Холодная ковка, станки и чертежи своими руками — Дизайн на металле
Станки для ковки являются хорошим инструментом для художественных и творческих людей, у которых есть желание создать что-то красивое и индивидуальное в своем доме, чтобы подчеркнуть интерьер, а может сделать хороший подарок своими руками для важных людей. Существует два способа ковки металла. Чтобы сковать что-то способом горячей ковки необходимо произвести множество приготовлений и действий, поэтому дома проще всего ручная ковка дается, пользуясь способом холодной ковки. Период обучения такому процессу не занимает много времени, к тому же есть реальная возможность сконструировать станок своими руками.
Начало холодной ковки самодельными станками.
Холодная ковка своими руками требует два обязательных действия – пресс и гнутье. Для совершения всех этих действий придавать определенную температуру для металла нет необходимости, но все равно необходимо провести термообработку.
Чтобы сконструировать что-то своими руками, уже не обязательно иметь специальные станки для художественной ковки, теперь можно создать станки для ковки металла в домашних условиях.
Самодельный станок для холодной ковки запросто можно использовать для создания конструкций, которые будут значительно прочнее, нежели те, которые были изготовлены штамповкой. Кованые изделия своими руками получаться высококачественными, когда будет все сделано верно и без ошибок, ведь исправить их очень сложно. После нескольких работ, благодаря полученному опыту, можно начать делать превосходные конструкции, используя самодельные станки и приспособления для холодной ковки.
При изготовлении большого количества одинаковых металлических конструкций лучшего всего воспользоваться чертежами, приготовленными заранее. Чертежи на станки для холодной ковки своими руками заготавливаются заблаговременно. В некоторых случаях деталь лучше будет прогревать, чтобы избавиться от дефектов в последующем. Тем, кто не так давно начал использовать самодельные станки для холодной ковки для начала стоило бы продумать план работ, а так же приобрести необходимые навыки.
Самодельный станок для холодной ковки.
Компоненты станка и необходимые инструменты.
Станок для ковки своими руками состоит из определенных устройств. Среди которых обязательно должны быть:
Этими приспособлениями пользоваться лучше всего. Улитка для холодной ковки своими руками понадобиться для сплетения стальных прутьев. Можно ознакомиться с фото, чтобы лучше разглядеть конструкцию и пример деталей. Кузнечное оборудование для холодной ковки металла отыгрывает важную роль в работе. Основным инструментом во время работу будет гнутик. Это весьма простой элемент.
Изготавливаем станок.
Чтобы обработать трубы с шестигранным и круглым сечением используют «волну». «Фонариком» сгибают металлические прутья, а твистер чем-то на него похож, весьма удобное преспособление. Глобусом делается большая дуга из профильных прутьев.
Станки холодной ковки в большей мере выгоднее всего сделать самому, ведь далеко не все можно обработать ручными инструментами, а цена за станок для художественной ковки очень высока. Когда мастер за счет своих навыков с помощью своего оборудование создаст конструкцию, она будет неповторимой и особенной, пускай в чем-то и будет не такой качественной, как заводская. При изготовлении большого количества деталей, правильно будет создать кодуктор на электромоторе. Это облегчает процесс работы.
Станок холодной ковки своими руками должен быть приспособлен для таких видов работ, как гибка, закручивание и вытяжка.
В процессе вытяжки конструкция приобретает определённую форму. Поэтому она должна пройти через пресс, после чего сечения первостепенного материала станет меньше. Под гибкой подразумевается создание гнута в нужном угле. Для этого понадобятся шаблоны. Фото чертежей кованных изделий своими руками приготавливается заранее из которого и будет сделан шаблон. К стальной пластине прикрепляется завитушка, а сам лист закрепляется в держателе станка. В конце заготовке размещается прорезь, другой же конец закрепляется на месте. Используя рычаг, происходит влияние на окончание конструкции, которое необходимо провести по каждому изгибу пластины, которая используется как шаблон.
Видео самодельного станка по загибанию балясин.
Станки для холодной ковки своими руками.
Многие опытные изготовители собственноручно собирают несложные механизмы, которые позволяют создавать уникальные конструкции. На это влияет стаж работы. Чертежи на станки для холодной ковки своими руками можно в достаточном количестве найти в интернете, как и фото изделий холодной ковки, которые можно получить в итоге. Фотография такого оборудования позволяет выполнить мастеру чертеж с нуля, если у него есть опыт.
Можно рассмотреть станок «Улитка». Используя его можно создавать различные спирали или волны. Для создания такого станка нужно иметь чертежи на станок для холодной ковки своими руками такого типа, а так же делать все в соответствии с технологией. Рабочая поверхность должна состоять из листового металла. 4 мм толщины будет достаточно. Размеры устанавливаются исходя из габарита детали. Для придания форму необходим листовой металл в толщину 3 мм и в виде полос.
Для создания нормального процесса работы нужно хорошо зафиксировать один из концов детали. В этом поможет прут, равный ширине полос. Чтобы зафиксировать рабочую площадку нужно будет использовать верстак. Основная цель всего – придать максимальной неподвижности детали, потому что во время холодной ковки нужно приложить большие усилия.
Перед началом изготовления любого станка для холодной ковки, инструментами для ручной работы нужны шаблоны, эскизы и различные чертежи, в том числе и чертеж на оборудование для холодной ковки своими руками.
Придать более хорошую точность разметке можно за счет миллиметровой бумаги. Нужно нарисовать на ней спираль, где будут увеличиваться витки в радиусе. Между ними нужно должным образом соблюдать равную дистанцию. Такое условие будет обязательным только для создания симметричных узоров.
Станок для холодной ковки.
Для создания любого станка можно использовать несколько вариантов на выбор – разборный, монолитный или сплошной. По все длине бедующего станка рекомендуется приварить маленькие прутки. На рабочей площадке для этого стоит просверлить специальные дырки. Требуется хорошо закрепить концы деталей, которые будут выгибаться.
Чертежи станков для холодной ковки. Холодная ковка своими руками станки чертежи
Cтанки для холодной ковки пригодятся тем, кто любит мастерить и разбирается в таком оборудовании. Многие используют станки при создании усадеб, интерьера и подарков. Изделия, сделанные с помощью холодной ковки, используют как украшения вместе с другими элементами декора. Чтобы заниматься холодной ковкой, нужно прилагать много усилий. Этим трудно заниматься дома. Самым легким способом считается художественная холодная ковка.
Чтобы сделать нормальное изделие своими руками , нужны будут инструменты и чертежи. Эти вещи уменьшают затраты и сокращают время изготовления. В некоторых случаях детали нагревают, чтобы на стыках не было кривизны. Перед созданием самодельного станка холодной ковки нужно заняться проектированием.
Вначале нужно нарисовать спираль, которая будет постепенно увеличиваться, соблюдая при этом симметричность узоров. Дистанцию витков нужно размещать так, чтобы она была больше диаметра прутьев и можно было взять из станка сделанное изделие. При создании рабочей поверхности нужно использовать листовое железо. Размеры определяют с помощью основания габаритов и использованных деталей. Чтобы создать форму, нужен листовой металл в виде полос.
