экструзионый пенополистирол — это единое химическое вещество, с межмолекулярными химическими связями, которые на порядок прочнее, чем в пенополистироле. Ячейки экструдированного пенополистрола непроницаемы, потому что, в отличие от пенополистирола, не имеют микропор, следовательно, проникновение газа и воды из одной ячейки в другую невозможно. Стенки ячеек — это сплошная масса вещества. Доступ веществ окружающей среды возможен только в открытые ячейки, находящиеся на боковых поверхностях и срезах куска экструзионного пенополистирола. Т.е. весь кусок материала не поглощает влагу, пар, и т.п. извне. Качественный экструзионный пенополистирол обладает равномерной, закрытопористой структурой, с диаметром ячеек 0,1-0,2 мм.
Этот тип материала, обладающий плотностью 28 — 45 кг/м³ и высокой прочностью на сжатие, применяется при строительстве взлётных полос, автомобильных и железных дорог. Высокая прочность экструзионного пенополистирола является его главным преимуществом и позволяет его использовать не только как утеплитель, но и как строительный материал выполняющий иногда даже функции вспомогательных или несущих конструкций.
Экструзионный пенополистирол обладает низкой теплопроводностью (0,029-0,034), минимальным водопоглощением (0,2-0,4%), малым удельным весом (25 — 45 кг/м³). По показателям теплоизоляции и легкости экструзионный пенополистирол несколько превосходит обычный пенополистирол низкой плотности, который имеет теплопроводность 0.038 Вт/(м*С), но теплопроводность EPS может ухудшадся во влажных условиях эксплуатации (например, грунтовые воды при утеплении фундамента) из-за более высокого водопоглощения. И в таком случае экструдированный пенополистирол будет уже значительно превосходить обычный пенополистирол.
Сфера применения XPS весьма широка: теплоизоляция фундаментов и цоколей, слоистой кладки и штукатурного фасада, кровли (инверсионные, традиционные, эксплуатируемые и др), полов, в том числе «тёплых». Также именно экструзионный пенополистирол применяется при строительстве автомобильных и железных дорог, снижая риск промерзания грунтов земляного полотна и последующего промерзания и вспучивания (морозное пучение грунта) Материал решает задачи теплоизоляции спортивных площадок, холодильных установок и ледовых арен.
Срок службы материала сопоставим со сроком службы всего здания, у качественных производителей он составляет более 40 лет.
Недостатки XPS (по сравнению с EPS)
К недостаткам экструзионного пенополистирола относится в 5 раз более худшая паропроницаемость 0.013 Мг/(м*ч*Па) чем у традиционного пенопласта, что повышает требования к вентиляции дома утепленного экструзионным пенополистиролом.
Так-же существенный недостаток экструзионного пенополистирола — его высокая горючесть (класс Г3-Г4), в то время как многие производители обычного пенополистирола за счет специальных добавок добились фактически негорючих характеристик по классам Г1 и В1. Тем не менее, согласно СНиП 21-01-97 «Пожарная безопасность зданий и сооружений» и Федеральному закону №123 (Российскому) экструзионные плиты высокой степени горючести (Г3-Г4) могут использоваться в конструкциях. При повышенных требованиях к пожарной безопасности используют экструзионный пенополистирол группы горючести Г3. Однако, существуют современные ЭПС, в характеристиках которых по заявлению газеты класс горючести Г1 (слабогорючий материал)! Реализуется это за счёт новейших добавок из графитовых нано-частиц. … Эм, проверка этой информации показала, что производитель такого всё-же не заявляет, и класс горючести любого экструдированного пенополистирола Г3 либо Г4. Не верьте никому! И даже мне=)
Также следует отметить, что согласно новому Федеральному законодательству РФ (ФЗ №123) для горючих теплоизоляционных материалов регламентируется определение показателя токсичности продуктов горения, для качественных пенополистиролов она составляет не более Т2 — умеренноопасные. Кстати, показатель Т2 также присущ и материалам из дерева, например паркетам.
ПОЛУЧЕНИЕ ТЕПЛОИЗОЛЯЦИОННЫХ МАТЕРИАЛОВ Н4 ОСНОВЕ ПОЛИСТИРОЛА МЕТОДОМ ЭКСТРУЗИИ
Высокая сорбционная способность полистирола к предельным углеводородам и их галогенпроизводным (фреонам) явилась основой для развития технологии пеноизделий. По сравнению с другими крупнотоннажными пластмассами полистирол относительно легко перерабатывается методом экструзии, так как требует меньших энергозатрат и обладает более широким интервалом температур при переработке по сравнению, например, с полиолефинами. Инертность фреонов по сравнению с пентанами с точки зрения пожарной безопасности также способствовала их внедрению в производство.
Первые производства пенополистирольных плит методом экструзии были созданы фирмой «Ооу СЬет.» в конце 1950-х гг. В качестве пеноаген гов использовалась смесь фреонов 11 и 12. Однако экологические проолемы, связанные с нарушением озонового слоя из-за широкого использования этих фреонов, привели к необходимости их замены на озонобезоиасные соединения, к которым можно отнести:
1) неполностью галогенировачные углеводороды: фреоны 142в, 22,134а и 152а;
2) нейтральные газы: азот и углекислый газ:
3) предельные углеводороды: бутан, пентан, изопентан.
Применение дешевых инертных газов — азота и углекислого
Газа в качестве пеноагентов ограничивается их низкой Генри растворимостью в полистироле. Так, для достижения растворимости азота более 10 см3/г требуется давление свыше 200 кгс/см2 (см. рис. 5.3), что технически трудно обеспечить в экструзионном оборудовании. В связи с этим азот используется в качестве пено — агента только при получении из полистирола экструзионных вспененных пленок толщиной до 500 мкм.
Углекислый газ, в отличие от азота, характеризуется удовлетворительной Генри растворимостью в полистироле (=15 см3/г при
давлении 80 кгг./см2). Однако низкий коэффициент диффузии С02 (см. табл. 5.2) снижает скорость его десорбции при формировании пеноизделий на заключительных стадиях экструзии и приводит к получению повышенной плотности изделий (более 40 кг/м8).
Углекислый газ применяют при производстве из полистирола методом экструзии листов толщиной 1-5 мм, а также как добавку к фреону при выпуске пенополистирольных плит толщиной 20 мм и более с целью повышения их плотности и соответственно прочности.
Высокое значение Генри растворимости углеводородов С4-С5 в полистироле приводит к тому, что при формовании пеноизделий часть пор становится открытыми. Это снижает теплоизоляционные свойства пеноплит и их влагостойкость.
Использование предельных углеводородов С4-С5, обладающих высокими сорбцией и диффузией по отношению к полистиролу, затруднено практически, так как связано с необходимостью обеспечения условий взрывобезопасности экструзионного оборудования, производственных помещений, включая склады хранения готовых пеноизделий.
С точки зрения теплоизоляционных свойств пеноплит, полученных на основе различных пеноагентов, существенными преимуществами обладают плиты, полученные на основе фреонов (рис. 5.8), так как фреоны обладают наименьшим коэффициентом теплопроводности среди рассмотренных пеноагентов.
Таким образом, использование галогенпроизводных углеводородов в качестве пеноагентов при получении теплоизоляционных пеноплит является оптимальным, ибо в процессе экструзии обеспечивается получение пеноплит закрытой ячеистой структуры, в которой длительное время сохраняется определенная доля фреона. Низкая теплопроводность фреона обеспечивает пониженную теплопроводность пенополистирольных плит (ЭПС), получаемых на его основе методом экструзии. Пеноплиты (ВПС) на основе смеси пентана с изопентаном уступают им по этому показателю.
Наиболее широко распространенным пеноаген — том, используемые в производстве пенополистирольных плит, получаемых экструзионным методом, является
Рис. 5.8. Диаграмма влияния пеноагентов на теплопроводность пенополистирольных плит
Фреон фреон С02 °оздух 142в, 22 152а, 134а
Смесь фреонов 142в (СН3СС№2) и 22 (СНС1Р2) состава 60 : 40. Эта смесь обеспечивает низкую теплопроводность пеноплит в течение длительного времени (более 20 лет), благодаря низкой скорости диффузии фреона 142в. 1
В качестве альтернативы смеси фреонов 142в и 22 представляет интерес смесь Фреонов 152а и 134а в соотношении -70 : 30, обладающая меньшим парниковым эффектом.
Основные характеристики указанных смесей фреонов и углекислого газа приведены в табл. -5.3.
Таблица 5.3 Характеристики агентов вспенивания при получении пенополистирольных плит экструзионным методом
|
Смесь фреонов 152а и 134а по сравнению с фреонами 142а и 22 обладает в 2 раза меньшей проницаемостью по отношению к полистиролу и повышенным коэффициентом теплопроводности.
С целью повышения раствооимости в полистироле смеси фреонов 152а и 134а в качестве добавк I, способствующей повышению сорбции пеноагента полистиролом, используются спирты или кето — ны, например этиловый спирт [7-9]. Анализ патентов показывает, что смесь фреонов 152а и 134а може ‘- быть эффективным агентом вспенивания при получении пенополистирольных плит методом экструзии, при этом увеличение теплопроводности плит не превышает 10 % и остается существенно ниже, чем для члит, получаемых с использованием в качестве пеноагента воздуха или пентанов.
Использование углекислого газа в качестве пеноагента не может быть альтернативной заменой смеси фреонов 142в и 22, так как высокое давление газа приводит к образованию значительного количества открытых пор, что, наряду с повышением теплопроводности, приведет к потере теплоизоляционных характеристик пеноплит, получаемых экструзионным методом.
Аппаратурно-технологическое оформление процесса получения пенополистирольных плит методом экструзии можно разделить на две основные группы, схематически изображенные на рис. 5.9:
1. Установки тандемного типа, состоящие из двух последовательных экструдеров (рис. 5.9, а, б). Первый экструдер предназначен для плавления исходного полистирола и смешения его с добавками. На выходе из первого экструдера происходит смешение расплава полистирола с пеноагентами, подаваемыми под давлением специальными насосами. В качестве первого экструдера плавления первоначально использовался одношнековый экструдер (рис. 5.9, а). По мере развития производств он был заменен двухшнековым экструдером (рис. 5.9, б). Второй (одношнековый) экструдер предназначен для охлаждения расплава, его тщательного перемешивания с целью обеспечения однородной прочности расплава и подготовки его к процессу формирования плит.
А
Двухшнековый экструдер плавления и смешения с добавками |
| |
| |
| |
Экструдер охлаждения и гомогенизации расплава
Экструдер охлаждения и гомогенизации расплава
Зона плавления |
Статический Теплообменник |
| |
| |
Рис. 5.9. Схематическое изображение типов экструзионных линий, используемых для получения полистирольных пеноплит:
А, б — тандемные установки из двух экструдеров. Охладитель расплава — динамический в виде второго одношнекового экструдера специальной конструкции; в, г — моноэкструзионные установки (б — двухшнековый экструдер, совмещенный с динамическим охладителем расплава; г — двухшнековый экструдер для плавления. Охладитель расплава статического типа)
Рис. 5.10. Влияние температуры и содержанья фреона на вязкость полистирола:
105 100 120 140 160 180 200 Г, ”С |
I — полистирол оез фреона; — о — 2 — полистирол с 5 % фреона; — Д — 3 — полистирол с 20 % фреона
2. Моноэкструзионные установки с испотьзоъанием двухшнековых экструдеров (рис. 5.9, в, г) и статических смесителей для стабилизации и охлаждения расплава.
Первоначально в производстве пеноплит появились именно тандемные установки. Наличие независимого экструдера плавления позволяет осуществлять смешение исходного полистирола в расплаве с индивидуальными добавками: антипиренами, красителем, тальком, который играет роль физического зародышеобра — зователя, способствующего образованию пор.
Смешение расплава полистирола с адсорбционно активными средами, например с фреоном, приводит к снижению поверхност ного натяжения на границе раздела расплав полимера — фреон и, следовательно, к существенному снижению вязкости расплава (рис. 5.10). Это позволяет обеспечивать транспортировку расплава уже при температуре 110-140 °С вместо 180—190 °С, т. е. стабилизация смеси полимера с пеноагентом происходит при высокоэластическом состоянии полимера.
Создание и развитие производств двухшнековых экструдеров явилось технической базой для организации моноэкструзионных установок получения пенополистирольных плит (рис. 5.9, в, г). В этом случае экструзионная линия состоит из одного двухшнекового экструдера, в котором первые зоны являются зонами плавления полистирола и его смешения с добавками, затем после зоны сжатия происходит охлаждение расплава, сопровождаемое подачей вспенивающего агента.
Наличие эффективных зон смешения расплава полимера с агентом вспенивания в двухшнековом экструдере обеспечивает однородность расплава и его надежную транспортировку при температуре 120-140 °С.
Концентрация добавляемого агента вспенивания зависит от толщины получаемых экструзионных изделий. Так, при производстве вспененных пленок и листов толщиной до 3-4 мм содержание фреона находится на уровне =10 % (мае.). При получении пеноплит толщиной более 20 мм содержание фреона увеличивается до 16-18 % (мае.).
Первоначально в моноэкструзионных установках получения пеноизделий охлаждение расплава производилось ь динамических теплообменных устройствах (рис. 5.9, в), совмещенных со шнеками основного двухшнекового экструдера. Разработка эффективных устройств смешения расплава в статических условиях позволила в экструзионных линия? получения пеноплит на основе двухшнеко — вого экструдера (рис. 5.9, г) использовать для охлаждения расплава статические смесители вместо динамических. Использование статических смесителей для охлаждения и гомогенизации смеси расплава полимера с агентом вспенивания максимально снижает турбулентность расплава и повышает его однородность по сравнению с использованием экструдера для охлаждения расплава на тандемных установках. Статические смесители специальной конструкции, предназначенные для охлаждения и гомогенизации, непосредственно прифланцовываются к двухшнековому экструдеру.
На стадии гомогенизации под действием напряжения, создаваемого экструдером, начинает развиваться процесс жидкого крей — зинга в полимере под воздействием пеноагентов, играющих роль ААС. Наличие направленногс воздействия на полимер, создаваемого во втором экструдере тандемных установок (рис. 5 9, а, б), вызывает нарушение ламинарности потока и может приводить к зарождению неоднородной структуры на начальном процессе жидкого крейзинга.
После гомогенизации смесь поступает в фильеру. На этой стадии начинается процесс формирования пеноиздетшй. Тип получаемого пеноизделия определяется конструктивными особенностями фильеры:
— плоская фильера предназначена для получения пеноплит толщиной 20-150 мм;
— кольцевая фильера — для производства пленок и листог толщиной 0,3-0,4 мм;
— профильная фильера — для изготовления декоративных профилей;
— стренговая фильера — для изготовления гранул диаметром до 4 мм.
Приобретение опыта по созданию производств концентратов позволило отказаться от использования индивидуальных добавок в производстве пеноизделий и перейти к применению их в виде 40-50 % — х концентратов на основе полистирола.
Использование добавок в виде концентратов с экологической точки зрения обладает рядом преимуществ: снижается образование пыли, повышается точность дозировки добавок, исключается стадия предварительного смешения добавок с исходным полистиролом. В установках тандемного типа, имеющих одношнековый экструдер плавления, использование концентратов для смешения с расплавом полистирола невозможно, так как одношнековые экструдеры не обеспечивают однородного смешения.