Перед началом работы всем начинающим нужно ознакомиться с видеоматериалами о холодной ковке оборудования своими руками.
Инструменты и материалы для холодной ковки :
Самым важным приспособлением для работы всегда был гнутик. Он используется при изменении формы металла. Главная функция гнутика — изгиб детали под разными углами.
Улитка применяется для манипуляций в спирали. Она является оснасткой для сгибания различных изделий, профилей и т. д. При работе с этим инструментом можно не ограничивать спираль в радиусе и сделать нужную величину.
Фонарик необходим для сгибания материала из металла. С помощью фонарика обрабатывают прутки из металла. Благодаря приспособлению волна можно создавать волны и выгнутые куски. Применяют волну при обработке труб с круглым сечением.
Твистер имеет схожесть фонариком. При его помощи можно выкручивать прутья.
Глобус помогает создать большую дугу из профиля с толщиной до 12 мм. В конце заготовки тоже сгибаются. Это самый легкий инструмент и его довольно часто делают своими руками.
Станок для холодной ковки своими руками, чертежи
По размеру конструкции можно приварить маленькие кусочки прутков с расстоянием 5-6 см. В конструкции нужно сделать отдельные отверстия. Если лень разбираться, как правильно собрать станок для холодной ковки, всегда можно посмотреть обучающее видео. При возведении кондуктора своими руками нужно обратить внимание на виды основных работ: вытяжки, гибки и закручивания. Все эти механизмы можно объединить в одно. Во время вытяжки для изделия создается нужная форма. Лучше всего изделие пропустить через валики или пресс, из-за этого сечение исходного сырья может уменьшиться. Основной процесс гибки состоит из того, чтобы деталь гнули под определенным углом. Выполнить эту операцию можно с использованием шаблона.
Это делается следующим образом:
- подготовка чертежа;
- создание шаблона по чертежу;
- приваривание завитушки на стальную пластину;
- лист нужно крепить на станке в держателе;
- установление прорези и окончательная фиксация.
При создании шаблона специальный шов нужно проводить с внешней стороны, чтобы он в последующем не мешал при эксплуатации материала.
Виды станков для холодной ковки
Существует несколько видов станков для холодной ковки:
Как сделать станок для ковки своими руками?
Из-за того, что станки для холодной ковки имеют высокую стоимость, а цены зависят от производителей, многие люди прибегают к созданию таких станков своими руками.
При создании самодельного станка « Улитка » понадобится следующее:
- прутья из металла;
- стальные листы в виде полосок;
- специальная труба;
- сварка, плоскогубцы , болгарка.
Основная схема для создания станка:
- возьмите обычный листок, нанесите на него рисунок спирали, проверьте размеры для резьбы;
- при помощи болгарки, нужно сделать два отдельных листа из пластины;
Первая с параметрами 100х100 мм и вторая 130х130 мм.
- возьмите прут и полосы из стали, почистите края срезов от заусениц;
- плоскогубцами создайте изгиб стальных полос по схеме;
- приварить элементы;
- приварите стальную трубу снизу.
Вот весь несложный процесс по созданию станка для ковки из разных материалов.
Чертежи для создания станка можно использовать совершенно разные, все зависит от материалов, использованных в работе.
Как создать свой ковкий станок торсион ? Этот станок используют при закручивании спиралей в виде змейки, созданных из металла.
Инструменты для создания:
- стальной лист;
- балка;
- тиски и элементы для крепежа;
- редуктор, цепь или электромотор;
- болгарка;
- сварка.
Схема действий при создании станка для холодной ковки:
Вот основные способы создания самодельных станков своими руками. Главное — это желание и усиленная работа, тогда все получится. Оборудование и приспособления для работ по холодной ковке можно купить в любом специализированном магазине.
Какие технологии и приемы используются в холодной ковке, что нужно знать о производственных операциях? Об этом — далее в нашем материале.
Сегодня большое распространение получили небольшие домашние мастерские по обработке металла. Это и хобби, и дополнительный доход в семейный бюджет. Более распространена холодная ковка своими рукам. Такая технология не требует больших затрат на начальном этапе, а изделия ручной работы ценятся довольно высоко.
Какие технологии и приемы используются таким способом металлообработки, что нужно знать о производственных операциях? Об этом — далее в нашем материале.
Холодным способом обрабатывается, в основном, металлопрокат в виде прутков, квадратов, круга, полосы или листа.
Для производства применяются особые приспособления и инструменты, причем часто они узкоспециализированные и не пригодны для работы в других направлениях.
Разогрев заготовок до ковочной температуры не предусмотрен технологией, которая использует одно из главных свойств металла — пластичность. Нагрев возможен лишь частичный в местах изгиба некоторых изделий (например, при слишком толстом металле исходного материала).
Холодная ковка металла используется для изготовления решеток, заборов, ворот, калиток (и отдельных элементов их украшений), каркасы мебели и различные детали декора.
При этом в процессе производства этой продукции металл поддается прессованию и изгибанию, что делает изделие даже прочнее, чем при горячей ковке, так как не изменяются свойства металла, а кристаллическая решетка, наоборот, упрочняется за счет сжатия.
Холодная ковка в домашних условиях довольно простой, но, в то же время, и сложный технологический процесс, который требует опыта. Что нужно знать о такой металлообработке, а также что потребуется для изготовления изделий без разогревания материалов?
Холодная ковка своими руками
Весь рабочий процесс по созданию изделий с помощью холодной ковки можно разделить на несколько этапов.
- Чертеж или схема готового изделия.
- Подбор материалов.
- Обработка металла и изготовление деталей.
- Сборка и отделка.
Чертеж
Гибка — практически основной процесс, на котором построена холодная ковка. Перечисленные выше станки (кроме твистера и фонарика) работают по этому же технологическому принципу. Чаще всего используется улитка, которая формирует большой список разного рода завитков (вензелей, волот, спиралей и прочих).
Кручение построено на свойстве металла — пластичности и способности сохранять заданную форму. Во время такой обработки, заготовка закручивается под усилием вокруг своей оси. Обычно процедуру делают на твистере. Однако, такие элементы, как корзинки, производят с помощью фонарика. Он способен закрутить несколько заготовок, сформировав при этом объемный элемент.
Обычно вся обработка проводиться холодным способом, однако, иногда требуется нагрев определенных точек на заготовке. Это делают при гибке или кручении толстых деталей или же когда нужно исправить бракованные элементы. Нагревание может осуществляться в кузнечных горнах или газовым резаком до температуры 200-300 градусов, что значительно ниже ковочной температуры.
Также в холодной обработке металла используются стандартные способы: резка, рубка, шлифовка и прочие. Для этого применяют болгарки, отрезные круги, шлифовальные машины, гильотины, зубила и прочие.
Сборка и отделка
Эти два этапа завершают процесс изготовления изделий способом холодной ковки.
Сборка деталей в единую комбинацию проводится несколькими способами:
- На заклепках.
- На хомутах.
- Сварка.
Самый простой и быстрый метод собрать изделие — это электро- или газосварка (последняя используется реже).
Однако, некоторые детали крепят на хомуты и заклепки, если это предусмотрено стилевым оформлением.
Ранее использовалась кузнечная сварка, которая сегодня потеряла свою актуальность из-за трудоемкости процесса.
К окончательной отделке относят шлифовку, зачистку поверхностей металла, а также нанесение декоративного покрытия (лакокрасочного или любого другого). После чего работа считается завершенной и проводиться монтаж готового изделия по надобности.
А что Вы можете добавить к материалу этой статьи из личного опыта? Поделитесь им в обсуждениях и оставьте свои комментарии.
Металлические завитки, изготовленные методом холодной ковки, применяются для украшения элементов экстерьера.
Изделия пользуются популярностью у владельцев загородных коттеджей и коммунальных служб, занимающихся архитектурным обустройством мест общего пользования.
Также можно применять эти элементы при изготовлении отдельных приспособлений – , уличной мебели, и даже посуды.
Такой декор, а особенно готовые изделия, очень дорого стоит. Даже стандартные комплекты, поставленные на поток и продающиеся в магазинах – имеют неподъемную цену. Что уже говорить об изделиях, изготовленных по индивидуальному заказу.
Поэтому, многие домашние мастера стараются создать подобные творения самостоятельно. Тем более что «холодная ковка своими руками» не предполагает классической кузнечной технологии. Обработка материала заготовки производится без использования нагрева и работы кузнечным молотом. А значит, ее можно выполнить в домашних условиях.
Однако для подобной работы требуется специальный инструмент – гнутик для холодной ковки. Оборудование предлагается в магазинах, или изготавливается в мастерских по индивидуальному заказу. Набор для универсальной обработки металла представляет собой целый комплекс различных приспособлений.
Во-первых, это действительно уникальный инструмент, позволяющий создавать высокохудожественные изделия, без молота, кузнечного горна и наковальни.
Во-вторых, из простого металла такие приспособления не делают, иначе станок выйдет из строя при первой же нагрузке. Стало быть, качественная и прочная сталь увеличивает цену.
Рассмотрим различные самодельные приспособления для холодной ковки
Начнем с принципа работы инструмента:
Заготовка (металлический круг, квадрат или полоса) устанавливается в станок между направляющими. При помощи рычажного ручного, или редукторного электрического привода, происходит изменение геометрической формы.
Существует несколько стандартных приспособлений, представляющих собой шаблоны для холодной ковки.
Приспособление «гнутик».
Это усовершенствованный аналог . С его помощью заготовка изгибается под запрограммированным углом. Он может быть как одиночным, так и формировать геометрические фигуры. Декоративный элемент бывает плоским или объемным, и все это делает один инструмент. С помощью гнутика можно выполнять дугу из прямой заготовки.
Приспособление твистер.
С его помощью заготовка закручивается винтом. Работает по принципу шпинделя токарного станка или патрона для дрели. Часть заготовки прочно зажимается в неподвижных тисках, а другая закручивается при помощи воротка или электропривода.
Особенность конструкции – неподвижные тиски должны иметь возможность продольного перемещения.
Деталь при скручивании уменьшается по длине, и может выскочить из крепления.
Если вместо одного прута вставить в станок пучок проволоки – можно получить объемную стальную фигуру, так называемую корзинку. Ее изготовление требует особой сноровки.
Самое популярное приспособление — улитка.
Самый распространенный шаблон для холодной обработки металла. С его помощью создаются завитки любой формы и с разным количеством оборотов. Его конструкция простая и сложная одновременно. Недостаточно просто создать шаблон нужной формы.
Давайте рассмотрим виды приспособлений и фигуры, которые можно получить с их помощью.
Если вы только собираетесь организовать мастерскую холодной ковки и хотите избежать больших расходов, то самостоятельное изготовление станков и приспособлений поможет создать свой маленький бизнес без чрезмерных затрат.
Основные приспособления и станки
Станки для холодной ковки предназначены в основном для гибки по дуге или углом, а также для скручивания. Они могут быть ручные или с электрическим приводом.
Основные виды станков и приспособлений для холодной ковки:
- «Гнутик»
- «Твистер»
- «Улитка»
- «Глобус»
- «Волна»
- «Фонарик»
Приспособление «Гнутик»
Покупной или сделанный самостоятельно «Гнутик» — универсальное приспособление, позволяющее получить дугу или угол из прута. Он представляет собой основание с ползуном, на котором закреплен упор с углом (90° или другим по необходимости) и двумя цилиндрическими неподвижными упорами. Перемещая ползун и угловой упор, прут сгибается под углом. Для получения дуги предусмотрен третий цилиндр, вращающийся на противоположной от углового упора стороне.
Приспособление может быть выполнено на горизонтальной или вертикальной платформе.
Аксонометрия приспособления «Гнутик» — вертикальное расположение
Чтобы смасштабировать размеры, приводим чертёж нижней планки этого «Гнутика».
Планка нижняя
Это приспособление — универсальное. С помощью насадок на нем можно не только гнуть, но и резать, и пробивать отверстия. Но это уже будет следующим шагом.
Получение дуги на «Гнутике»
Получение угла на «Гнутике»
Так выглядит самодельный «Гнутик»:
Приспособление «Твистер»
«Твистер» — инструмент для скручивания прутков, в основном квадратного сечения, вдоль продольной оси. Это несложное приспособление может быть ручным и с электроприводом. Принцип действия: закрепляются оба конца прута, потом одно крепление начинает проворачиваться, скручивая металл до необходимой формы.
Внешний вид покупного ручного «Твистера»
Посмотрите фото самодельного «Твистера» с электроприводом, собранного с использованием электрооборудования бывшего в употреблении:
Для изготовления «Фонариков» и «Шишек» существует специальный станок, но для начала можно использовать и «Твистер», как это показано на видео (англоязычное, но всё предельно понятно).
Видео 1. Как сделать заготовку под «Фонарик» на «Твистере»
Приспособление «Улитка»
Инструмент «Улитка» предназначен для получения завитков (или спиралей) и «валют» (S-образных деталей). Встречаются различные конструкции.
Один из вариантов конструкции: 1 — лемех улитки; 2 — основа станка; 3 — прижимной валик; 4 — рычаг для управления прижимным валиком; 5 — крепление основы; 6 — палец для фиксации лемехов; 7 — паз для прижиного валика; 8 — ось рычага управления; 9 — пружина для прижатия валика; 10 — фиксатор для заготовки; 11 — ведущий лемех улитки; 12 — основная ось; 13 — рычаги
В результате должно получиться такое приспособление:
Ещё одна лёгкая конструкция, чтобы гнуть прокат сечением до 12 мм:
1 — сегмент улитки; 2 — эксцентрик; 3 — ручка; 4 — основание; 5 — направляющие полозья; 6 — ось; 7 — ползун; 8 — гайка оси; 9 — ось крепления ролика; 10 — ролик; 11 — приводная ось; 12 — направляющая эксцентрика; 13 — центральный сегмент улитки; 14 — барашек эксцентрика; 15 — основная ножка; 16 — соединительный штифт сегментов улитки; 17 — корректирующий винт; 18 — соединительное ухо сегментов улитки
Часто приспособление «Улитка» делают на опоре, особенно если гнуть нужно толстый прокат.