Моноэкструзионные установки на базе двухшнекового экструдера, снабженного статическим охладителем и гомогенизатором расплава, являются более прогрессивными по сравнению с установками тандемного типа. Одним из основных производителей мо — ноэкструзионных установок является фирма «LMP» (Италия), ко торая выпускает установки производительностью до 600 кг/ч.
Технологическая схема моноэкструзионной установки производства пенополистирольных плит методом экструзии представлена на рис. 5.11.
Технологический процесс получения пеноплит на моноэкстру- зионных установках на основе двухшнекового экструдера состоит из следующих основных стадий и узлов:
1. Хранение исходного сырья, добавок и отходов.
2. Предварительное смешение концентратов различных добавок.
3. Дозирование исходного сырья и смеси добавок в основной двухшнековый экструдер.
4. Плавление исходного полистирола и добавок в двухшнековом экструдере и смешение расплава с пеноагентом.
5. Охлаждение расплава в теплообменнике статического типа.
6. Гомогенизация расплава в гомогенизаторе статического типа.
7. Подготовка расплава к формированию пеноплит в фильере.
8. Формирование пеноплит в кали&раторах.
9. Разрезание и обработка краев пеноплит.
10. Сбор, грануляция отходов и их возврат ь основной процесс.
Хранение исходного полистирола в виде гранул осуществляется в специальных цилиндрических емкостных силосах, снабженных сигнализаторами верхнего и нижнего уровня и циклонами для улав — яивания пыли. Хранение отходов, образующихся при обработке пеноплит и утилизации некачественных изделий, получаемых при пуске установки, также производится в силосах аналогичного типа. В нижней конической части силосы оборудованы специальными камерами всас ывания, через которые с помощью вакуума осуществляется подача гранул в питающие бункеры основного производства.
Все добавки, необходимые для получения пеноплит, вводятся в основное производство в виде 10-40 %-х гранулированных концентратов с полистиролом.
Гранулы исходного полистирола, возвратного полистирола и концентратов должны иметь цилиндрическую форму с размерами: диаметр (2-3) мм, длина (3-5) мм. Возвратный полистирол может иметь вид щепы.
Рис. 5.11 Принципиа пьная технологическая схема получения пеноплит экструзионным методом в двухшнеко — вом экструдере со статическим теплообменником |
Хранение концентратов добавок осуществляется на складе в мешках
Агенты вспенивания или их смеси хранятся в специальных емкостях при повышенном давлении (до 12 кгс/см2), которые снабжены манометром, предохранительным клапаном и уровнемером. Емкости хранения пеьоагента имеют циркуляционный контур, с помощью которого обеспечивается поддержание постоянного давления при хранении и подаче пеноагентов в основное производство.
Концентраты добавок в определенном заданном количестве вручную загружаются из мешков в вертикальный предварительный смеситель, снабженный мешалкой шнекового типа с импеллером в нижней части. После кратковременного смешения смесь концентратов добавок перегружается в промежуточный бункер для смеси добавок (см рис. 5.11).
Как правило, прл получении пенополистирольных плит используются концентраты талька, красителя и антипирена.
Дозирование исходного полистирола, возвратного полистирола и смеси концен гратов в питающую воронку основного экстру дера из питающих бункеров производится с помощью непрерывных весовых дозаторов шнекового типа. На входе в основной экструдер вмонтирован металлоискатель для удаления посторонних металлических примесей. Система подачи твердых компонентов должна быть сконструирована таким образом, чтобы исключить образование пыли при транспортировке гранул. Наличие пытга в исходном сырье нарушает работу непрерывных весовых дозаторов.
Дозирование агента вспенивания в зону смешения основного экструдера производится специальным высоконапорным 3-х сту пенчатым дозировочным насосом диафрагменного типа, создаю щим давление до 100 кгс/см2. Непосредственная подача агента вспенивания в зону смешения экструдера, находящегося под давлением 50-70 кгс/см2, производится игольчатым клапаном, открытие которого происходит автоматически — при достижении на нем давления 100 кгс/см2.
Основной экструдер получения пеноплит представляет собой двухшнековый экструдер с отношением длина : диаметр = 32, который имеет 8 зон регулирования температуры. Шнеки экструдера вращаются двигателем постоянного тока в одном направлении.
Шнеки состоят из наборных элементов различной конструкции по каждой из зон. Внутри шнека каждой зоны имеются спе — циа льные проточки, предназначенные для циркуляции теплоносителя, обеспечивающего регулирование температуры по зонам экструдера.
Непосредственно к экструдеру прифланцован теплообменник, представляющий собой многозаходный статический смеситель специальной конструкции, предназначенный для удаления избы точной тепловой энергии из полимера и стабилизации температуры полимера. К теплообменнику примыкает гомогенизатор, являющийся также статическим смесителем простейшей конструкции, 3 гомогенизаторе происходит окончательная стабилизация температуры расплава до величины, характерной для перехода полимера в высокоэластическое состояние, и обеспечивается однородность реакционной массы. После гомогенизатора расположена щелевидная фильера, имеющая три зоны (корпус, головка и губы) регулирования температуры. Температура на губах фильеры поддерживается на 10-15 °С ниже температуры размягчения полистирола, так как на этой стадии начинается формирование пено — плит
Регулирование температуры по зонам экструдера, в теплообменнике, гомогенизаторе и фильере осуществляется с помощью специальных контуров охлаждения. В первом контуре в качестве теплоносителя используется обессоленная вода, а в двух других — высокотемпературный органический теплоноситель (ВОТ). Теплоносители в контурах охлаждения находятся в замкнутых циклах. Поддержание температуры теплоносителя в каждом контуре обеспечивается за счет циркуляции захоложенной воды через теплообменные устройства, вмонтированные в эти контуры.
Первый контур охлаждения, работающий на обессоленной воде и обладающий наиболее высокой теплопередачей, предназначен для регулирования температуры в зонах смешения расплава полимера с агентом вспенивания (зоны 4, 5 экструдера), а также на губах фильеры.
Второй контур, работающий на ВОТ с высокой температурой, обеспечивает регулирование температуры в зоне п, [авления полимера и подачи пеноагента (зоны 2, 3 экструдера), а также в транспортирующих зонах экструдера (6-8).
Третий контур регулирует температуру в теплообменнике, гомогенизаторе, корпусе и на головке фильеры.
В основном экструдере происходит ряд сложных сЬизико-хи- мических процессов, необходимых для последующего формирования пеноплит.
В первой зоне экструдера при температуре 200-210 °С происходит плавление полистирола с добавками с целью перевода полимера в вязко-текучее состояние. Во второй зоне экструдера (зона сжатия), где поддерживается температура 220-230 °С, происходит смешение в расплаве полистирола с добавками, возвратным полимером и создается давление, необходимое для транспортировки
Расплава полимера с добавками. В конце второй зоны экструдера на шнеках имеются специальные сегменты, предотвращающие появление обратных потоков и попадание во вторую зону экструдера агента вспенивания.
В третьей зоне экструдера (зона сжатия) при температуре 215- 220 °С под давлением осуществляется ввод агентов вспенивания.
В четвертой и пятой зонах экструдера температура расплава снижается до 85 -95 °С для предотвращения роста давления и начинается процесс смешения расплава полимера с агентом вспенивания. Растворимость пеноагента в расплаве полимера зависит от температуры и давления, а также от природы агента вспенивании и молекулярной массы исходного полимера. Введение 15-20 % фреона, являющегося агентом вспенивания, снижает вязкость расплава полимера (см. рис. 5.10) так, что ее величина при 120-130 ПС становится равной вязкости расплава полистирола при 180-190 °С. Это обеспечивает надежную транспортировку полимера вблизи его температуры размягчения, т. е. в высокоэластическом состоянии. Наличие частиц талька в расплаве полимера обеспечивает появление неплотностей или «дырок» в вязкой жидкости, способствующих проникновению агента вспенивания и повышению его Генри растворимости.
В зонах 6-8 экструдера при постепенном снижении температуры от 140 до 100-105 °С происходит динамическое смешение раси пава с пениагеятом и его одновременное охлаждение.
Окончательное охлаждение реакционной массы завершается в теплообменнике — многозаходном статическом смесителе, в котором поддерживается температура 85-95 °С. В данных условиях агент вспенивания в виде жидкости на этой стадии уже начинает играть роль адсорбционно активной среды (ААС), способствующей проявлению процесса жидкого крейзинга. Можно предположить, что именно на этой стадии начинается процесс инициирования крейз.
В гомогенизаторе при температуре 110-120 °С достигается стабилизация структуры и состава расплава с целью повышения его однородности и прочности. Возможно, на этой стадии происходит рост крейз, инициированных ААС После гомогенизатора полимер, находящийся в высокоэластическом состоянии, продавливается через фильеру, в головке и корпусе которой поддерживается температура =120 и 100 °С соответственно. Пребывание полимера в гомогенизаторе и фильере в высокоэластическом состоянии способствует не только повышению прочности расплав?, но и увеличивает сорбционную способность по иистирола, повышая Генри растворимость фреона в микронеоднородных структурных зонах полимера.
Важным фактором для обеспечения однородности расплава на этих стадиях является приближение течения полимера к ньютоновскому. Повышение однородности полимера по молекулярной массе (сужение ММР) способствует его текучести как ньютоновской жидкости. Стабильность давления, действующего на полимер в гомогенизаторе и фильере, является важным фактором, позволяющим исключить турбулентность при течении. В этом отношении процесс охлаждения расплава полистирола в статических условиях обладает реальными преимуществами по сравнению с динамическим охлаждением в установках тандемного типа.
Использование двухшнекового экструдера в моноэкстоузион- ных установках для получения пеноплит обеспечивает лучшее смешение расплава полистирола с добавками и агентом вспенивания по сравнению с одношнековым экструдером.
Стабилизированный при температуре 100-120 °С вязкий «раствор» полистирола после фильеры п подавливается через ее губы при температуре 75-85 °С. На этой стадии начинается формирование пеноплиты, так как при выходе из фильеры агент вспенивания мгновенно вскипает, что способствует охлаждению полимера и его одновременному вспениванию. Температура губ фильеры поддерживается несколько ниже температуры стеклования полимера для предотвращения его перехода в хрупкое состояние при мгновенном охлаждении при вспенивании. Для предотвращения налипания расплава губы фильеры имеют тефлоновое покрытие, которое обновляется через 15-20 сут непрерывной работы линии.
С физико-химической точки зрения на выходе расплава полимера из губ фильеры под действием растягива: )щего напряжения, создаваемого тянущими устройствами (волочильнями), завершается процесс жидкого крейзинга. На этой стадии крейзинга происходит коллапс крейз, приводящий к образованию микро — пор, в которых капсулируется агент вспенивания.
Образование микропор при однородности расплава и его повышенной пбочности протекает стабильно. Сужение ММР полимера и повышение его молекулярной массы способствуют получению пор, однородных по размеру, с одновременным повышением прочности их стенок.
После выхода с фильеры первоначально сформированная плита под действием напряжения, создаваемого волочильнями, проходит первую стадию созревания через систему трех калибрационных плит, нагретых до температуры, соответствующей хрупкости полимера (75- 80 °С).
При калибрации протекает процесс дальнейшего образования микрочор с одновременной десорбцией агента вспенивания. Поверхность первого калибратора также имеет тефлоновое покрытие для исключения налипания полимера. При калибрации на поверхности пеноплит образуется тонкая пленка гомополимера, что обеспечивает повышение прочности пеноплит.
После калибрации полученная пеноплита охлаждается при транспортировке ее по роликовому каландру. Затем в специальных камс рах происходит разрезание плит по длине и обработка их краев для обеспечения максимального удобства использования полученных изделий в качестве эффективной теплоизоляции.
При получении пеноплит на тандемных установках в качестве исходного полистирола используется полимер с более низкой молекулярной массой, чем на моноэкструзионных установках. Это обусловлено тем, что в одношнековых экструдерах не обеспечивается однородное смешение высокомолекулярного полистирола с добавками.
Под действием сдвиговых напряжений, создаваемых в экструдере охлаждения на тандемных линиях, нарушается ламинарное течение полимера. Это способствует появлению неоднородностей в микроструктуре не только полимера в высокоэластическом состоянии при его транспортировке по экструдеру, но и при формировании пли гы. При этих условиях в плитах увеличивается число слабых мест, а снижение молекулярной массы используемо*ю полистирола снижает прочность полимерных стенок, образующих поры. В результате процесс созревания пеноплит, полученных на тандемных установках, протекает более длительно, чем на моноэкструзионных установках, а прочностные показатели пеноплит будут ниже.
Отходы, образующиеся при обработке краев пеноплит, собираются пневмотранспортом в емкости для отходов и поступаю™ в воронку специального экструдера для переработки отходов. После предварительного уплотнения измельченные отходы расплавляются в зоне плавления экструдера. Экструдер для переработки отходов также имеет зону дегазации, в которой происходит удаление агентов вспенивания. После этого расплав сжимается и через стренговую фильеру производится его грануляция. Гранулированный возвратный полимер, содержащий твердые добавки (тальк, краситель, антипирен и др ), поступает в силос хранения отходов возвратного полимера и добавляется к исходному полистиролу при получении пеноплит
При обработке полимера в основном экструдере и при переработке отходов происходит механическая деструкция полимера, в результате которой показатель текучести расплава возвратного полимера увеличивается в 2-2,5 раза. С целью снижения деструкции целесообразно добавлять при получении пеноплит термостабилизаторы, наличие которых снижает разрушение полимера под термическим и механическим воздействием.
Рис. 5.12. Влияние структурных характеристик талька на распределение микро — г. ор в пенополистирольнь’х плитах. Содержание талька 2,3 %:
1 — размер микрочастиц талька 120-140 мкм; — О — 2 — иазмер микрочастиц талька 30- 80 мкм; — Л — 3 — тальк с бимодальным размером микрочастиц: 30-80 и 120-140 мкм
Анализ показывает, что на установках тандемного типа меха но-химическая деструкция полистирола протекает в большей степени, о чем свидетельствует увеличение показателя текучести расплава возвратного полистирола в 3-3,5 раза.
Изучение влияния особенностей получения пенополистироль- ных плит на формирование их структуры позволяет выявить наличие корреляции между размерами микрочастиц талька и распределением по размеру микропор, образующихся в плитах (рис. 5.12). Наличие этой зависимости свидетельствует о том, что тальк является физическим нуклезатором и способствует образованию дефектов в расплаве полимера. В этих микродефектных зонах концентрируется агент вспенивания. При переходе расплава полимера в состояние высокоэластичности (на стадии охлаждения и гомогенизации) возникшие микрообласти, содержащие агент вспенивания, превращаются в зоны развития жидкого крейзинга. Анализ концентрации талька в полимере при получении плит показывает, что каждая микрочастица талька размером 140 мкм образует в полимере до 104 пор аналогичного размера. Снижение размера микрочастиц талька до 20- 30 мкм уменьшает размер пор и увеличивает количество пор, образующихся в полимере, больше чем на порядок. Улучшение микроструктуры пеноплит и снижение размера микропор при одновременном повышении их однородности обеспечивают повышение прочностных показателей пеноплит [10]. Установлено, что снижение размера микрочастиц талька до 20-30 мкм обеспечивает получение пеноплит с прочностью при 10 %-м сжатии до 0,5-0,6 МПа при плотности 40-42 кг/м3. Использование талька с размером микрочастиц 120-140 мкм позволяет получать плиты с прочностью не более 0,4 МПа. Использование в качестве промоторов веществ, обладающих высокой пористостью и соответственно сорбционной способностью, налример у-окиси алюминия в минимальных количествах (0,1 %) (рис.