Несколько полезных видеоматериалов по самодельных станкам «Улиткам».
Вариант с массивным основанием на опоре:
Видео 2. Изготовление основания
Видео 3. Изготовление улитки
Видео 4. Работа станка
Вариант настольного приспособления:
Видео 5. Часть 1
Видео 5. Часть 2
Подробнее о таких конструкциях мы поговорим ниже.
Приспособление «Глобус»
Такое устройство внешне похоже на школьный транспортир и предназначено для изготовления дуг с большим радиусом изгиба из полосы, квадрата, круга или шестигранника. Сначала загибом фиксируется один конец заготовки, потом она изгибается по всей длине по шаблону. Принцип действия чем-то похож на работу закаточной машинки для консервации.
Внешний вид приспособления
Видео 6. Работа на «Глобусе»
Пользуясь исключительно мускульной силой, дугу большого диаметра можно изготовить на шаблоне, прикрученном или приваренном к верстаку. На нём хорошо гнуть полосу, трубу тонкостенную и т. д.
Шаблон
Приспособление «Волна»
Получить волнообразные изделия из заготовки круглого, квадратного, шестигранного сечения или трубки можно на приспособлении «Волна». Деформация заготовки происходит между вертикальными валками прокручиванием.
Приспособление волна и полученные изделия
Видео 7. Приспособление в действии
Приспособление «Фонарик»
На этом станке изготавливают заготовки элементов «Фонарики» или «Шишки», которые могут состоять из 4-х, 6-ти, 8-ми и более прутков. По принципу действия станок похож на «Твистер», но тут заготовки изгибаются вокруг направляющего вала, что формирует более правильную и точную конфигурацию изделия.
Приспособление «Фонарик»
Видео 8. Работа приспособления для изготовления «Фонарик»
Приспособление для холодной ковки элемента «Хомут»
Элемент холодной ковки «Хомут» предназначен для фиксирования между собой других элементов конструкции.
Приспособление для гибки «Хомута» можно выполнить по прилагаемым чертежам.
Приспособления для выполнения «гусиной лапки»
«Гусиная лапка» — расплющивание с нанесением красивых насечек концов заготовок для придания большей изящности конструкции или с целью уменьшения толщины для различных соединений.
Концы элементов оформлены «гусиной лапкой»
Эту операцию можно выполнить при помощи станка с матрицей или приспособлением и тяжелым кузнечным молотом на наковальне. Оба варианта мы даем в виде видеоматериалов.
Видео 9. Станок для изготовления «гусиной лапки»
Видео 10. Приспособления для ковки «гусиных лапок»
Видео 11. Подробный процесс изготовления штампа
Ниже прокатный станок для выполнения той же операции.
Станок для прокатки «гусиной лапки» (расстояние между вальцами регулируется). Материалы для прокатного станка: шестерни и валы — запчасти от комбайна б/у
Принцип действия
Изготовление «Улитки» с приводом
«Улитка» с электроприводом облегчает изготовление завитков и «валют». Особенно это ценно, когда работа не «для души», а для изготовления большого количества однотипных изделий на потоке при работе на заказ.
Ниже приведены этапы сборки станка для гиба прута максимальным сечением 10х10 мм. Двигатель мощностью 0,5 КВт/1000 об/мин работает при этом на пределе своих возможностей. Выполняет 6 оборотов вала в минуту. Сегменты улитки выточены из круглой болванки Ст.45 без термообработки высотой 25 мм и толщиной 20 мм. Улитка насажена на вал на подшипниках от заднего колеса мотоцикла — 7204. Поддерживающий ролик закреплён жёстко в пазу. Между двигателем и редуктором установлены шкивы.
Ниже приведены чертежи сегментов улитки.
Элемент улитки 1
Элемент улитки 2
Элемент улитки 3
Центральный элемент улитки
Для более массивного прута (от 12 мм) мощность двигателя должна составлять более киловатта. На фотографиях ниже представлен станок с двигателем мощностью 2,2 кВт, 1000 об/мин, дающий выход на валу около 10 об/мин. Это уже станок для профессионального использования. Применён бывший в употреблении редуктор, матрица вырезана из заготовки толщиной 30 мм — самый трудоёмкий процесс.
Для холодной ковки ещё понадобятся наковальня и молот. Горн не нужен, он требуется только для горячей ковки.
Совет! Перед началом работ начертите эскиз будущей конструкции в натуральную величину. Это поможет корректировать элементы и не запутаться при сборке.
Для изготовления кованых изделий применяют два метода — холодная и горячая обработка. Первый способ отличается низкой трудоемкостью, но предусматривает наличие специального инструмента. В большинстве случаев можно изготовить станок для холодной ковки своими руками, руководствуясь стандартными чертежами.
Принципы холодной ковки металлов
Для производства металлических кованых изделий необходимо обеспечить процесс их контролируемой деформации. При этом следует учитывать структуру материала, его технические и эксплуатационные свойства.
Принцип холодной ковки основан на воздействии внешних факторов на кристаллическую решетку материала. Она состоит из зерен неправильной формы. В результате искажения структуры, которое выполняет станок для холодной ковки, происходит уплотнение и изменение конфигурации заготовки. Так как одним из условий является сохранение свойств детали — необходимо подобрать чертежи для производства станков.
Особенности холодной ковки металла, требования к приспособлениям для этого:
- возможна обработка только низкоуглеродистых сталей, которые обладают высокой степенью пластичности;
- в качестве заготовок используются прутки различных сечений;
- предварительный расчет размеров конечных изделий. В процессе их производства необходим постоянный контроль за геометрическими параметрами;
- использование различных станков для формирования нужной конфигурации.
В настоящее время для художественной обработки металлов методом холодной ковки используется ряд специальных инструментов. Часть из них можно сделать самостоятельно. Но для этого необходимо предварительно изучить чертежи и специфику производства.
Кованые изделия могут выполнять несколько функций одновременно — эстетическую и эксплуатационную. Это относится к заградительным конструкциям различной конфигурации, например, волна.
Улитка для холодной ковки
Самыми распространенными и востребованными являются самодельные станки для холодной ковки типа улитка. С их помощью происходит формирование спиралевидных заготовок. Конструкция оборудования позволяет изготовить его своими руками.
Чертеж станка «улитки» можно адаптировать для производства конкретного типа изделия художественной ковки. Для этого необходимо знать следующие параметры:
- минимальный и максимальный радиус кривизны заготовки;
- геометрические параметры и форма исходного материала;
- планируемая производительность.