5.13), повышает однородность распределения микропор в пеноплитах. Увеличение
Рис. 5.13. Влияние добавки промотора порообразования у — окиси алюминия на распределение микропор в пенопо лигтролыдах плитах при содержании талька 2,3 %:
20 40 60 80 100 120 140 160 |
1 -тальк без промотора; — о — 2
— тальк с промотором (у-окись алюминия 0,1 %)
Содержания талька при получении пеноплит способствует оптимизации распределения микропор в пеноплитах (рис. 5.14).
Вещества, обладающие сорбционной активностью, например у-окись алюминия, оказывают большее влияние на повышение однородности микропор в плитах, чем тальк. Так, добавка 0,1 % у-окиси алюминия по эффективности воздействия на микроструктуру плит аналогична увеличению содержания талька с 2,3 до 2,7 %. Увеличение концентрации талька выше некоторой критической величины недопустимо, так как происходит нарушение стабильности расплава.
При получении пеноплит на моноэкструзионных установках существенное влияние на их качество оказывает температура в гомогенизаторе, которую необходимо поддерживать на 10-15 °С выше температуры размягчения полистирола. Эта темпера-урэ зависит от показателя текучести расплава полистирола. Плотность получаемых пеноплит при этом уменьшается, так как повышается прочность стенок и снижается количество дефектных пор, разрушающихся при созревании плит (рис. 5.15).
Стабильность ьязкотекучего и высокоэлас! ичегкого состояний полимера при получении пеноплит являются решающими параметрами для получения плит высокого качества. Об этом свидетельствует снижение плотности получаемых плит при повышении скорости вращения экструдера (рис. 5.16) при сохранении неизменным его литания. Это явление объясняется тем, что с увеличением скорости вращения шнеков
Рис. 5.14. Влияние концентрации талька на распределение микропор в пенополисти- польных плитах:
1 — содержание талька 2,3 %;
-О — 2 — содгржапие талька 2,7 %
Н Рис. 5.15. Зависимость те. лпера-
О туры в гомогенизаторе и плотно-
Н сти плит от показателя текуче-
£ сти расплава (ПТР) исходного
Полистирола:
1 — температура в гомогенизаторе; — О — 2 — плотность плит
Основного экструдера повышается и стабилизируется давление перед теплообменником. Прочность получаемых при этом пено — плит несколько повышается и стабилизируется. Одновременно происходит снижение плотности пеноплит.
Обобщение технологических особенностей получения пенопо- листирольных плит показывает, что использование статических смесителей для охлаждения полимера и стабилизации его однородности на стадии высокоэластического состояния имеет решающее значение для оптимизации производства пеноплит. Анализ патентных данных [11] показывает, что использование статических смесителей в производстве пеноизделий является наиболее перспективным. Так, фирма «Зульцер» [11] запатентовала процесс смешения расплава полистирола с физическими нуклезаторами и последующего насыщения расплава предельными углеводородами в статических смесителях специальной конструкции. Грануляция под давлением такого расплава полистирола с пеноагентом позволит получать полистирол для вспенивания в виде гранул, а в перспективе — совместить процесс получения полистирола и пеноплит в едином технологическом потоке.
Рис. 5.16. Зависимость плотности плит «Пеноплэкс-45» (1) и производительности их выпуска (2) от скорости вращения шнека основного экс — трудеоа со:
1 — плотность, кг/м3;
-о — 2 — производительность, м3/ч
(О, об/мин
Сопоставление тандемных и моноэкструзионных установок при получении пенополистиролиных плит методом экструзии свидетельствует о наличии ряда технологических преимуществ моноэкструзионных установок на базе двухшнекового экструдера со статическими смесителями на стадиях охлаждения и гомогенизации:
— смешение полистирола с нуклезаторами и другими добавками в двухшнековом экструдере характеризуется более высокой эффективностью по сравнению с одношнековым экструдером;
— степень механо-химического воздействия на расплав полистирола снижается, так как зоны плавления в двухшнековом экструдере существенно меньше по длине;
— использование статических смесителей вместо экструдера на стадии охлаждения расплава и обеспечения его однородности перед формированием плиты позволяет исключить турбулентность расплава и способствует повышению однородности микроструктуры пеноплит;
— снижение теплосодержания в расплаве полимера перед формированием плиты за счет использования статических смесителей вместо второго экструдера охлаждения в тандемных установках сокращает время созревания пеноиаделий;
— прочностные показатели пеноизделий могут быть увеличены путем использования полистирола с повышенной молекулярной массой (низким значением ПТР).
В установках тандемного типа верхнее значение молекулярной массы полимера ограничено не только условиями его смешения с добавками в одношнековых экструдерах, но и повышением механо-химической деструкции полимера.
admin Основы технологии полистирольных пластиков
в чем разница с пенополистиролом, что лучше экструзионного, отличия экструзии и обычного, чем отличается
Сегодня при выборе утеплителя для дома перед каждым человеком открываются широкие возможности. Среди всего разнообразия большим спросом пользуются такие изделия, как пенопласт и пенополистирол. Многие думают, что это идентичные материалы, ведь для их получения применяют полистирол. Но это далеко не так, так как каждый из представленных теплоизоляторов имеет свою область применения и свойства.
Плюсы и минусы Экструдированного пенополистирола
Экструдированный пенополистирол – это теплоизоляционный материал, для которого характерна равномерная структура. Она состоит из мелких ячеек закрытого типа. Для получения плиты ЭПП происходит смешивание гранул полистирола под высоким давлением. При этом плавно вводится вспенивающий агент.
На фото- экструдированный пенополистирол
К достоинствам материала можно отнести:
- Высокие показатели сохранения тепла. Коэффициент теплопроводности составляет 0,031-0,042. Так как он высокий, то это удается снизить расход пенополистирола в несколько раз.
- Не подвергается воздействию влаги. В основе материала положен такой компонент, как полистирол. В процессе обработки у него формируются ячейки, которые наполнены воздухом. Благодаря этому утеплитель не впитывает воду. Таким образом, применять экструдированный пенополистирол можно при обустройстве фундаментов, бассейнов и плоской кровли. За счет водостойкости материал характеризуется высокими теплосберегающими свойствами, которые неизменны на протяжении всего срока службы.
- Теплоизоляционный материал не подвергается влиянию гнили, плесени и грибков.
Таким образом, его структура остается неизменной.
- Высокие показатели прочности на сжатие. При влиянии на пенополистирол механических или температурных факторов он остается в прежнем состоянии.
- Высокая шумоизоляция. Так как в ходе изготовления пенополистирола его ячейки заполняют воздухом, то это повышает его звукоизоляцию. Применяя материал для теплоизоляции дома, удается улучшить шумоизоляцию его на 35 Дб.
- Высокая пожаробезопасность. Рассматриваемый утеплитель не способствует распространению и поддерживанию очага возгорания. Кроме этого, пенополистирол – это самозатухающий теплоизолятор. Таким образом, с его помощью можно даже потушить огонь.
- Доступная цена. Благодаря невысокой стоимости позволит подобный утеплитель смогут многие желающие.
- Не вступает в химическую реакцию. Утеплитель не поддается влиянию извести, соли, гипса, рубероида, цемента, бетона, соды, спирта.
Помимо этого, он сможет выдержать непродолжительный контакт с пищевыми и машинными сливами.
- Экологическая чистота. Применяя экструдированный пенополистирол, можно не переживать относительно своего здоровья.
- Продолжительный срок службы. Так как при получении полистирола использовался метод экструзии, то это гарантирует материалу высокие эксплуатационные характеристики. Его свойства остаются неизменными в течение 50 лет. Поэтому часто менять старый утеплитель на новый не придется.
На видео – экструдированный пенополистирол:
Не лишен экструдированный пенопласт минусов. При его контактировании со сложными углеродами он начинает крошиться. Негативно влияют на него УФ-лучи при прямом контакте. При нагреве 25 градусов в 1 м3 утеплителя будет находиться 104 микрограмм стирола. Применять его при теплоизоляции фасада с высокой степенью эксплуатации не придется, так как здесь понадобиться более плотный материал.
Что собой представляет и где используется потолочная плитка из пенопласта, можно узнать из данной статьи.
А вот как приклеить пенопласт к бетону и что стоит использовать из клеющего материала, рассказывается в данной статье.
Как происходит штукатурка пеноплекса снаружи и с помощью какого материала, поможет понять данная информация: https://resforbuild.ru/sypuchie-materialy/shtukaturka/po-penopleksu.html
А вот как происходит фасадная штукатурка по пенопласту и насколько сложно это выполнить, подробно рассказывается в данной статье.
Плюсы и минусы пенопласта
Пенопласт – это теплоизоляционный материал, который характеризуется белым цветом и жесткой вспененной структурой. Она содержит 98%воздуха и 2% полистирола.
На фото- пенопласт для утепления
К преимуществам пенопласта можно отнести:
- Инертность относительно таким материалов, как известь, песок.
- Малый вес. Таким образом, применять пенопласт можно даже при утеплении тех конструкций, которые не должны подвергаться серьезным нагрузкам.
- Простота установки. Выполнить всю работу сможет даже человек, который не имеет должного опыта в этом деле.
- Экологическая чистота. Пенопласт – это безопасный утеплитель. Благодаря этому он не выделяет в окружающую среду токсичным компонентов.
- Поддается обработке. Чтобы получить нужную форму и размер материала, можно использовать обычный нож.
- Низкая цена. Теперь купить пенопласт под силу практически каждому, кто решил заняться утеплением своего дома.
На видео- пенопласт для утепления:
Как выбрать пенопласт. Как выбрать сетку для пенопласта.» data-lazy-type=»iframe» data-src=»https://www.youtube.com/embed/Q4bN_BAh78k?feature=oembed» frameborder=»0″ allow=»accelerometer; autoplay; encrypted-media; gyroscope; picture-in-picture» allowfullscreen=»»/>
Процесс монтажа такого легкого и недорого утеплителя не доставляет никаких сложностей. Его можно смело использовать для сельскохозяйственных построек, складов, помещений технического назначения. Даже теплоизоляция на чердаке не станет утомительной процедурой. Есть у пенопласт ряд минусов, к которым можно отнести токсичность при горении и образование плесени при неверной установке.
В чем разница
Если провести сравнительный анализ между пенопластом и экструдированным пенополистиролом, то на первый взгляд особой разницы между ними нет. Они изготовляются из одного материала, но только вот технология производства и плотность у них разные. А основное отличие между ними состоит в сфере применения. Полистирол разрешено задействовать при теплоизоляции цоколя с шириной 20-30 мм, а вот толщина пенопласта должна составлять 50 мм. А о том, какие плюсы и минусы у потолочной плитки из пенополистирола вы можете почитать в статье.
На видео- отличие пенопласта от экструдированного пенополистирола:
Возможно вам так же будет интересно узнать о том, каковы теплоизоляционные свойства пенопласта.
А вот какова цена утеплителя Пеноплекс для стен дома снаружи и где можно применять такой материал, рассказывается в данной статье.
Как происходит поклейка потолочного плинтуса из пенопласта, можно увидеть на видео в данной статье.
А вот каковы характеристики экструдированного пенополистирола Пеноплекс существуют в настоящее время, рассказывается в данной статье.
Возможно вам также будет интересно узнать о том, что собой представляет декоративный утеплитель для стен внутри дома.
Что лучше
На основании приведенный выше информации можно сделать вывод относительно того, какой утеплитель лучше – пенопласт или экструдированный пенополистирол. Профессиональные строители чаще всего выбирают для утепления домов и прочих построек пенополистирол, многие отдают предпочтение утеплителям для стен Изовер.
Связано это с тем, что он имеет гораздо больше преимуществ, следовательно, и разницы в применении будет ощутимой. Благодаря ему можно получить качественное утепление дома, которое будет оставаться таким на протяжении длительного времени.
Сегодня при выборе лучшего утеплителя возникают определенные сложности. И причина этому широкий ассортимент товаров. Рассматривая пенопласт и экструдированный пенополистирол, можно подумать, что они идентичны. Но стоит подробнее ознакомиться с характеристиками каждого отдельного утеплителя, как сразу можно определить самый лучший и подходящий материал для теплоизоляции в том или ином случае. Так что самый лучший утеплитель каждый сможет определить для себе сам, исходя из условий монтажа, эксплуатации и личных пожеланий.
Экструзия. Экструдеры. Экструзионные линии
Экструзионная линия для производства гранул композиционного материала для кабельной промышленности
Исходные данные:
Полимерное сырье и его структура:
Требования к техническим характеристикам линии:
Предлагаемое оборудование: Экструзионная линия производства гранул композиционного материала для кабельной промышленности на основе двухвинтового экструдера в комплекте с гравиметрической системой дозирования и водокольцевой системой грануляции.
Полимерное сырье и его структура:
Технические характеристики:
Установленная мощность:
Сжатый воздух:
Электродвигатель:
Материальное исполнение:
Стандартные параметры энергоносителей:
Воздух:
Комплектация экструзионной линии:
- Опорная рама;
- Приемный бункер для гранул Полиэтилена;
- Гравиметрический дозатор для гранул Полиэтилена;
- Приемный бункер для гранул Сажевого концентрата;
- Гравиметрический дозатор для гранул Сажевого концентрата;
- Приемный бункер;
- Гравиметрический дозатор для гранул;
- Гравиметрический насос дозатор для Дибутилоловодилаурата;
- Электрический блок управления;
- Двухвинтовой экструдер;
- Вакуумный блок для закрытого контура вентиляции;
- Энергосберегающий электродвигатель экструдера;
- Электрическая панель для цифрового преобразователя;
- 15″ сенсорный экран электрического шкафа управления;
- Электрическое соединение внутри линии;
- Датчики давления и температуры;
- Водокольцевой гранулятор;
- Системы охлаждения замкнутого контура;
- Вибрационная сортировочная установка для гранул.
Линия по производству изделий из резинокомпозита
Вес: 3,55 кг/м лин
Теоретическая плотность: 1,1 – 1,20 кг/дм3
Макс линейная скорость 1 м/мин ± 10%
Производительность: ожидаемая мощность с типом профиля материала 60х60: 180 кг/ч ±10%
В зависимости от формулы процесса и свойств сырого материала. Точные данные определяются после лабораторных проб.
Вес: 3,125 кг/м лин
Теоретическая плотность: 1,1 – 1,20 кг/дм3
Макс линейная скорость 1 м/мин ±10%
Производительность: ожидаемая мощность с типом профиля материала в виде полупирамиды 60х70х45: 160 кг/ч ±10%
В зависимости от формулы процесса и свойств сырого материала. Точные данные определяются после лабораторных проб.
Принципы работы:
1.Гравиметрическое устройство подачи для HDPE (полиэтилен повышенной плотности)
2.Гравиметрическое устройство подачи для вторичного сырья
3. Гравиметрическое устройство подачи для пигментного концентрата
4.Гравиметрическое устройство подачи для добавок в порошок
5.Гравиметрическое устройство подачи для наполнителя
6.Установка боковой подачи для наполнителя
7.Дегазация
Преимущества прямой экструзии
Нет необходимости предварительно смешивать / гранулировать материал.