Для массового производства необходимо сделать станок для ковки с электроприводом. Если же планируется работа в домашних условиях — подойдут ручные модели.
В качестве основы для проектирования улитки необходимо использовать стальной лист толщиной не менее 3 мм. Это позволит гнуть прутки большого сечения.
Для формирования различных углов необходим ручной гнутик – одно из самых требуемых приспособлений для холодной ковки металла. Он состоит из стальной пластины, на которой находятся два опорных вала и движущийся упор.
Заготовка помещается между опорными валами и клином. Последний имеет механизм смещения по направлению к упорам. В результате этого действия происходит худ. обработка стального прута. Таким способом можно изготовить кованые изделия различной формы.
Особенности применения гнутика, необходимые для корректного составления его чертежа:
- предварительный расчет угла деформации;
- в конструкции можно предусмотреть дополнительную гибочную часть. Для этого следует установить еще один вращающий вал;
- монтажный узел для крепления к столу.
Для производства гнутика необходимо применять инструментальную сталь. Это объясняется большими нагрузками во время эксплуатации. Дополнительно на нем можно собирать элементы типа «волна», но для этого следует модернизировать исходный чертеж.
Минимальный и максимальный радиус изгиба для худ. ковки необходимо рассчитать исходя из геометрических параметров заготовки.
Твистер для холодной ковки
Современную художественную ковку сложно представить без элементов, имеющих форму шнека. Для производства подобных худ. деталей предназначен твистер — самодельный станок для холодной ковки.
Особенностью этого инструмента является раскручивание прутика вдоль оси. Конструктивно чертеж станка состоит из двух частей — фиксирующей и подвижной. Деталь крепится между ними и с помощью поворотной ручки выполняется ее информация.
Эксплуатационные качества приспособления:
- расчет рычага давления для минимизации усилий по производству заготовок;
- возможность изменения расстояния между фиксирующими элементами инструмента.
Это позволит изготовить детали различной длины;
- следует учитывать, что формирование спирали происходит со стороны фиксации.
Благодаря твистеру можно сделать кованые элементы для оконных решеток, стальных заграждений и т.д.
Это основной перечень станков для холодной ковки. Но кроме них применяется различное оборудование, предназначенное для создания по-настоящему худ. изделий.
В видеоматериале показаны примеры станков для холодной ковки металлов в домашних условиях:
Чертеж станка для холодной ковки
Чертежи станков для изготовления элементов холодной ковкиСтанки для ковки являются хорошим инструментом для художественных и творческих людей, у которых есть желание создать что-то красивое и индивидуальное в своем доме, чтобы подчеркнуть интерьер, а может сделать хороший подарок своими руками для важных людей. Существует два способа ковки металла. Чтобы сковать что-то способом горячей ковки необходимо произвести множество приготовлений и действий, поэтому дома проще всего ручная ковка дается, пользуясь способом холодной ковки. Период обучения такому процессу не занимает много времени, к тому же есть реальная возможность сконструировать станок своими руками
Начало холодной ковки самодельными станками.
Холодная ковка своими руками требует два обязательных действия – пресс и гнутье. Для совершения всех этих действий придавать определенную температуру для металла нет необходимости, но все равно необходимо провести термообработку.
Чтобы сконструировать что-то своими руками, уже не обязательно иметь специальные станки для художественной ковки, теперь можно создать станки для ковки металла в домашних условиях. Но без опыта работы с такими инструментами все равно не справиться. Чтобы вся работа была успешной, нужно пользоваться металлами определенной толщины.
Самодельный станок для холодной ковки запросто можно использовать для создания конструкций, которые будут значительно прочнее, нежели те, которые были изготовлены штамповкой. Кованые изделия своими руками получаться высококачественными, когда будет все сделано верно и без ошибок, ведь исправить их очень сложно. После нескольких работ, благодаря полученному опыту, можно начать делать превосходные конструкции, используя самодельные станки и приспособления для холодной ковки.
При изготовлении большого количества одинаковых металлических конструкций лучшего всего воспользоваться чертежами, приготовленными заранее. Чертежи на станки для холодной ковки своими руками заготавливаются заблаговременно. В некоторых случаях деталь лучше будет прогревать, чтобы избавиться от дефектов в последующем. Тем, кто не так давно начал использовать самодельные станки для холодной ковки для начала стоило бы продумать план работ, а так же приобрести необходимые навыки. Не лишней тут будет помощь различных видео уроков в сети интернет, а так же специальных курсов.
Компоненты станка и необходимые инструменты. Станок для ковки своими руками состоит из определенных устройств. Среди которых обязательно должны быть:
1. гнутик;
2. улитка;
3. волна;
4. глобус;
5. твистер;
6. фонарик;
Этими приспособлениями пользоваться лучше всего. Улитка для холодной ковки своими руками понадобиться для сплетения стальных прутьев. Можно ознакомиться с фото, чтобы лучше разглядеть конструкцию и пример деталей. Кузнечное оборудование для холодной ковки металла отыгрывает важную роль в работе. Основным инструментом во время работу будет гнутик. Это весьма простой элемент.
Чтобы обработать трубы с шестигранным и круглым сечением используют «волну». «Фонариком» сгибают металлические прутья, а твистер чем-то на него похож, весьма удобное преспособление. Глобусом делается большая дуга из профильных прутьев.
Станки холодной ковки в большей мере выгоднее всего сделать самому, ведь далеко не все можно обработать ручными инструментами, а цена за станок для художественной ковки очень высока. Когда мастер за счет своих навыков с помощью своего оборудование создаст конструкцию, она будет неповторимой и особенной, пускай в чем-то и будет не такой качественной, как заводская. При изготовлении большого количества деталей, правильно будет создать кодуктор на электромоторе. Это облегчает процесс работы.
Станок холодной ковки своими руками должен быть приспособлен для таких видов работ, как гибка, закручивание и вытяжка.
В процессе вытяжки конструкция приобретает определённую форму. Поэтому она должна пройти через пресс, после чего сечения первостепенного материала станет меньше. Под гибкой подразумевается создание гнута в нужном угле. Для этого понадобятся шаблоны. Фото чертежей кованных изделий своими руками приготавливается заранее из которого и будет сделан шаблон. К стальной пластине прикрепляется завитушка, а сам лист закрепляется в держателе станка. В конце заготовке размещается прорезь, другой же конец закрепляется на месте. Используя рычаг, происходит влияние на окончание конструкции, которое необходимо провести по каждому изгибу пластины, которая используется как шаблон.
Видео самодельного станка по загибанию балясин.
Многие опытные изготовители собственноручно собирают несложные механизмы, которые позволяют создавать уникальные конструкции. На это влияет стаж работы. Чертежи на станки для холодной ковки своими руками можно в достаточном количестве найти в интернете, как и фото изделий холодной ковки, которые можно получить в итоге. Фотография такого оборудования позволяет выполнить мастеру чертеж с нуля, если у него есть опыт.