Применима более высокая влажность содержания.
Компактный.
Простое управление логистикой.
Экономия энергии.
Более низкая стоимость обслуживания / управления благодаря меньшему размеру экструдера.
Более низкая стоимость обслуживания благодаря модульной конструкции винтов и бочки (емкости).
Значительное снижение стоимости (на энергию, рабочую силу, логистику, управление…).
Более высокие механические характеристики благодаря улучшенному смешиванию наполнителя / пластика.
Меньше ухудшения свойств материала благодаря только одной истории нагрева/разделения.
Непрерывная линия регулирования (настройки) состава.
Поддержка собственного ноу-хау в процессе производства по внутренним заказам.
Линейные компоненты
СЕКЦИЯ А погрузочно-разгрузочные устройства для сырья
СЕКЦИЯ B Гравиметрическое устройство подачи сырья
СЕКЦИЯ С одновременно поворачивающийся двухшнековый экструдер
СЕКЦИЯ D пресс-формы и калибраторы
СЕКЦИЯ E главный шкаф управления
СЕКЦИЯ F оборудование, расположенное ниже по технологической цепочке
Опции и вспомогательные системы
Для секции С: система замкнутого контура для вентилирующего вакуумного насоса
Опция 1 оборудование для соэкструдированного отделочного слоя
Вспомогательная система 1 метод помола отходов
Вспомогательная система 2 установка для охлаждения водой
1. Обработка сырья (сырьевого материала).
2. Гравиметрические устройства подачи непрерывного действия.
3. Опорные рамы.
4. Одновременно поворачивающийся двухшнековый экструдер.
5. Устройство боковой подачи для наполнителя.
6. Зубчатый насос дозировки полимеров.
7. Пресс-форма для профиля.
8. Калибраторы и охлаждающая ванна.
9. Опорный стол калибратора.
10. Отвод изделия из экструдера.
11. Чистка щеткой или система тиснения.
12. Система поперечного разреза.
13. Стол комплектации (сбора).
СЕКЦИЯ А погрузочно-разгрузочные устройства для сырья
Поз. А. 1 Полимер в форме гранул в мешках по 25 кг.
Пневматический питатель с заборным щупом.
Гранулы будут вытягиваться из короба (корзины) (не включен в объем поставки), который расположен на стороне экструдера.
Макс горизонтальное расстояние 5 м.
Макс вертикальное расстояние 6 м.
Поз.А.2 Измельченные отходы
Для хлопьев в коробке (не включено), расположенной на стороне экструдера.
Пневматический питатель (устройство погрузки (с заборным щупом.
Макс горизонтальное расстояние 5 м.
Макс вертикальное расстояние 6 м.
Поз.А.3 Добавки в форме гранул
Ручная погрузка из стеллажа накопителя.
Поз.А.4. Добавки в форме порошка
Ручная погрузка из стеллажа накопителя.
Поз.А.5 Наполнитель в форме порошка
Для наполнителей в больших мешках.
Конструкция держателя для больших мешков (макс габариты 1,1х1,1х2 м)
Подвеска для больших мешков: вручную с помощью вильчатого погрузчика
Пневматическая система выгрузки для трудно передвигаемого порошка.
Корзина (короб) для хранения с системой вибрации.
Порошковый фильтр для воздушной вентиляции.
Система погрузки с помощью архимедова винта.
СЕКЦИЯ B Гравиметрическое устройство подачи для сырья
Поз. B.1 Гравиметрическое устройство подачи для полимера в форме гранул
Дозирующая система весового питателя непрерывного действия с максимальной мощностью до 50% от производительности всей линии.
Питатель винтового действия с высоким разрешением цифровой ячейки погрузки.
Бункер повторной погрузки 50 л.
Датчик уровня.
Пневматический клапан нагнетания.
Поз. B.2 Гравиметрическое устройство подачи для измельченных отходов
Дозирующая система весового питателя непрерывного действия с максимальной мощностью до 15% от производительности всей линии
Питатель винтового действия с высоким разрешением цифровой ячейки погрузки.
Бункер повторной погрузки 23 л.
Датчик уровня.
Пневматический клапан нагнетания.
Поз. В.3 Гравиметрическое устройство подачи для добавки в форме гранул
Дозирующая система весового питателя непрерывного действия с максимальной мощностью до 10% от производительности всей линии
Питатель винтового действия с высоким разрешением цифровой ячейки погрузки.
Бункер повторной погрузки 23 л.
Датчик уровня.
Пневматический клапан нагнетания.
Поз. В.4 Гравиметрическое устройство подачи для добавки в форме порошка
Дозирующая система весового питателя непрерывного действия с максимальной мощностью до 10% от производительности всей линии
Питатель винтового действия с высоким разрешением цифровой ячейки погрузки.
Бункер повторной погрузки 23 л.
Датчик уровня.
Пневматический клапан нагнетания.
Поз. В.5 Гравиметрическое устройство подачи для наполнителей в форме порошка
Дозирующая система весового питателя непрерывного действия с максимальной мощностью до 65% от производительности всей линии
Питатель винтового действия с высоким разрешением цифровой ячейки погрузки.
Бункер повторной погрузки 200 л. специального исполнения для порошка, который тяжело пересыпать
Датчик уровня вибрации.
Пневматический клапан нагнетания.
Поз. В.6 Панель управления
Для управления до 8 весовыми установками
Удобный в пользовании графический дисплей с сенсорным экраном.
ПО для управления дозированием.
Поз.В.7 Стальная опорная рама
Для опоры весового дозатора и погрузочных устройств.
Надежная и устойчивая конструкция для работы персонала на промежуточном этаже без взаимодействия с гравиметрическим взвешиванием / системой контроля.
Лестницы для доступа к стеллажу накопителя.
В.7.1. Сеть распределения электропитания
Комплект кабелей для соединения каждого устройства повторного наполнения с кабиной управления.
Комплект кабелей для соединения каждого гравиметрического устройства с кабиной управления, включая специальный кабель для коммуникации.
Комплект кабельных желобов для соответствующей опоры при прокладке кабелей.
В.7.2 Сеть распределения сжатого воздуха
Комплект труб для соединения каждого устройства, установленного на платформе от отдельной питающей точки.
В комплекте с регулятором давления и воздушным фильтром.
СЕКЦИЯ С одновременно поворачивающийся двухшнековый экструдер
Поз. С.1 Одновременно поворачивающийся двухшнековый экструдер
С высокими эксплуатационными характеристиками, винтовой тип, находящийся в зацеплении для характеристик по самоочистке.
С.1.1. Опорная стальная сварная рама
Изготовлено из прочных сварных стальных пластин и профилей.
Предоставляется с уравнивающими болтами.
С.1.2 Бачок (емкость)
Модульное исполнение, изготовлено из 10 квадратных секторов емкости, каждый сектор длиной 4 D.
Корпус из секторов изготовлен из стали С-50 с внутренней сменной футеровкой, износостойкого сплава.
Встроенный водный контур охлаждения, простая конструкция и легкое обслуживание.
Система нагрева высокой эффективности – патронный нагреватель.
С.1.3 Комплект винтов
Прошивной вал из специального сплава – стойкий к повреждению/деформации/скручиванию.
Модульное исполнение.
Винтовые элементы
С.1.4. Редуктор
С. 1.5. Главный двигатель переменного тока
С.1.6. Установка водного охлаждения для экструзионного бачка (емкости)
Для подачи охлаждающей воды к каждому сектору бачка.
Включая циркулирующий насос.
Теплообменник вода/вода с расширительной камерой.
Соединяющий трубопровод.
С.1.7. Датчики температуры плавления и давления
Встроены в передний конец бачка.
Поз.С.2. Система вентиляции, включая:
вакуумный насос с водяным кольцом (система замкнутого контура, предложено в качестве опции)
вентилирующий свод
конденсатор дыма
промежуточный коллектор порошка
С.2.1. Дополнительная система вентиляции
Для отработанной излишней влажности от фильтров.
Естественная вентиляция (не вакуумный насос).
С.2.2. Специальная препятствующая закупориванию система для древесной муки
Двухвинтовое устройство для заталкивания обратно материала, который вылезает из бачка (емкости) из-за увеличения в объеме и давления пара.
Необходим для высокого процента фильтрации наполнителя или содержания высокой влажности.
Вакуумное отверстие установлено наверху на противоположном к винтам конце.
Винты сделаны из закаленной и шлифованной стали.
Стальной бачок с термообработкой.
Приводится от редукторного двигателя переменного тока.
Поз.С.3 Двухвинтовой боковой питатель
Винты, диаметр: 70 мм
Для подачи наполнителей в расплавленную пластмассу.
Двойные винты сцепленного типа.
Винты, изготовленные из закаленной и шлифованной стали.
Бачок (емкость) из закаленной стали с цепью водяного охлаждения.
Приводится от редукторного двигателя переменного тока, регулируемого цифровым частотным контроллером.
Поз. С.4 Редуктор 70
Для стабилизации линейного выхода и образования достаточного давления для питания головки пресс-формы без влияния на качества экструдера.
Специальное исполнение, подходящее для экструзии заполненных материалов.
Специальное износостойкое покрытие корпуса насоса и редукторов.
Редукторный двигатель 7, 5 кВт и универсальное соединение.
Зонд (щуп) давления плавления на входе/выходе.
Зонд (щуп) температуры плавления на выходе.
Зоны нагрева, вкл. основной кабинет (управления), специализированная система управления, соединенный с устройством контроля экструдера.
Опции для секции С
Поз.С.5 Замкнутый контур для вакуумного насоса
Желательно не тратить воду, и цеха для обработки воды нет.
Сепараторная емкость воздуха/воды встроена в опору насоса.
Встроенный теплообменник вода/вода.
Необходимо часто сменять воду (через 305 дней в зависимости от уровня загрязнения воды).
СЕКЦИЯ D пресс-формы и калибраторы
Поз. D.1. Пресс-форма профилей для насыпного материала профиля 60х60
D.1.1. Экструзионные пресс-формы для профилей
Соединение с редукторным насосом.
Встроенный, нержавеющая сталь.
Обогрев при помощи электрических нагревателей.
#5 терморегулируемых зон, вкл. главный кабинет.
D.1.2. Калибровочная группа профилей
Сухая и мокрая система.
Калибровочное устройство, открывающееся с помощью шарниров (петлей).
Изготовлено из нержавеющей стали.
D.1.3. Под вакуумными охлаждающими емкостями.
Изготовлено из 3 секций длиной 2 м.
2 секции с вакуумным кольцом.
1 секция только для охлаждения.
Изготовлено из алюминия и органического стекла (плексиглас).
Система охлаждения «полная вода (полностью водяная)».
Поз. D.2. Пресс-формы профилей насыпного материала в виде полу-пирамиды, профиль 70х60х45
D.2.1. Экструзионные пресс-формы для профилей
Соединение с редукторным насосом.
Встроенный нержавеющая сталь.
Обогрев при помощи электрических нагревателей.
#5 терморегулируемых зон, вкл. главный кабинет.
D.2.2. Калибровочная группа профилей
Сухая и мокрая система.
Калибровочное устройство, открывающееся с помощью шарниров (петлей).
Изготовлено из нержавеющей стали.
D.2.3. Под вакуумными охлаждающими емкостями.
Будет поставляться та же емкость охлаждения, как и для формы профилей 60х60
СЕКЦИЯ E Главный шкаф управления
Поз.Е.1 Главный шкаф управления
Система на основе ПЛК для контроля всей последовательности передвижения.
Интерфейс оператора с сенсорным экраном с цветным монитором.
# 18 зон температурного контроля (2 отдельные зоны для пресс-форм).
Зоны терморегуляции, встроенные в ПЛК.
Все системы кондиционирования.
Построен по стандартам ЕС.
Степень защиты: IP54.
Е.1.1. Удаленный пакет обновлений
Через промышленный LAN с доступом в Интернет.
ПО и техника на основе системы eWon.
Соединение с Интернетом, необходимое на поле со статичным IP адресом и открытым межсетевым экраном компании.
Е.1.2. Соединительные кабели
Соединительные кабели и коробы для прокладки кабеля от кабинета к экструдеру.
Панель управления, расположенный макс на расстоянии 3 м от экструдера.
СЕКЦИЯ F оборудование, расположенное ниже по технологической цепочке
Поз. F.1 Держатель калибровочного устройств
Для профилей с макс шириной: 150 мм
Длина опорного стола: 7 м
Продольное и высокое (наверное, осевое) смещение двигателями переменного тока.
Ручное поперечное смещение.
Сеть распределения охлаждающей воды с термометрами и регуляторами потока.
Центробежный насос 4 кВт для циркуляции воды.
200 л коллекторы для воды из нержавеющей стали.
Теплообменник вода/вода.
Вакуумная распределяющая сеть с вакуумметрами и регуляторами.
# 3 вакуумный насос 5,5 кВт.
Поз. F.2 Устройство отвода изделия из экструдера конвейерного.
Для макс ширины профиля 150 мм.
Стальная рама и алюминиевая конструкция держателя конвейера.
Плоский конвейер из специальной синтетической резины, стойкой к износу.
Приводной двигатель 1,5 кВт для каждого конвейера.
Пневматические цилиндры для верхнего открытия/закрытия конвейера, макс шаг 160 мм.
F.3. Устройство поперечной резки
Для макс ширины профиля 150 мм
Для макс высоты профиля 60 мм.
Стальная конструкция.
Лопасть из видиа, диаметр 400 мм.
Пневматический цилиндр для хода цилиндра вниз.
Приводной двигатель 1,5 кВт.
Устройства безопасности.
F.3.1. Устройство всасывания стружки
Металлическая конструкция для опоры тканевого воздушного фильтра и приемные полиэтиленовые мешки.
Всасывающий вентилятор из стали.
Макс мощность 2500 м3/ч.
F.4. Стенд / стан сборки для профиля разреза
Стальная структура с подвижными пластинами из алюминия.
Габариты пластины: 500х6000 мм.
Система бокового выталкивания с пневматическим приводом для передвижения профилей в /к приемной наклонной плоскости.
Опция 1. Оборудование для соэкструдированного отделочного слоя
Поз.Е.1. – Экструдер с одним винтом.
Винт, диаметр: 45 мм
Номинальное отношение длины к диаметру: 1:30
Макс скорость винта: 100 об в мин
Е.1.1 Опора стальной сварной рамы
Е.1.2. Бачок (емкость)
Изготовлено из азотированной стали LK3.
Обогрев керамическим обогревателем.
Система охлаждения электро-вентилятора.
Е.1.3. Винты
Изготовлено из азотированной стали LK3.
Е.1.4. Редуктор
Двигатель / коробка передач с помощью ремня и шкива.
Принудительная смазка.
Е. 1.5. Главный двигатель переменного тока
Е.1.6. Температура плавления и датчик давления
Поз. Е.2. Дополнительные инструменты для соэктсрудирования
Для пресс-форм для профилей из материала 60х60.
Экструзионная линия по производству профиля
Одношнековый экструдер 75 мм
Производительность: 60-90 кг/ч профиля (в зависимости от размеров и состава смеси)
Редуктор
Система подачи материала
- приводной двигатель: 1/2 л.с., с понижающим редуктором
- питатель: загрузка 50кг., нержавеющая сталь
Шнек
Цилиндр
Управление
- независимая панель управления
- семизонный температурный контроллер
*4 зоны для цилиндра с четырьмя воздуходувками
*1 зона для фланца
*2 зоны для экструзионной головки - инверторный контроль скорости
Калибровочный стол
Тянущее гусеничное устройство
- максимальный размер отреза ШхВ 200х60мм либо 120х100мм
- микрорегуляция скорости отреза
- контроль давления микрозажима
- пневмоконтроль пилы на соответствие скорости линии
- точный и регулируемый контроль длины
- двигатель 1 л.
с., диаметр пилы 14″
Пылесборник
- двигатель 3л.с.
- звукоуловитель
- мобильное исполнение
Полуавтоматический укладчик
- длина укладчика 3000мм со свайной структурой для сбора в стопки
- максимальная высота 1100мм
- выравнивание укладчика гидравлическое
- гидропривод ЛА л.с.
- настраиваемое пошаговое понижение уровня
Пресс-форма
Пресс-форма 25*25
- выход в 2 ручья
- экструзионная головка
- размерная форма 300Lх1компл., 50Lх1компл.
Пресс-форма 20*20
- выход в 2 ручья
- экструзионная головка
- размерная форма 300Lх1компл., 50Lх1компл.
Перфоратор
- двустороннее ударное (одновременно)исполнение
- линейная скорость 10м/мин
- контроль перфорации — инверторный
- 2 сменные головки
Станок для оклейки сеткой с автоматическим питателем
- система управления
- датчик контроля положения сетки
- резервуар термоплавкого клея с изоляцией, защищающей оператора от термических ожогов
Экструдер производительностью 1-12 кг/час
Характеристики экструдера:
- Производительность экструдера: 1 – 12 кг/час
- Входной материал необходимо определить
- Высота оси 1070 мм ± 100 мм
- Диаметр шнека и цилиндра 30 мм
- Экструдер оснащен загрузочным бункером
- Сторона управления будет указана после заказа
- Рама, цвет RAL 5012
- Щит управления, цвет RAL 7035
- Цилиндр горизонтальный и его невозможно перемещать по вертикали
Цилиндр:
- Внутренний диаметр 30 мм с допуском H7
- Обработка цилиндра – азотирование
- Три зоны нагрева.
Каждая зона охлаждается отдельно при помощи вентилятора с производительностью 150 м3/час
- Цилиндр охлаждается в нижней части бункера (заказчик заботится об охлаждающем средстве)
- Температура в нижней части бункера только измеряется и отображается. Эта температура не регулируется.
Шнек:
- Диаметр 30 мм
- Обработка шнека – азотирование
- Рабочая длина шнека 24 L/D
Двигатель экструдера:
- Конический редуктор с двигателем
- Мощность 5,5 кВт
- Напряжение 400/690 В
- Двигатель оснащен независимым охлаждением с мощностью 0,25 кВт
На панели управления экструдера возможно настроить следующие параметры:
- Ручное управления располагается на передней стороне щита управления
- На стороне щита управления будет сделан один служебный разъем 230В/16A/1Ф
- На панели управления экструдера можно настроить следующие характеристики:
- Число оборотов шнека 5 – 90 об / мин
- Старт/стоп экструдера
- Настройка температуры
Значения, отображаемые на дисплее экструдера:
- Температура и давление
- Число оборотов шнека
- Мощность двигателя при эксплуатации
- Температура в нижней части бункера
- Сигнализация
Безопасность:
- Центральная остановка
- Защита от давления (механическая) макс.
давление 6500 Psi (448 бар)
ПЕНОПЛЭКС 45 теплоизоляция для дорожного строительства
Описание
Высокоэффективный теплоизоляционный материал последнего поколения, изготавливаемый методом экструзии из полистирола общего назначения. Нулевое водопоглощение, высокая прочность, экологичность и низкая теплопроводность — основные преимущества утеплителя ПЕНОПЛЭКС® по сравнению с другими материалами.
Применение
Предназначен для использования в промышленном и гражданском строительстве, является высокопрочным материалом для применения в любых конструкциях, где предъявляются специальные требования по нагрузкам на конструктив. Материал ПЕНОПЛЭКС® 45 активно применяется в дорожном строительстве.
- — гражданском и промышленном строительстве
- — холодильной промышленности
- — автомобильном и железнодорожном строительстве
- — строительстве аэродромов
- — строительстве газопроводов и нефтепродуктопроводов
Плиты ПЕНОПЛЭКС 45.
Плиты предназначены для устройства теплоизоляционных слоев в конструкциях взлетно посадочных полос, автомобильных и железных дорог на вечномерзлых и пучинистых грунтах, а также для защиты от замерзания высоконагруженных полов, фундаментов, эксплуатируемых кровель, доступных автотранспорту. Прочность на сжатие при 10% деформации для этого типа плит составляет не менее 0,5 МПа, т.е. при распределенной нагрузке до 50 тонн на 1 м? материал не разрушается и его деформация по толщине составляет не более 10%.
Теплоизоляционные плиты ПЕНОПЛЭКС 45 производятся методом экструзии из полистирола общего назначения. Процесс экструдирования полистирола обеспечивает получение пеноматериала с однородной структурой, состоящей из мелких закрытых ячеек размером 0,1мм. — 0,2мм. В сочетании с водостойкими свойствами полистирола ячеистая структура обеспечивает чрезвычайно низкое водопоглощение материала, а так же высокую прочность на сжатие и низкую теплопроводность. Теплоизоляционные плиты ПЕНОПЛЭКС 45 рекомендуются использовать в диапазоне температур от — 50°С до + 75°С. В этом температурном режиме все физические и тепло-технические характеристики материала остаются неизменными. Теплоизоляционные плиты Пеноплекс 45 выпускаются в соответствии с ТУ 5767-00246261013-99.
Теплоизоляция труб с помощью экструдированного пенополистирола
Активно развивающимся направлением является применение материала ПЕНОПЛЭКС 45 в качестве теплоизоляции газо-нефтепроводов в условиях крайнего Севера
Применение трубной изоляции позволяет заменить надземную и полузаглубленную прокладку трубопровода на заглубленную (траншейную), что минимизирует тепловое воздействие трубопровода на вечномерзлые грунты в условиях крайнего Севера. Это позволяет предотвратить растепление грунтов и возможную деформацию трубопровода. Следует отметить, это в два раза сокращается объем земляных работ по созданию песчаной подсыпки, уменьшается срок строительства газопровода и увеличивается его рабочий ресурс.
Теплоизоляция нефтепроводов
Данный вид теполизоляции значительно снижает затраты по их эксплуатации, т.к. сводит к минимуму возможность временного выхода из строя нефтепровода из-за влияния низких температур на нефть (особенно в случаях высокой парафинизации).Теплоизоляция трубопродоводов Надежная теплоизоляция водопроводов, водозаборных сооружений, систем канализации и теплотрасс. Благодаря высокой механической прочности материал не требует
дополнительной внешней защиты (кожухов). Защита трубопроводов от механических повреждений
Высокие прочностные характеристики
Обеспечивают надежную защиту трубопроводов от механических повреждений, в том числе острых скалистых пород. Примером может служить строительство газопровода Голубой поток, где сегменты из экструзионного пенополистирола применены для защиты газопровода на участках активных тектонических разломов.

Имеет все необходимые сертификаты и рекомендована к использованию Госгортехнадзором России, Госстроем России RU.СЛ42.Н00024. АО ВНИИСТ и ООО ВНИИГАЗ разработали, а ОАО ГАЗПРОМ согласовало ТУ 5767-001-01297858-02 на тепловую изоляцию для трубопроводов диаметром от 57 мм до 1420 мм. По согласованию с заказчиком наша компания может изготовить теплоизоляцию для трубопроводов любых диаметров и типоразмеров.
Пример условных обозначений элементов изоляции :
Единица измерения – погонные метры.
ПЕНОПЛЭКС 45 ПЦ-1250.80.30 – ТУ 5767-001-01297858-02, где:
45 – марка (средняя плотность материала) полуцилиндра
ПЦ – наименование изделия – полуцилиндр
1250 – длина изделия, мм
80 – внутренний диаметр полуцилиндра, мм
30 – толщина полуцилиндра, мм
Плиты ПЕНОПЛЭКС упаковывают в полиэтиленовую пленку с защитой от проникновения УФ лучей. Высота упаковки 40-42 см с количеством плит от 4 до 17 шт. Объем одной упаковки плит типа пеноплекс 45 – от 0,576 до 1,134 м? в зависимости от длины.
Для получения более подробной информации о материалах позвоните по телефону 8 800 200 97 78, или напишите нам письмо (в разделе контакты.
Технические характеристики пеноплекс 45:Плотность | ГОСТ 17177-94 | кг/м? | 38,1-45,0 |
Прочность на сжатие при 10% линейной деформации, не менее | ГОСТ 17177-94 | МПа (кгс/см2; т/м2) | 0,50 (5; 50) |
Предел прочности при статическом изгибе, не менее | ГОСТ 17177-94 | МПа | 0,4-0,7 |
Модуль упругости | СОЮЗДОРНИИ | МПа | 18 |
Водопоглощение за 24 часа, не более | ГОСТ 17177-94 | % по объему | 0,2 |
Водопоглощение за 30 суток |
| % по объему | 0,4 |
Категория стойкости к огню | СНиП 21-01-97 | группа | Г4 |
Коэффициент теплопроводности (25±5) °С | ГОСТ 7076-94 | Вт/(м?°С) | 0,030 |
Расчетный коэффициент теплопроводности при условиях эксплуатации «А» | СП 23-101-2004 | Вт/(м?°С) | 0,031 |
Расчетный коэффициент теплопроводности при условиях эксплуатации «Б» | 0,032 | ||
Теплоусвоение при условиях «А» (при периоде 24 часа) | 0,35 | ||
Теплоусвоение при условиях «Б» (при периоде 24 часа) | 0,36 | ||
Коэффициент паропроницаемости | ГОСТ 25898-83 | мг/(м?ч?Па) | 0,007 |
Удельная теплоемкость, со | СП 23-101-2004 | кДж/(кг?°С) | 1,40 |
Звукоизоляция перегородки (ГКЛ-ПЕНОПЛЭКС® 50 мм-ГКЛ), Rw | ГОСТ 27296-87 | дБ | — |
Индекс улучшения изоляции структурного шума в конструкции пола | ГОСТ 16297-80 | дБ | — |
Технология производства пенопласта (пенополистирола) — ООО «ПК ВикРус»
Главная / Технология производства пенопласта (пенополистирола)Содержание:
- Предварительное вспенивание гранул.
- Кондиционирование предварительно вспененных гранул.
- Формование пенополистирольных блоков.
- Кондиционирование пенополистирольных блоков.
- Разрезание пенополистирольных блоков на плиты.
- Использование пенополистирольных отходов.
1. ПРЕДВАРИТЕЛЬНОЕ ВСПЕНИВАНИЕ
1.1. Краткая характеристика сырья
В качестве сырья используется вспениваемый самозатухающий полистирол, содержащий 5-6% смеси пентана и изопентана, являющейся вспенивающим фактором. Эта смесь содержится в гранулах полистирола в растворенном виде.
Сырье имеет вид гранул, получаемых путем суспензионной полимеризации стирола. Оно содержит вещество, снижающее горючесть -антипирен.
После подогрева до температуры 90-100°С, под действием улетучивающегося пентана гранулы увеличивают свой объем (процесс вспенивания) примерно в 30-65 раз. В промышленной практике для вспенивания полистирола используется водяной пар, который проникает также внутрь гранул и способствует действию пентана.
Международное обозначение вспениваемого полистирола: EPS самозатухающий FS.
Хранение:
Хранить исключительно в заводской, плотно закрытой таре или контейнерах, установленных в проветриваемых помещениях или под навесом, далеко от источников тепла и огня. Рекомендуется хранить сырье при температуре, не превышающей 20°С.
Продукт, хранимый при рекомендуемой температуре, следует использовать не позднее 3-6 месяцев с даты исследования продукта, указанной в сертификате качества. Продукт из частично опорожненной или поврежденной тары следует использовать немедленно.
В производственных помещениях можно хранить сырье в количестве, не превышающем его среднесуточный расход.
1.2. Переработка вспениваемого полистирола .
Окончательная плотность готового продукта определена уже на этапе предварительного вспенивания.
Важным показателем является контроль давления при процессе вспенивания, для непрерывных предвспенивателей 0,015-0,03 МПа, для циклических 0,015-0,02 МПа.
Во вспенивателе два способа изменения мнимой плотности продукта:
- путем изменения количества подаваемого сырья;
- путем изменения уровня вспениваемого материала в рабочей камере;
Первый и второй способ оказывают влияние на время нахождения вспениваемого материала в рабочей камере. Третий способ влияет на температуру в камере.
Влияние времени нахождения сырья во вспенивателе на мнимую плотность продукта представлено на рис.1.2.
Если время нахождения сырья во вспенивателе слишком продолжительно, то гранулы начинают усаживаться и плотность растет; при слишком высокой температуре вспененные гранулы могут образовать комки. Оба эти явления могут происходить одновременно. И оказывать непосредственное влияние на качество конечного продукта.
Плотность
Продолжительность предварительного вспенивания
Рис.1.2. Зависимость между мнимой плотностью и продолжительностью вспенивания
С целью получения низкой плотности (< 12 кг/м3) применяют двухступенчатое вспенивание. Двухступенчатое вспенивание проводят с помощью того же самого оборудования, которое используется для одноступенчатого вспенивания, с подачей предварительно вспененного сырья через систему вторичного вспенивания.
С целью достижения оптимальных результатов вспенивания гранулы перед вспениванием второй ступени должны быть насыщены воздухом (процесс кондиционирования).
Предварительно вспененные гранулы поступают в сушилку с кипящим слоем, в которой теплый воздух (темп. примерно 30-40°С) проходит через перфорированное днище сушилки, сушит и продвигает гранулы в направлении выгрузочного вентилятора.
Воздушная струя должна распределяться таким образом, чтобы процесс сушки и перемещения гранул протекал равномерно по всей длине сушилки (регулировка осуществляется с помощью заслонок в воздушных камерах сушилки).
Одним из чрезвычайно важных факторов, оказывающих влияние на вспенивание полистирола, является продолжительность хранения сырья. Чем старше сырье, тем продолжительнее вспенивание и тем труднее достичь требуемой мнимой плотности вспененных гранул. Поэтому срок хранения сырья в герметичной упаковке ограничен до шести месяцев.
1.3. Техническое оснащение узла предварительного вспенивания
a) вспениватель ВП-03
b) система вторичного вспенивания СВВ-1
c) поточная сушилка гранул СС-106
d) выгрузочный вентилятор ВПВ-2,5
2. КОНДИЦИОНИРОВАНИЕ ПРЕДВАРИТЕЛЬНО ВСПЕНЕННЫХ ГРАНУЛ
2.1. Основы процесса кондиционирования гранул
В ходе кондиционирования воздух проникает внутрь вспененных гранул вследствие образовавшегося в них вакуума, а из вспененных гранул в атмосферу выпускается влага в виде пара и пентан, не прореагировавшие остатки процесса полимеризации сырья. Указанный газообмен возможен благодаря газопроницаемости полистироловых оболочек.
Рис.2.1. Гранулы вспениваемого полистирола в процессе кондиционирования
Скорость диффузии воздуха внутрь гранул обусловлена, главным образом, мнимой плотностью, температурой окружающей среды и размером гранул. Целью удаления влаги с поверхности гранул в сушилке с кипящим слоем является получение 100% мнимой поверхности, через которую осуществляется газообмен.