Можно рассмотреть станок «Улитка». Используя его можно создавать различные спирали или волны. Для создания такого станка нужно иметь чертежи на станок для холодной ковки своими руками такого типа, а так же делать все в соответствии с технологией. Рабочая поверхность должна состоять из листового металла. 4 мм толщины будет достаточно. Размеры устанавливаются исходя из габарита детали. Для придания форму необходим листовой металл в толщину 3 мм и в виде полос. Он выгибается по шаблону плоскогубцами и получается спираль.
Для создания нормального процесса работы нужно хорошо зафиксировать один из концов детали. В этом поможет прут, равный ширине полос. Чтобы зафиксировать рабочую площадку нужно будет использовать верстак. Основная цель всего – придать максимальной неподвижности детали, потому что во время холодной ковки нужно приложить большие усилия.
Перед началом изготовления любого станка для холодной ковки, инструментами для ручной работы нужны шаблоны, эскизы и различные чертежи, в том числе и чертеж на оборудование для холодной ковки своими руками.
Придать более хорошую точность разметке можно за счет миллиметровой бумаги. Нужно нарисовать на ней спираль, где будут увеличиваться витки в радиусе. Между ними нужно должным образом соблюдать равную дистанцию. Такое условие будет обязательным только для создания симметричных узоров.
Конструирование станка.
Для создания любого станка можно использовать несколько вариантов на выбор – разборный, монолитный или сплошной. По все длине бедующего станка рекомендуется приварить маленькие прутки. На рабочей площадке для этого стоит просверлить специальные дырки. Требуется хорошо закрепить концы деталей, которые будут выгибаться. Такой способ ковки очень популярен у новичков кузнечного дела.
Используя станок для холодной ковки металла, сделанного своими руками, неопытный мастер сможет изготовить кованые балконные козырьки, поручни для лестниц, различные решетки для окон, заборы, многочисленную мебель для дома, ограждения, различные кованые аксессуары и предметы декора, которые дополняют интерьер помещений, на подобии решеток под камины. Это хороший вариант для начинающих специалистов.
Коллекция чертежей станков для холодной ковки.
Чертеж для улитки с лемехом.
На чертеже представлено устройство гибочной улитки с лемехом и правила работы с ним
Гидравлический пресс для холодной штамповки
Гидравлический пресс для холодной штамповки
Описание продукта
Genaral Введение
Имеет черно-белое управление и ПЛК управления двумя видами электрической системы управления. Регулировка, ручной и полуавтоматический три режима работы могут реализовывать постоянное давление и принимать решения по двум направлениям.
При постоянном формировании давления, после подавления есть гарантии при прокатке и автоматическом возврате в движение.В рабочий стол загружается идет против рассрочки, кроме того идет против продукта. Все еще допустимое использование в качестве прокладки давления жидкости вместо растяжения формовочной машины заготовки, ее рабочего давления и графика движения, может в соответствии с необходимостью ремесла регулироваться в соответствии с установленным объемом.
Техническая производительность
1. Конструкция из трех балок и четырех колонн |
2. Три сварных балки сварены с обработкой отпуска |
3.Гидравлическая система с картриджным клапаном: долгий срок службы, меньшее гидравлическое воздействие и уменьшение точки утечки |
4. Гидравлическая система оснащена предварительным устройством для снижения гидравлического воздействия |
5.![]() |
6. Оборудован функцией постоянного хода и давления |
7.Рабочие функции и устройства: световая завеса, датчик смещения, рабочий ход и давление и цифровой дисплей, регулируемая скорость |
Применение
4-контактный волочильный пресс обычно используется для формования пластичных материалов и порошковых изделий; коррекция вала и других подобных деталей; прессование электрических деталей; обработка листового металла, штамповка и волочение; алюминиевые пряжки, встроенный потолок и так далее. Эта машина применяется в станкостроении, автомобилестроении, автомобильной промышленности, кондиционированных корпусах, механических подшипниках, порошковой металлургии и пластиковой промышленности.
- Автозапчасти: детали кузова, тормоза, топливные баки, ходовая часть, картер моста, бампер;
- Бытовая техника: стиральная машина, телевизор, холодильник, кондиционер, рисоварка и другие комплектующие;
- Кухонные принадлежности: мойка, чайный набор и другие виды посуды.
Главным образом компоненты
Назначение Y32 4-канальный чертежный пресс
Упаковка и доставка
Гидравлический пресс для холодной штамповки
Тип упаковки: деревянная упаковка или может быть отрегулирована для безопасности машины. |
Контейнерная упаковка: завернутый в пластик для защиты от намокания. |
Подробности упаковки: |
1) перед упаковкой станок в течение 48 часов проводит испытания, чтобы убедиться, что все оборудование соответствует требованиям 100%. |
2) перед загрузкой, стабильная упаковка, профессиональный и опытный грузчик уменьшают повреждение продукта при транспортировке. |
3) после погрузки наши профессиональные сотрудники, работающие с документами, будут выполнять заказ до тех пор, пока товар не выйдет из порта. |
Деталь поставки: 30 дней |
Наши услуги
Гидравлический пресс для холодной штамповки
- Служба запросов и консультаций : круглосуточное реагирование в течение 2 часов, предоставление решения в течение 2 часов один день и решить жалобу в 2 дня.
- Техническая служба : Инженеры могут обслуживать зарубежные машины. Мы отправляем техника на фабрику заказчика для установки и предварительной эксплуатации машин.(клиентам нужно только оплатить авиабилет и гостиницу)
- Гарантия качества Sevice : Мы предоставляем 5 лет гарантии . Мы подписываем договор с подробными техническими данными.
- Другие услуги : Скидка на долгое сотрудничество и приветствуется ваш визит на наш завод.
Информация о компании
Гидравлический пресс для холодной штамповки
О LVD-CNC
LVD-CNC полностью сосредоточен на предоставлении линейки продуктов и поддержки для максимизации производительности листового металла техник. |
Уже более 16 лет LVD-CNC специализируется на листогибочных прессах с ЧПУ, гильотинной и лазерной резке и штамповке, чтобы обеспечить цех полного производства листового металла и повысить точность производительности.![]() |
Компания имеет глобальную сеть из более чем 15 назначенных дистрибьюторов, обученных продавать и обслуживать станки LVD-CNC. |
Станки LVD-CNC изготавливаются в соответствии с нашим строгим набором стандартов проектирования и качества на современных производственных мощностях. |
Конструкции изделий LVD-CNC сочетают в себе точность, скорость, гибкость, долговечность, надежность и передовые технологии, чтобы поставлять станки с самым высоким соотношением производительности и цены в отрасли. |
Другие продукты LVD-CNC
и
. серво гидравлический алюминиевый глубокой вытяжки пресс обратной экструзии машина для холодной ковки$ 13 000.00 — 179 500,00 долларов / Устанавливать | 1.0 комплект / комплекты (мин. Заказ)
- Время выполнения:
Количество (Наборы) 1 — 5 > 5 Est. Время (дни)
45 Торг
- Персонализация:
Индивидуальный логотип (Мин.Заказ: 1 комплект)
Индивидуальная упаковка (Мин. Заказ: 1 комплект)Подробнее
Настройка графики (Мин.Заказ: 1 комплект)
Технические характеристики (Мин. Заказ: 1 комплект) Меньше
83,357 Товаров из 4 387
Цена FOB: US $ 9800-25000 / Piece
Мин.Заказ: 1 шт.