Скорость испарения пентана также зависит от плотности, температуры окружающей среды и размера гранул. Из крупных гранул пентан испаряется медленнее, чем из гранул малого диаметра, что обусловлено соотношением между поверхностью гранулы и ее массой.
2.2. Техническое оснащение узла кондиционирования гранул
Силосы, используемые для кондиционирования вспененных гранул, изготовляются в виде легкой металлической конструкции стеллажного типа с контейнерами из ткани, пропускающей воздух.
При перемещении вспененных гранул с помощью струи воздуха, на поверхности гранул накапливаются сильные электростатические заряды. Поэтому чрезвычайно важно тщательно заземлить все металлические элементы силосов, транспортных трубопроводов и остального оборудования.
2.3. Параметры кондиционирования гранул
Температура окружающей среды в цехе кондиционирования гранул не должна быть ниже 15°С, при более низкой температуре продолжительность кондиционирования увеличивается. В летний период, при температуре свыше 20°С время кондиционирования сокращают, а при более низких температурах — продлевают.
При транспортировке свежих гранул в силосы, их мнимая плотность увеличивается в результате столкновений со стенками трубопровода. Поэтому при установке параметров вспенивания необходимо учитывать увеличение плотности при транспортировке.
3. ФОРМОВАНИЕ ПЕНОПОЛИСТИРОЛЬНЫХ БЛОКОВ
3.1. Характеристика процесса формования
При выработке блоков вспененные гранулы свободно засыпают в камеру формы до ее полного наполнения. Затем в форму подают насыщенный сухой водяной пар под давлением 0,2-0,4 МПа, что приводит к дальнейшему увеличению объема гранул. В связи с тем, что гранулы находятся в закрытой камере, сначала заполняется свободное пространство между ними, а затем гранулы сцепляются друг с другом.
Рис.3.1.1. Пример фазового цикла формования блоков без использования вакуума1) наполнение 2) продувание 3) запаривание 4) охлаждение 5) расформовка
Рис.

1) наполнение 2) вакуум 3) продувание 4) запаривание — рост | 5) запаривание — выдержка 6) выпуск 7) вакуумное охлаждение 8) разгрузка |
Важным фактором при запаривании блока является подача в камеру в свободное пространство между гранулами соответствующего количества пара в кратчайшее время. Для этого необходима соответствующая вентиляция (продувание), целью которой является удаление воздуха перед началом процесса запаривания. Недостаточная продолжительность продувания приводит к неоднородной плотности и плохому спеканию блока.
Важно также поддерживать постоянную высокую температуру формы, в противном случае значительно растет расход пара (рис.3.1.3) и пар становится мокрым, что снижает качество сцепления гранул.
Рис.3.1.3. Примерный расход пара в зависимости от температуры формыДавление, которое блок оказывает на внутренние стенки формовочной камеры, составляет примерно 0,08 МПа.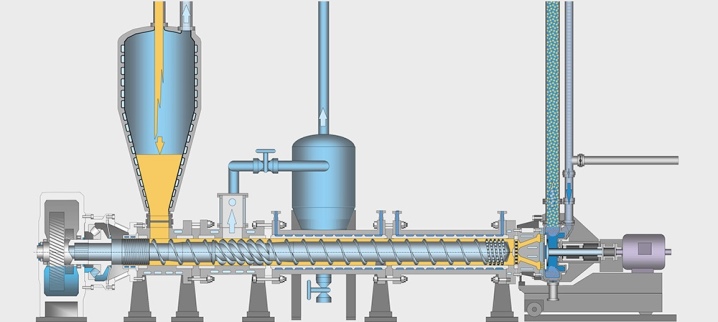
3.2. Техническое оснащение узла формования
a) блок форма УЦИП 1030.
b) установка вакуумирования ВУ-3,3 с аккумулятором вакуума АВ-1.
c) система вакуумной загрузки и охлаждения блоков.
d) компрессорная установка СБ4/Ф-500
e) аккумулятор пара ПН-5000
f) котел паровой
4. КОНДИЦИОНИРОВАНИЕ БЛОКОВ
4.1. Краткая характеристика процесса кондиционирования блоков
После окончания процесса формования блоки кондиционируют. Кондиционирование проводится с целью снижения влажности и устранения внутренних напряжений, возникающих при формовании. Кроме того, при этом протекают процессы диффузии газов и выравнивания давления внутри гранул с атмосферным давлением, подобные процессам, происходящим при кондиционировании предварительно вспененных гранул.
В процессе кондиционирования блоков очень важную роль играет очередность их использования, соответствующая очередности формования, то есть при отборе блоков для разрезания следует начинать с самых «старых».
5. РАЗРЕЗАНИЕ ПЕНОПОЛИСТИРОЛОВЫХ БЛОКОВ НА ПЛИТЫ
5.1. Характеристика процесса резки пенополистирола
Разрезание блоков осуществляется с помощью реостатной проволоки, нагретой до соответсвующей температуры.
Все отходы подаются в измельчитель, откуда в измельченном виде пневматически транспортируются на вторичное использование.
5.2. Требования по качеству
Внешний вид
Окраска пенополистироловых плит должна быть такой же, как окраска предварительно вспененных гранул полистирола.
Необходимо проводить выборочную проверку плит — по крайней мере 2 шт. на длине каждого блока.
Если плиты отвечают предъявляемым требованиям, то после укладки в стопки они направляются на упаковку.
Если отклонение от требуемых размеров превышает допустимую величину, то следует еще раз проверить по одной плите на всей длине блока, определить причину, произвести соответствующую корректировку промежутков между отрезками реостатной проволоки.
Проверить таким же образом размеры плит, полученных в результате разрезания следующего блока.
Плиты, которые не отвечают предъявляемым требованиям, направляются на вторичное использование.
6. ИСПОЛЬЗОВАНИЕ ПЕНОПОЛИСТИРОЛЬНЫХ ОТХОДОВ
Отходы используется вторично в производстве блоков.
6.1. Техническое оснащение узла
a) дробилка пенополистирольных отходов
b) технологический силос
6.2. Система измельчения
Устройство предназначено для измельчения пенополистироловых отходов, в результате чего получают крошку, используемую в качестве добавки к гранулам полистирола при производстве пенополистироловых блоков. Размеры получаемой таким образом крошки составляют до 15 мм.
Интересно? Оставьте закладку, что бы вернуться сюда позже!
Пенополистирол
EPS – Coperion
Вспенивающийся полистирол (EPS) представляет собой жесткий и прочный пенопласт. EPS часто используется для упаковки пищевых продуктов, строительной изоляции и упаковочного материала либо в виде твердых блоков, сформированных для размещения защищаемого предмета, либо в виде сыпучих гранул, амортизирующих хрупкие предметы внутри коробок.
Проверенная временем первоклассная технология Coperion и Coperion K-Tron оптимально подходит для одностадийного производства пенополистирола.Чрезвычайно надежные гравиметрические питатели Coperion K-Tron обеспечивают высокую точность подачи при добавлении в процесс GPPS, EPS, наполнителей, антипиренов, зародышеобразователей, цветных пигментов или пенообразователей. Благодаря интенсивному смешиванию и очень щадящей обработке продукта двухшнековые экструдеры ZSK обеспечивают оптимальное распределение всех ингредиентов. Микрогранулы создаются с помощью подводного гранулятора, а затем расширяются или формуются.
Подробнее Читать меньше
Основные преимущества:
- Компактная конфигурация системы
- Гибкое производство по рецепту
- Регулируемый размер гранул
- Повышение качества продукции благодаря двухшнековому компаундированию
- Высокоточная подача основных ингредиентов
- Доступна полная конструкция ATEX
- Доступна полностью защищенная от коррозии технологическая секция
Типовая установка для одностадийного производства вспенивающегося полистирола (EPS)
Полный ассортимент продукции
Машины для производства компаундов и экструдеры
Компания Coperion предлагает двухшнековые экструдеры ZSK и STS с однонаправленным вращением. Обе линии экструдеров обеспечивают плавное взаимодействие этапов процесса и бережное обращение с продуктом с максимальной производительностью.
Оборудование для кормления
Питатели Coperion K-Tron обеспечивают непрерывную равномерную подачу с очень высокой кратковременной точностью и повторяемостью.В зависимости от сырья и технологических требований доступны различные модели и конфигурации питателей. Вибрационные питатели, одношнековые питатели или насосы для сыпучих материалов для сыпучих материалов, таких как грануляты и пеллеты, двухшнековые питатели для сложных порошков, таких как наполнители, антипирены, пигменты или другие добавки, а также дозаторы жидкости и другие специальные питатели — это лишь некоторые из технологий, доступных для разработки правильного решения для каждого применения.
Погрузочно-разгрузочное оборудование
Coperion и Coperion K-Tron разработали широкий спектр решений для обработки материалов для производства пенополистирола.Наши проекты включают в себя полный спектр решений: компоненты для хранения и разгрузки материала, пневматические и механические системы транспортировки, системы взвешивания и подачи, а также комплексные системы управления технологическим процессом. Решения для транспортировки могут использовать давление или вакуум, бедную или плотную фазу, в зависимости от характеристик материала и свойств применения. Разгрузку материалов можно осуществлять с грузовиков, силосов, BBU (разгрузчиков больших мешков) на станции выгрузки мешков (маленькие мешки) и в перчаточные ящики для токсичных или опасных материалов. В зависимости от свойств материала и требований мы рады интегрировать в наши системы другие функции, такие как удаление комков, просеивание или другое оборудование, зависящее от вашего процесса.
Установки и системы
Компания Coperion предлагает комплексные системы, включающие в себя весь наш опыт в области обработки материалов, подачи, компаундирования и экструзии.При планировании и установке установки по производству компаундов у вас есть только одно контактное лицо, и вы получаете выгоду от четко определенной ответственности за проект.
Глобальная служба
Наша сервисная структура состоит из более чем 350 сервисных инженеров и техников по всему миру, которые заботятся не только о ваших машинах и системах, но и о вашем бизнесе. Они видят себя партнерами, которые обеспечивают ваше будущее.
загрузок
Посмотреть больше загрузок Меньше загрузок
Хотите узнать больше об одностадийном производстве пенополистирола?
Связаться с намиКитай производитель XPS, линия для XPS, поставщик листов XPS
Компания «Green Earth®» является одним из ведущих разработчиков и производителей оборудования для производства экструдированного пенополистирола в Китае, основана в 2005 году. «Зеленая Земля®» — это команда специалистов, состоящая из специалистов различных отраслей, опытных производственников, инженеров, ученых.
Производственные мощности компании расположены в …
Компания «Green Earth®» — один из ведущих разработчиков и производителей оборудования для производства экструдированного пенополистирола в Китае, основана в 2005 году.«Green Earth®» — это команда специалистов, состоящая из специалистов различных отраслей, опытные производственники, инженеры, ученые.
Производственные мощности компании расположены в городе Шицзячжуан провинции Хэбэй. В компании работает 96 человек. Площадь производства составляет 39 600 квадратных метров.
Директор-основатель компании — профессор Пекинского химико-технологического университета, где он преподает технологию вспенивания полимеров. Компания имеет собственную лабораторию на базе университета, где постоянно ведутся исследования и разработки по совершенствованию оборудования и технологий.Благодаря этой работе компания накопила большой положительный опыт и получила ряд патентов на изобретения в области технологии экструзии.
Также компания придает особое значение сохранению окружающей среды и снижению вредных выбросов, использованию в производстве вторичного сырья. Компания «Green Earth®» Входит в состав официальных представителей Китая в ООН по программе защиты окружающей среды. В рамках этого участия компания представила запатентованную технологию производства полностью «Зеленой» плиты XPS без использования дополнительных вредных для окружающей среды пенообразователей.Эксперты ЮНЕП дали высокую оценку этим разработкам, что подтверждено сертификатами этой организации.
«Green Earth®» Оборудование производится с использованием европейских комплектующих. Производимое оборудование соответствует высоким стандартам качества. «Green Earth®» дает гарантию не только на свое оборудование, но и на результат своей работы, на качество производимого экструдированного пенополистирола.
Эксклюзивный дилер «Green Earth®» В России и СНГ:
ООО «Астерол»
Россия, г. Томск, м.ул. Горького, 66
Тел/факс: +7 (3822) 592-100
Web: www. asterol.ru
Пенопласт
Существует 3 основных жестких пенопластовых материала, обычно используемых для изоляции жилых, коммерческих и промышленных объектов: экструдированный полистирол (XPS), вспененный полистирол (EPS), полиуретан (PUR/PIR). Каждый тип имеет индивидуальные характеристики и определенные преимущества и недостатки для конкретных применений в строительстве. Пены рекомендуются для мест, где требуются высокие механические свойства и малый вес.
Мы предлагаем 3 вида изделий из пенопласта; все они обладают отличными изоляционными характеристиками:- EPS, пенополистирол
- XPS, экструдированный полистирол
- PUR/PIR, полиуретан
Пенополистирол (EPS) | Экструдированный полистирол (XPS) | Полиуретан (PUR/PIR) |
Пенополистирол — это легкий, жесткий изоляционный материал из пенопласта с закрытыми порами, изготовленный из твердых шариков полистирола.![]() | Экструдированный полистиролотличается высокой устойчивостью к давлению и влаге. Он производится методом непрерывной экструзии: гранулы полистирола расплавляются в экструдере, и в экструдер под высоким давлением впрыскивается вспениватель, где он растворяется в расплаве полистирола.Основным используемым вспенивающим агентом является CO2. В результате непрерывного процесса экструзии получается вспененный продукт с однородной структурой с закрытыми порами и гладкой непрерывной оболочкой. | Полиуретан — это общий термин, который охватывает широкий спектр различных составов, полученных в результате химической реакции диизоцианата с полиолом. Полиуретановая изоляция относится к группе изоляционных материалов на основе PUR (полиуретан) или PIR (полиизоцианурат).![]() Дополнительная информация |
Подготовка к устойчивому производству
Sulzer поддерживает круговую стратегию EPS BEWiSynbra Group
Автор: Дорота Золдосова, руководитель отдела маркетинга и коммуникаций, Sulzer Chemtech Ltd.
Компания Sulzer Chemtech завершила проектирование, монтаж и запуск передовой производственной линии для вспенивающегося полистирола (EPS) для группы BEWiSynbra. Компания является одним из ведущих производителей пенополистирола в Европе, и новое подразделение будет поддерживать ее амбициозную цель по сбору и переработке 60 000 тонн пенополистирола в год, используя переработанные материалы в качестве сырья.
Компания Sulzer, лидер в области технологий разделения и смешивания, поставила современную линию по производству пенополистирола на предприятие группы BEWiSynbra в Порвоо, Финляндия. В новой установке используется запатентованная компанией Sulzer технология пропитки расплавом на основе экструзии, и она способна производить более 10 000 тонн пенополистирола в год как из переработанных, так и из первичных материалов.
Производственная линия способна производить более 10 000 тонн пенополистирола для монтажа и упаковки зданий в год как из переработанных, так и из первичных материалов.
Новый актив поможет BEWISynbra Group расширить свои производственные мощности по производству пластмасс, а также позволит достичь поставленных целей в области экономики замкнутого цикла. Производственная линия может преобразовывать бытовые отходы пенополистирола в новый материал пенополистирол, используемый в таких областях, как изоляция зданий или упаковка.
Йонас Сильескар, генеральный директор BEWiSynbra Group, комментирует: «Новая линия экструдеров EPS, разработанная и поставленная Sulzer, позволяет BEWISynbra расширить свой ассортимент EPS. Это позволяет нам увеличивать объем перерабатываемых материалов, одновременно повышая эффективность производства, а также снижая затраты на ремонт и техническое обслуживание».
Филипп Зюсс, глава Sulzer Chemtech ERA, заключает: «Приятно видеть, что наши решения играют ключевую роль в повышении конкурентоспособности наших клиентов, а также в поддержке их амбициозных методов устойчивого развития. Мы надеемся на сотрудничество с BEWiSynbra Group в будущем».
О Зульцер
Компания Sulzer является мировым лидером в области гидродинамических технологий. Мы специализируемся на технологиях перекачивания, перемешивания, смешивания, разделения и применения жидкостей всех типов.Наши клиенты получают выгоду от нашей приверженности инновациям, производительности и качеству, а также от нашей гибкой сети из 180 производственных предприятий и сервисных центров мирового класса по всему миру. Штаб-квартира Sulzer находится в Винтертуре, Швейцария, с 1834 года. В 2019 году наши 16 500 сотрудников принесли доход в размере 3,7 млрд швейцарских франков. Наши акции торгуются на SIX Swiss Exchange (SIX: SUN).
Подразделение Chemtech является мировым лидером в области инновационного массопереноса, статического смешивания и полимерных решений для нефтехимии, нефтепереработки, СПГ, биополимеров и биотоплива. Ассортимент нашей продукции варьируется от технологических компонентов до комплексных технологических установок разделения, включая лицензирование. Поддержка клиентов включает инженерно-технические услуги и выездные услуги по установке тарелок и уплотнений, техническому обслуживанию башни, сварке и капитальному ремонту завода.
www.sulzer.com
Патент США на способ производства пенополистирола с добавками для обработки полимеров Патент (Патент № 10,059,822, выдан 28 августа 2018 г.)
РОДСТВЕННЫЕ ЗАЯВКИЭто приложение является выделенным приложением U.С. Сер. № 11/259970, поданной 27 октября 2005 г. под названием «МЕТОД ПРОИЗВОДСТВА ПЕНОПОЛИСТИРОЛА С ДОБАВКАМИ ДЛЯ ПЕРЕРАБОТКИ ПОЛИМЕРОВ», полное раскрытие которого включено в настоящий документ посредством ссылки.
ССЫЛКА НА ПРАВА ГОСУДАРСТВА Это изобретение было сделано при поддержке правительства в рамках Программы передовых технологий (ATP) Грант № 70NANB2h4023, присужденный Национальным институтом стандартов и технологий (NIST). Правительство может иметь определенные права на это изобретение.
Изобретение относится к способам получения пенополимеров, в частности к производству пенополистирола (ЭПС) в отсутствие хлорфторуглеродов и фторуглеродных пенообразователей с использованием одного или нескольких сложных эфиров, в частности адипинатов, бензоатов и дибензоаты в качестве вспомогательных средств для обработки полимеров (PPA) для улучшения внешнего вида и свойств получаемой пены, и, более конкретно, в процессах получения изделий из экструдированного пенополистирола из смесей полистирола с использованием диоксида углерода в качестве основного вспенивателя.
Изобретение относится к композициям и способам производства плит из экструдированного пенополистирола (XPS), пригодных для применения в качестве изоляционных материалов, в частности, для системы наружной отделки изоляции (EIFS) для строительства зданий.
ПРЕДПОСЫЛКИ СОЗДАНИЯ ИЗОБРЕТЕНИЯ При традиционном производстве пенополистирола (ПС) с использованием процесса экструзии в качестве пенообразователей обычно использовали один или несколько галоидоуглеводородов, таких как метилхлорид, этилхлорид, хлоруглероды, фторуглероды (включая ГФУ ) и хлорфторуглероды (ХФУ), включая дихлордифторметан, фторуглеводороды или хлорфторуглеводороды (которые также называются «мягкими ХФУ», «ГХФУ» или «ГФУ»). Примеры таких галоидоуглеводородов включают ряд CFC, таких как CFC-11 (хлортрифторметан), CFC-12 (дихлордифторметан) и CFC-113 (1,2,2-трифтор-1,1,2-трихлорэтан), и гидрогалогенуглероды, также называемые «мягкими» ХФУ, ГХФУ и ГФУ, включая ГХФУ-22 (хлордифторметан), ГХФУ-123 (1,1-дихлор-2,2,2-трифторэтан), ГХФУ-142b (1-хлор- 1,1-дифторэтан), HFC-134a (1,1,1,2-тетрафторэтан), HFC-152a (1,1-дифторэтан) и HCFC-141b (1,1-дихлор-1-фторэтан.
Общая процедура, используемая при получении экструдированных изделий из синтетических пенопластов, обычно включает стадии плавления базовой полимерной композиции, введения в расплав полимера одного или нескольких вспенивателей и других добавок в условиях, обеспечивающих тщательное смешивание вспенивателя и полимер, предотвращая преждевременное вспенивание смеси, т.е.г., под давлением. Затем эту смесь обычно экструдируют через одноступенчатую или многоступенчатую экструзионную головку для охлаждения и снижения давления на смесь, позволяя смеси вспениваться и производить вспененный продукт. Понятно, что относительные количества полимера(ов), пенообразователя(ей) и добавок, температура и способ снижения давления имеют тенденцию влиять на качество и свойства полученного продукта из пенопласта.
Растворимость хлорфторуглеродов и некоторых алканов в полистироле снижает вязкость экструзионного расплава и улучшает охлаждение расплавов пенополистирола (ПС).Например, комбинация пентана и хлорфторуглерода, такого как фреон 11 и 12, частично растворима в полистироле и использовалась для получения пенополистирола, который демонстрировал в целом приемлемый внешний вид и физические свойства, такие как отделка поверхности, размер и распределение ячеек, ориентация, усадка и жесткость.
Однако в связи с очевидным вкладом таких соединений ХФУ в уменьшение озонового слоя в стратосфере Земли широкое использование и сопутствующий выброс в атмосферу таких соединений в таких областях, как аэрозольные пропелленты, хладагенты, пенообразователи и специальные использование растворителей недавно было резко сокращено или исключено в соответствии с постановлением правительства. Хотя некоторые из «мягких» ХФУ, такие как некоторые гидрофторуглероды (ГФУ), в том числе 1,1,1,2-тетрафторэтан (ГФУ-134а) и 1,1-дифторэтан (ГФУ-152а), считаются гораздо более безопасными для озона и рассматривались как альтернативные пенообразователи. Однако эти альтернативные соединения дороги, как правило, менее растворимы в полистироле, имеют более высокую теплопроводность, чем ГХФУ, и все же могут способствовать глобальному потеплению.
Углеводороды, такие как пентан, гексан, циклопентан и другие гомологи этого ряда, также рассматривались, но они являются легковоспламеняющимися и летучими, что вызывает опасения как по поводу безопасности, так и по выбросам летучих органических соединений.Углекислый газ является привлекательным кандидатом в качестве пенообразователя как с экологической, так и с экономической точек зрения. Проблемы, связанные с успешным использованием СО 2 в качестве пенообразователя, однако, являются значительными в свете относительно низкой растворимости, высокой диффузионной способности и плохой технологичности СО 2 в полистирольных смолах. CO 2 также имеет повышенную теплопроводность по сравнению с ГХФУ-142b и ГФУ-134а, при этом пенопласт CO 2 демонстрирует примерно на 17 % и примерно на 10 % более низкие значения общей изоляции продукта, соответственно, по сравнению с соответствующими пенами, произведенными с использованием ГХФУ. -142b и ГФУ-134а.
В других предыдущих попытках использовались спирты, такие как этанол, или углеводороды, такие как циклопентан, в сочетании с CO 2 для улучшения технологичности и обеспечения производства плит из экструдированного пенополистирола с желаемыми или целевыми физическими и термическими свойствами. Проблемы со вспенивателями, такими как спирты или углеводороды, заключаются в их воспламеняемости, безопасности и негативном влиянии на характеристики воспламенения и изоляционные свойства конечного продукта.
Обычные процессы включают процессы полимерной пены для изготовления термоформованных изделий, в которых вспенивающий агент представляет собой смесь, по крайней мере, атмосферного газа и, по крайней мере, одного летучего пластифицирующего вспенивающего агента. Предыдущие попытки смешать обычно жидкие углеводороды и обычно газообразные вспенивающие агенты, как правило, имели лишь ограниченный успех и, как правило, требовали большой осторожности для получения приемлемых полимерных пен с использованием легколетучих вспенивающих агентов, таких как диоксид углерода.
Задачи настоящего изобретения включают разработку усовершенствованного способа получения полимерных пенопластов с использованием одного или нескольких атмосферных газов в качестве вспенивателя в сочетании по меньшей мере с одним сложным эфиром, в частности адипиновым эфиром, в качестве средства обработки полимера. помогать.
В иллюстративном варианте осуществления изобретения экструдированные пенополистирольные пенопласты получают из расплава полимера, который обычно включает полистирол с высокой текучестью расплава в качестве основного полимерного компонента, атмосферный газ, такой как CO 2 , в качестве основного вспенивателя и по меньшей мере одну полимерную технологическую добавку, выбранную из группы сложных эфиров, особенно адипинатов, имеющих структуру бис(nR), где R является алифатическим (линейным, циклическим и разветвленным, насыщенным и ненасыщенным) или ароматическим, причем предпочтительным адипатом является бис(н-деканил ) адипат.
В примерном варианте осуществления изобретения расплав полимера будет приготовлен из основной части одного или нескольких стирольных полимеров, которые имеют высокий индекс расплава, например, индекс расплава по меньшей мере около 10,0 (г/10 минут) ( измерено в соответствии с ASTM D 1238, условие L), в сочетании с не более чем примерно 5 мас. % бис(н-деканил)адипата в качестве добавки для обработки полимера и менее чем примерно 4 мас. % СО 2 в качестве пенообразователя ,
В примерном варианте осуществления изобретения расплав полимера будет приготовлен из предварительно полученных стирольных полимеров или сополимеров, которые могут быть предварительно смешаны с бис(н-деканил)адипатом.В качестве альтернативы или дополнительно бис(н-деканил)адипинат можно впрыскивать непосредственно в полимерный расплав в промежуточном положении на пути шнекового экструдера. В дополнение к бис(н-деканил)адипату в предварительно полученные стирольные полимеры могут быть включены другие технологические добавки или их можно вводить в расплав по мере его прохождения через экструдер. Вспенивающий агент(ы), такой как CO 2 , также вводят в полимерный расплав в промежуточной части по ходу шнекового экструдера.В любом случае каждая добавка и вспенивающий агент(ы) должны быть введены в расплав полимера на достаточно высоком уровне перед экструзионной головкой, чтобы обеспечить достижение адекватного смешивания до того, как композиция достигнет экструзионной головки.
В соответствии с изобретением способ изготовления пенополистирола включает смешивание атмосферного газа, такого как диоксид углерода, азот или воздух, и по меньшей мере одного нелетучего смешивающего агента с расплавом полистирола. Расплав полистирола может также включать один или несколько зародышеобразователей, таких как тальк, бикарбонат натрия или лимонная кислота.Затем смесь расплава полистирола, атмосферного газа и смешивающего агента выбрасывается через экструзионную головку, тем самым снижая давление и позволяя вспенивающему агенту расширяться и образовывать пенополистирол. В зависимости от концентрации пенообразователя и условий экструзии полученная пена может практически не иметь остаточного пенообразователя и будет демонстрировать приемлемые свойства пены и поверхности.
Примеры вариантов осуществления изобретения будут очевидны из более подробного описания некоторых примеров вариантов осуществления изобретения, приведенных ниже и проиллюстрированных на прилагаемых чертежах.
РИС. 1 представляет собой схематический чертеж примерного экструзионного устройства, пригодного для применения на практике способов согласно изобретению;
РИС. 2 представляет собой схематический чертеж другого примерного экструзионного устройства, пригодного для применения на практике способов согласно изобретению; и
РИС. 3 представляет собой график, иллюстрирующий измерения давления, полученные с использованием множества сравнительных и показательных составов и способов.
Эти чертежи были предоставлены для облегчения понимания примерных вариантов осуществления изобретения, которые более подробно описаны ниже, и их не следует рассматривать как чрезмерно ограничивающие изобретение.В частности, количество, относительный интервал, расположение, размеры и размеры различных элементов, показанных на чертежах, показаны не в масштабе и могут быть преувеличены, уменьшены или иным образом изменены для большей ясности.
ПОДРОБНОЕ ОПИСАНИЕ ПРИМЕРНЫХ ВАРИАНТОВ ВОПЛОЩЕНИЯ Как показано на ФИГ. 1, экструзионное устройство 100 , пригодное для применения способов согласно изобретению, может включать одношнековый или двухшнековый (не показан) экструдер, включающий цилиндр 102 , окружающий шнек 104 , на котором имеется спиральный виток 106 выполнен с возможностью сжатия и, таким образом, нагревания материала, подаваемого в шнековый экструдер.Как показано на фиг. 1, базовую полимерную композицию можно подавать в шнековый экструдер в виде текучего твердого вещества, такого как шарики, гранулы или пеллеты, или в виде жидкого или полужидкого расплава из одного или нескольких (не показаны) загрузочных бункеров 108 .
По мере продвижения основной полимерной композиции через шнековый экструдер уменьшающееся расстояние между витками 106 определяет последовательно уменьшающееся пространство, через которое полимерная композиция проталкивается за счет вращения шнека.Это уменьшение объема приводит к повышению температуры полимерной композиции для получения полимерного расплава (если использовался твердый исходный материал) и/или к повышению температуры полимерного расплава.
По мере продвижения полимерной композиции через шнековый экструдер 100 в цилиндре 102 может быть предусмотрено одно или несколько отверстий с соответствующим устройством 110 , предназначенным для введения одной или нескольких полимерных технологических добавок в полимерную композицию. Аналогичным образом, в цилиндре 102 может быть предусмотрено одно или несколько отверстий с соответствующим устройством 112 для введения одного или нескольких вспенивающих агентов в полимерную композицию. После введения в полимерную композицию добавки для обработки полимера и пенообразователя (агентов) полученную смесь подвергают некоторому дополнительному смешиванию, достаточному для равномерного распределения каждой из добавок по всей полимерной композиции с получением экструзионной композиции.
Эта экструзионная композиция затем пропускается через экструзионную головку 114 и выходит из головки в область пониженного давления (которое может быть ниже атмосферного давления), тем самым позволяя вспенивающему агенту расширяться и образовывать слой полимерной пены или плиту. Полимерная пена может быть подвергнута дополнительной обработке, такой как каландрирование, погружение в воду, охлаждающее распыление или другие операции для контроля толщины и других свойств получаемого продукта из полимерной пены.
Как показано на РИС. 2, экструзионное устройство , 200, , используемое для практического применения способов согласно изобретению, может включать одношнековый или двухшнековый (не показан) экструдер, включающий цилиндр , 202, , окружающий шнек , 204, , на котором имеется спиральный виток , 206, . выполнен с возможностью сжатия и, таким образом, нагревания материала, подаваемого в шнековый экструдер. Как показано на фиг. 2, основная полимерная композиция, необязательно смешанная с одним или несколькими полимерными технологическими добавками, может подаваться в шнековый экструдер в виде текучего твердого вещества, такого как шарики, гранулы или пеллеты, или в виде жидкого или полужидкого расплава из одного или нескольких ( не показано) загрузочные бункеры 208 .