Цена FOB: US $ 58000-60000 / Комплект
Мин. Заказ: 1 комплект
Цена FOB: US $ 60000-100000 / Комплект
Мин. Заказ: 1 комплект
Чертеж простого станка для холодной ковки металла своими руками — как сделать ручное самодельное оборудование —
Станок для холодной ковки своими руками: чертежи и инструкции
Известными, благодаря наружному виду, считаются металлические изделия, которые сделаны методом ковки. Такой декор отличается ценой, поэтому не каждый может заказать их себе. Однако, помимо горячей технологии ковки, необходимой для изготовления деталей из металла, существует и холодная. Последний вариант есть возможность сделать самому, для этих целей потребуется изготовить станок для холодной ковки собственноручно.
Устройство станков для ковки по холодному типу
Конструкция станковЛюбой прибор для проведения ковки холодным способом обладает характерными чертами и качествами. Чтобы сделать качественный станок для холодной ковки своими руками, важно выяснить, как он устроен.
- Гибочные. Изменяя положение роликов и клиньев, изменяются габариты волн и изгибов. Из-за этого изгибаются прутья до 1,6 см. Единственным недостатком применяемого механизма станет невозможность изготовления его самому.
- Твистер. Снабжен спецшаблоном, к нему придавливают используемую металлическую часть. Сохранность шаблона обеспечивается упорным рогом.
- Основание с проставками. Прибор помогает делать любые узоры.
Конструкция отличается простотой, основой является пластиной из материала высокого качества, куда вкручиваются проставки на определенной дистанции. Этот тип прибора эффективен для металла в толщину 0,6 см.
- Улитки. Изделие является пластинкой-основой, где расположен спецвиток. Его применяют как шаблон для обрабатываемой детали. Характерной чертой станет то, что «улитка»-шаблон разделена на фрагменты, закрепленные друг с другом с помощью соединительных спецэлементов. Это даст возможность при работе шаблону менять форму, ввиду чего будут созданы разнообразные волны и изгибы. Для изготовления такого станка потребуется выбирать крайне надежный материал, которой не будет гнуться по прошествии времени.
- Торсионный станок. Подобное приспособление эффективно для винтового скручивания прута. Устройство делают из цилиндрического металлического каркаса и 2 фиксирующих элементов. Принцип работы заключается в том, что прутья помещают в крепежные элементы. С одной стороны их зажимают, а с другой закручивают до необходимых размеров винтовой волны.
Важно! До того, как создать устройство, необходимо ознакомиться с чертежами станка для холодной ковки.
Разновидности и назначение станков для ковки
Механизм облегчит работы вручную и создать уникальные изделия. Для ковки холодным методом мастера применяют различное оборудование, которое минимизирует физ. усилия человека и позволяет провести такие основные действия:
- согнуть профиль под необходимым углом;
- изготовить спирали либо завитки;
- скрутить детали вдоль.
Различные механизмы помогают создавать уникальные конструкции, художественное полотно для беседки, декор для скамьи в парке, прочие предметы разнообразного предназначения.
Виды приборовДекор-станки дают возможность создавать схожие по форме и параметрам детали за короткий временной интервал, помогают уменьшить их себестоимость и сроки изготовления.
Такие станки бывают профильными (выполняют лишь одно действие) и универсальными. Выделяют такие спецстанки:
- гнутики;
- улитки;
- торсионы;
- штамповочные.
Универсальные модели состоят из компонентов спецтехники в разных комбинациях.
Станок «улитка»
«Улитка»Алгоритм сборки станка для холодной ковки своими руками не вызовет сложностей. Во время создания улитки вероятны 3 типа конструкции, и то относительные. Каждый специалист делает завиток, спираль и изгиб изделия по-своему.
По виду исполнения механизмы бывают 3 видов:
- монолитные с фиксированным шаблоном изгиба;
- со съемным изгибом, дающим возможность делать различные завитки;
- с разборными составляющими завитка и крутящейся столешницей, чтобы получать сложные профили изгиба.
Монтаж станка начинают с конструирования основных узлов приспособления:
- Каркас. Механизм должен быть изготовлен из металла. Древесина совсем непригодна для сборки прибора: продолжительные и чрезмерные нагрузки разрушают дерево за несколько использований.
Как основной материал используется уголок, трубы с толстой стенкой либо швеллер.
- Столешница. Ее изготавливают из плиты из металла, которая вырезана в форме окружности, по толщине 0,4 см. Из такой плиты вырезают вторую столешницу, которая повторит по форме первую. На последней располагаются составляющие, производят изгибы заготовок. При холодной ковке столешница будет принимать большую нагрузку, потому не требуется экономить и создавать ее из тонколистового железа.
- Главный вал и рычаг. Вал расположен посередине, его окружают столешницы. Фиксируется к каркасу 4 треугольниками. Механизм сделан из трубы с толстой стенкой нужного диаметра. Рычаг крепят к валу посредством кольца и вращают вокруг его оси. Вспомогательно на него устанавливают ролик, чтобы сгибать прутья.
Станок торсионный
Обыкновенное скручивание ряд пользователей осуществляют, не используя станок. Зажимается одно окончание детали в тисках, а второе обращается благодаря стандартному вороту. При такой методике обрабатываемая заготовка скручивается, однако иногда и вытягивается. Во избежание этого, сооружается направляющая конструкция в качестве желоба. Необходимо учитывать:
- протяженность желобка – он не может быть длиннее детали, уменьшаемой во время деформации;
- ширину желобка – требуется, чтобы он вдвое был шире изделия, поскольку в процессе деформации оно увеличится.
Возможно достичь ожидаемых результатов без оборудования – в таких целях потребуется приложить усилия и потратить большое количество времени. Те, кто предпочитает собрать необходимое устройство, должны спроектировать такую спецтехнику.
Торсионный станокСборка такого станка собственноручно возможна в 2 вариациях: стандартная и универсальная. Первая станет улучшенным способом работ с тисками, а вторая предоставит шанс создавать уникальные детали.
Главное рабочее усилие, которое требуется, чтобы деформировать материал, принимает опора, потому основание создаваемого устройства должно отличаться высокой прочностью. В таких целях используется двутавр либо 2 швеллера, которые сварены друг с другом. Устойчивости для каркаса добавляют лапы, которые приварены к устройству. Затем возможно изготавливать остальные элементы – заднюю бабку и шпиндель.
В узлах механизма из профильной трубы своими руками находятся патроны, назначением которых станет их размещение внутри заготовки. Они должны обладать прочными фиксаторами (для надежного крепления). Ввиду уменьшения длины используемого изделия во время скручивания заднюю бабку выполняют скользящей. Допустимо сооружать ее из тисков, закрепляя на основании посредством болтов.