По мере продвижения основной полимерной композиции через шнековый экструдер уменьшающееся расстояние между витками 206 определяет последовательно уменьшающееся пространство, через которое полимерная композиция проталкивается за счет вращения шнека. Это уменьшение объема приводит к повышению температуры полимерной композиции для получения полимерного расплава (если использовался твердый исходный материал) и/или к повышению температуры полимерного расплава.
По мере продвижения полимерной композиции через шнековый экструдер 200 , одно или несколько отверстий могут быть обеспечены через цилиндр 202 с соответствующим устройством 212 , сконфигурированным для введения одного или нескольких вспенивающих агентов и, необязательно, одной или нескольких операций обработки полимера. вспомогательные вещества в полимерную композицию.После того, как в шнековый экструдер введены требуемые количества полимера, вспомогательного(ых) вещества(в) для обработки полимера и вспенивающего(ых) агента(ов), полученная смесь подвергается некоторому дополнительному смешиванию, достаточному для равномерного распределения каждой из добавок по всей полимерной композиции до получить экструзионную композицию.
Эта экструзионная композиция затем пропускается через экструзионную головку 214 и выходит из головки в область пониженного давления (которое может быть ниже атмосферного давления), тем самым позволяя вспенивающему агенту расширяться и образовывать слой полимерной пены или плиту.Как показано на фиг. 2, это снижение давления может быть достигнуто постепенно по мере того, как экструдированная полимерная смесь продвигается через последовательно увеличивающиеся отверстия, предусмотренные в головке, или через какое-либо подходящее устройство (не показано), расположенное после головки для экструзии, для до некоторой степени контролирующего способ, которым прикладывается давление. к полимерной смеси восстанавливается. Полимерная пена также может быть подвергнута дополнительной обработке, такой как каландрирование, погружение в воду, охлаждающее распыление или другие операции для регулирования толщины и других свойств получаемого продукта из полимерной пены.
Типичные способы согласно изобретению могут использовать один или несколько различных пенообразователей для достижения требуемых свойств полимерной пены в конечном продукте. Как правило, полимерная композиция будет включать, по крайней мере, большую часть полистирола с высокой текучестью расплава (например, полистирола, имеющего индекс текучести расплава по меньшей мере примерно 10 г/10 минут (при измерении в соответствии с ASTM D 1238, условие L) с использованием атмосферный газ, предпочтительно CO 2 , в качестве основного вспенивателя.
В дополнение к CO 2 , одна или несколько полимерных технологических добавок (PPA), выбранных из группы сложных эфиров, в частности сложных эфиров адипиновой кислоты и более конкретно сложных эфиров бис(nR)адипиновой кислоты, где R выбран из группы, состоящей из C 6 -C 16 и предпочтительно C 8 -C 13 , алифатические (линейные, циклические и разветвленные, насыщенные и ненасыщенные) и ароматические (замещенные и незамещенные) группы, особенно соединения, такие как бис(n -деканил) адипат. Технологическая добавка (добавки) улучшит стабильность профиля давления/температуры экструзии и, таким образом, улучшит однородность при производстве пенополистирольных плит различной толщины с использованием атмосферного газа, такого как воздух, N 2 или, предпочтительно, CO . 2 в качестве основного пенообразователя.
Полимерная композиция предпочтительно представляет собой стирольный полимер и/или другой полимер, имеющий достаточно высокий индекс текучести расплава (MFI или число текучести расплава), например индекс текучести расплава по меньшей мере около 10 (г/10 минут), таким образом, увеличение растворимости CO 2 по сравнению с той, которая может быть достигнута с полистиролами, имеющими MFI менее 10.Затем эту полимерную композицию можно объединить с небольшим количеством полимерной технологической добавки, обычно сложного эфира и предпочтительно сложного эфира адипиновой кислоты в соответствии с общей формулой I, представленной ниже:
, где X представляет собой азот или кислород, R 1 выбран из группа, состоящая из C 1 -C 20 алкила, арила или алкарила, и R 2 и R 3 независимо выбраны из группы, состоящей из водорода, C 1 -C 20 , предпочтительно C 6 -C 16 и более предпочтительно C 8 -C 13 , алифатические (линейные, циклические и разветвленные, насыщенные и ненасыщенные) и ароматические (замещенные и незамещенные) группы (и обычно идентичны), алкарил и алкоксилат, где R 2 и R 3 не могут оба обозначать H. Репрезентативные соединения представлены формулами II-IV, приведенными ниже: повышение растворимости СО 2 в полимерных композициях, таких как полистирол.
, где X представляет собой азот или кислород, R 5 выбирают из группы, состоящей из C 1 -C 20 алкила, арила, алкарила и алкоксилата.Подходящие соединения, соответствующие общей структуре, показанной в формуле V, для использования в данном изобретении показаны ниже как формулы VI-X:
быть полезным для увеличения растворимости CO 2 в полимерных композициях, таких как полистирол.
, где X представляет собой азот или кислород, R 4 выбирают из группы, состоящей из C 1 -C 20 алкила, арила, алкарила и алкоксилата.Подходящие соединения, соответствующие общей структуре, показанной в формуле V, для использования в данном изобретении представлены ниже как формулы XII-XVI:
Меньшая часть, обычно менее примерно 5% масс. , предпочтительно менее примерно 3% масс. или, возможно, даже менее примерно 2 мас.% PPA, такого как технологическая добавка адипатного полимера, можно использовать в сочетании с аналогичной или большей концентрацией вспенивающего агента(ов). Например, бис(н-деканил)адипат (формула III) можно вводить в полимерную систему или плавить при скоростях, равных приблизительно 0.5 мас.% и все еще демонстрируют улучшенную растворимость CO 2 , стабильность процесса экструзии, что отражается профилями температуры/давления процесса для производства плит из пеноматериала, демонстрирующих улучшенную размерную стабильность. Сложные эфиры, и особенно сложные эфиры адипиновой кислоты, имеют тенденцию превосходить более мелкие спиртовые соединения, такие как этанол, для сохранения свойств получаемых продуктов из пенопласта, особенно когда CO 2 используется в качестве единственного пенообразователя.
В тех случаях, когда PPA доступен в виде жидкости при комнатной температуре или близкой к ней, такой как бис(н-деканил)адипат, PPA можно закачивать через инжектор в промежуточную точку движения полимерной композиции через экструзионное устройство или экструдер. Соответственно, для систем или устройств, включающих в себя подходящее оборудование для работы с жидкостями, таких как узлы, которые использовались для впрыскивания одного или нескольких обычных PPA, таких как этанол, эти же узлы можно использовать для впрыскивания одного или нескольких новых PPA.
Другие добавки ПФА, такие как бис(3-этилгексил)адипат (формула II) и бис(н-тридеканил) (формула IV) и другие подобные соединения, как правило, проявляют аналогичные эффекты в отношении улучшения технологичности CO 2 в полимерный расплав.Другие полимеры и сополимеры, такие как сополимеры стирола и метилметакрилата (СММА), также могут быть использованы в качестве полимерной композиции в способах согласно настоящему изобретению и могут быть переработаны на том же аппарате, что и кристаллический полистирол общего назначения.
Что касается, в частности, сополимеров, использование бис(н-деканил)адипата в качестве ПАК в композиции сополимера СММА, имеющей молярное соотношение S:ММА около 80:20, способно поддерживать около 5 мас. % СО 2 в экструзионный состав.Эта полимерная композиция и схема добавок PPA имеют тенденцию увеличивать мощность вспенивания и снижать потребность в охлаждении, связанную с получаемыми в результате изделиями из пенополистирольных плит.
Некоторые ПАК, в том числе бис(н-деканил)адипинат, могут быть смешаны с другими полимерами и сополимерами, такими как этиленметилакрилат, и добавлены непосредственно к текучим частицам, гранулам, гранулам или другим составным формам и, как правило, проявляют аналогичные влияние на процесс пенообразования в целом и улучшение растворимости СО 2 в полимерной композиции.Соединение(я) ПАК может быть введено в расплав путем прямого впрыска в экструдер или путем предварительного компаундирования (смешивания) соединения(й) ПАК с одним или несколькими другими совместимыми полимерами или добавками для достижения аналогичных эффективных концентраций в конечной экструзии. состава и, таким образом, производят аналогичные эффекты.
Изобретатели также отметили, что присутствие бис(н-деканил)адипата (формула III), по-видимому, повышает растворимость ГФУ-134а в полимерной композиции.Соответственно, присутствие бис(н-деканил)адипата помогает поддерживать полимерные композиции с использованием комбинаций вспенивающих агентов, таких как HFC-134a/CO 2 , а также с добавлением воды в качестве совспенивающего агента для производства плит из пенополистирола с заданными характеристиками. характеристики.
Примеры Была проведена серия экспериментов для исследования относительной производительности изобретения и традиционной практики производства продуктов XPS. В каждом из испытаний использовали аморфный кристаллический полистирол общего назначения (в частности, PS NC0038 от NOVA Chemical), имеющий индекс текучести расплава 5-30 (г/10 мин) (ASTM D 1238, условие L), 0.78 мас.% бис(н-деканил)адипата, 1,0 мас.% гексабромциклодекана в качестве антипирена и 0,2 мас. % талька в качестве зародышеобразователя. Затем эту смесь подавали в двухшнековый экструдер с диаметром шнека 132 мм. Твердые вещества расплавляют, а затем смешивают с 3,7 мас.% CO 2 .
Из экструдера пластифицированную вспенивающуюся смесь охлаждали до второй температуры (обычно называемой температурой расплава экструзионной головки) и экструдировали в область пониженного давления с образованием вспененного продукта.В этом случае смесь охлаждали до температуры расплава головки 116°F (около 47°С) и затем выбрасывали через отверстие головки (27 см × 1,41 мм) в область более низкого давления. Примеры образцов согласно изобретению получали путем вспенивания смеси как при атмосферном давлении (101,3 кПа), так и при давлении ниже атмосферного, в частности, при вакууме 8, 12 или 16 дюймов ртутного столба (около 74,3, 60,8 и 47,3 кПа соответственно).
Сравнительные образцы были приготовлены с использованием ГХФУ-142b (11 мас.% в расчете на содержание полимера) в качестве пенообразователя и с использованием комбинации CO 2 (3. 7 мас.%) и этанол (1,5 мас.%) в качестве пенообразующей системы. Дополнительные образцовые образцы были изготовлены с использованием CO 2 (3,7 мас.%) и бис(н-деканил)адипата (формула III) (0,5 мас.%) в качестве системы пенообразователя. Низкий уровень бис(н-деканил)адипината улучшает характеристики поверхности пены и в то же время повышает способность к переработке расплава полимера. Колебания давления в экструдере обычно являются показателем того, как какая-либо система полимерного вспенивателя обрабатывается на контрольной линии. Как видно из фиг.1 изменения общего давления не существенны, как при сравнении вышеуказанных систем.
РИС. 3 показано сравнение между текущим HCFC-142b 11 %, CO 2 3,7 %/этанол 1,5 % и CO 2 3,7 %/бис(н-деканил)адипинат при уровнях 0,5 %, 1,0 % и 1,5 % с соответствующими давление на выходе экструзии, статическое давление в охладителе и давление в головке, отслеживаемые на экспериментальных линиях с этими композициями. Для системы 142b (контрольная) общего назначения PS(NOVA 1220) с индексом текучести расплава 1.6 (г/10,0 минут). Для CO 2 /этанол и всех других опытов использовали PS с высоким индексом текучести расплава 10,0 (г/10 минут) (NOVA NN0038). Были предприняты попытки изготовить пенокартон толщиной около 1 дюйма (около 25,4 мм), сохраняя при этом все остальные параметры процесса относительно постоянными.
Хотя на фиг. 3 показано давление экструзии при атмосферных условиях, это соотношение, по-видимому, справедливо и для 10 дюймов ртутного столба (около 67,5 кПа) (или любых других уровней вакуума).Эти результаты были достигнуты на экспериментальной установке Owens Corning в Талмэдже, штат Огайо. Профиль давления экструзии является показателем простоты обработки и растворимости вспенивающего агента в расплаве. Несмотря на то что. давление экструзии, охладителя и матрицы для системы CO 2 /бис(н-деканил)адипата было выше по сравнению с обычной системой 142 b , они были очень сопоставимы с системой CO 2 /этанол. На самом деле CO 2 / бис (н-деканил) адипат при 1.Уровень 5% превосходит систему CO 2 /этанол с точки зрения простоты обработки.
Позже в ходе испытаний полимер был заменен на сополимер S:MMA 80:20 (NOVA NC0044). Поскольку процесс оказался относительно стабильным, мы увеличили CO 2 постепенно до 4,3%, чтобы увеличить как потенциал продувки, так и возможности охлаждения. Этот более высокий уровень CO 2 обеспечивал приемлемые продукты с хорошей поверхностью в атмосферных условиях. По-видимому, присутствие бис(н-деканил)адипата ПФК в сочетании с более полярным сополимером S:ММА с высоким индексом плавления способствует увеличению растворимости СО 2 в полимерной системе.Способность растворять больше CO 2 оказывает огромное влияние на охлаждающую способность системы BA и простоту технологического процесса. Результаты испытаний представлены ниже в ТАБЛИЦЕ 1. Были измерены средний размер ячеек, модуль сжатия, процент открытых ячеек и значение R.
Значение R, или общее тепловое сопротивление, является мерой сопротивления теплопередаче. Способ определения R-величины описан следующим образом. Теплопроводность k определяется как отношение теплового потока на единицу поперечного сечения к перепаду температуры на единицу толщины в единицах США:
Btu·inHr·Ft2· ∘F.
И метрическая единица:
Wm·k
Теплопередача через изоляционный материал может происходить за счет проводимости твердого тела, проводимости газа, излучения и конвекции. Общее тепловое сопротивление (значение R), R является мерой сопротивления теплопередаче и определяется как:
R=t/k
Где t=толщина.
Между плитами, изготовленными с использованием ГХФУ-142b, CO 2 /этанол и CO 2 /бис(н-деканил)адипат, наблюдались некоторые заметные различия в физических свойствах, таблица 1.Плита становится слабее по мере увеличения уровня бис(н-деканил)адипината с 0,5 до 1,5%, что свидетельствует о более высокой степени пластификации. Кроме того, по-видимому, в результате повышения концентрации бис(н-деканил)адипата содержание открытых клеток имело тенденцию к соответствующему увеличению.
Дополнительные испытания проводились с использованием PS NC0038 (NOVA Chemicals) как с HFC-134a 7%/CO 2 0,5%/бис(н-деканил)адипат 1,5%, так и с HFC-134a/бис(н-деканил)адипат 1,5 % в качестве вспенивающих составов на той же пилотной линии, которая использовалась для получения ГФУ-142b, описанного выше.В ходе этих испытаний были получены полистирольные пенопласты с плотностью 2,25 фунта на фут с содержанием открытых ячеек всего около 2,29%, что находится в пределах приемлемого диапазона. В обоих этих экспериментах для улучшения качества поверхности плит из пенопласта использовали дополнительно 0,2% этилметилакрилатного полимера.