Подвижный элемент шпинделя проворачивают при помощи ручки, которая предусматривает наличие нескольких рычажков, имеющих необходимую длину для гашения прилагаемых усилий.
Сборка торсионного прибораВажно! Возможно добавить втулки из резины, чтобы защитить руки от скольжения.
Основным различием в алгоритме монтажа универсального прибора станет устройство подвижного элемента. Он предполагает винтовую подачу при изготовлении фонарей, фиксируется с помощью стандартного скручивания. Потому активный элемент снабжается 2 шпинделями. В этом варианте для скользящей бабки требуется фиксирующий винт.
Когда нужно сделать деталь, которая скручена лишь на конкретном фрагменте, к прибору добавляют ограничители. Их изготавливают по принципу задней бабки – присутствуют спецзажимы и есть опция скольжения.
Работы в такой ситуации крайне утомительны, получение изделий высокого качества представляет собой трудоемкий процесс. Потому оснащение электрическим приводом изделия станет наилучшим решением.
Станок «гнутик»
Приспособление отличается эффективностью, массивностью, простотой монтажа. Но существенным минусом станет то, что сложно отыскать и подогнать детали. Назначением устройства станет сгибание под различными углами детали, потому понадобится прикладывать значительные усилия на, следовательно, требования к монтажу станут выше.
Для каркаса приспособления подбирают толстую раму из стали. Следует учитывать, что устройство крепится к столу. В основном делается крепеж с помощью болтового соединения, к примеру, как в тисках. В середине рамы есть направляющая, отличающаяся подвижностью. Ее приводят в действие с помощью эксцентрикового механизма, фиксируемого на раме-каркасе. Вспомогательно устанавливаются 3 упора, которые создают необычную «вилку» – это рабочие составляющие устройства. С учетом профиля сгиба они меняются: круглые валы – чтобы выполнить волну, «молоток» – чтобы формировать углы.
Рабочие комплектующие изготавливаются лишь из особой стали. Они будут отвечать за прочность всей конструкции. Чтобы обрабатывать и подгонять изделия, понадобятся непосредственно спецнавыки и соответствующие инструменты. Потому, когда присутствуют трудности в заказе, при покупке либо изготовлении главных узлов, то рекомендуется приобрести устройство в магазине. Его цена не слишком высока, однако он может дополнительно использоваться, чтобы сгибать трубы.
Станок «волна»
Более логично называть рассматриваемое изделие управляемой волной. Устройство оснащается 2 стальными дисками в диаметре 14 см. Они фиксируются посредством болтов к столешнице. На основном диске закрепляется ось, которая вращает универсальный вороток.
Управлять рассматриваемым приспособлением нужно, меняя дистанцию меж дисков. Во время обкатывания воротом прута формируется узор. Когда прут снимают с кондуктора, образуется узор со второй стороны.
«Волна»Станок — пресс
Чтобы формировать наконечники прутьев, потребуется воспользоваться прессом. Рассматриваемое устройство функционирует аналогично маховику: изначально вращается штанга с грузиками, отводится винтовой боек до конца назад. Затем вставляется внутрь гнезда другой штамп и ставится обрабатываемое изделие. После, штанга быстро раскрутится в противоположный бок. Боек будет бить по хвостовой части штампа, вследствие чего образуется усилие необходимое в целях штамповки.
Детали, которые изготовлены методом холодной ковки, соединяют 2 методами:
- Сварка — изделия приваривают, окалину стачивают «болгаркой» либо иным оборудованием.
- Хомуты — подобный тип соединения выглядит значительно ярче.
Окрашивают заготовки, применяя спецэмали либо краски из акрила.
ПрессКак сделать своими руками станок для холодной ковки
Для монтажа станка для холодной ковки своими руками потребуется осуществить следующие действия:
- Сначала собирается стойка, выступающая в качестве опоры. В этих целях каждый элемент (фрагменты трубы аналогичных размеров и сочленения с верхней и нижней стороны) соединяются в одно целое. Устройство снаружи напоминает табуретку. Монтажные работы производят, используя сварочный аппарат, нарезку — применяя пилу.
- Теперь требуется нарезать металлические листы. Получатся круги одинакового диаметра и 4 треугольника, которые имеют одинаковые стороны. Треугольные составляющие привариваются к нижней части конструкции так, чтобы вышло что-то схожее с пирамидой. Основание с более широкой площадью приваривается к центру вырезанного круга.
- 4 планки, расположенные по горизонтали, присоединяются к окружности с приваренным элементом.
Подобное осуществляется, применяя болты (используют дрель для сверления отверстий).
- Последующим действием станет изготовление рукоятки. Требуется использовать 2 прута разной длины. Определяются их габариты методом соотношения с диаметра и окружности. Первый прут долен совпасть по размерам, второй несколько превышать его параметры. Во время сгибания первого прута требуется соблюсти необходимый угол. После этого углы привариваются между собой, затем вниз вваривается третий прут. Должна присутствовать перемычка меж начальных двух отрезков, к ним присоединяют спецрычаг.
- Подшипник для разнообразия направлений в приспособлении прикрепляется к окончанию приваренного рычага, к отрезку, который находится в нижней половине устройства. Верхний отрез играет роль крепления для металлической катушки (монтируется по горизонтали, помогает сгибать металл). Снизу отрезка, где находится свободное окончание, проделывается отверстие.
- Завершающим шагом изготовления станет монтаж изготовленной рукоятки с элементом, который напоминает «пирамиду».
Фиксируются такие детали после одевания рукоятки механизма с помощью гайки большого диаметра. На нее заранее приваривается круг из металла, дающий возможность закрепить шаблон. Затем «улитку» необходимо присоединить, используя сварочный аппарат. Теперь механизм будет готов к эксплуатации.
Соблюдая несложный алгоритм действий, домашний специалист или мастер сможет создать устройство высокого качества.
Для создания механизма самому требуется быть внимательным в процессе проектирования чертежей и произведения необходимых расчетов. В других моментах алгоритм изготовления простой. Установив принцип работы прибора, возможно придумать ему оригинальные вариации, способствующие улучшению обрабатываемых заготовок.
Кузнечное оборудование: станок для холодной ковки своими руками — RMNT
Холодная ковка невозможна без специального кузнечного оборудования. Давайте рассмотрим виды приспособлений и фигуры, которые можно получить с их помощью. Мы подготовили для вас чертежи и тематические видео. Также рассмотрим последовательность изготовления станка для холодной ковки своими руками.
Если вы только собираетесь организовать мастерскую холодной ковки и хотите избежать больших расходов, то самостоятельное изготовление станков и приспособлений поможет создать свой маленький бизнес без чрезмерных затрат.
Основные приспособления и станки
Станки для холодной ковки предназначены в основном для гибки по дуге или углом, а также для скручивания. Они могут быть ручные или с электрическим приводом.
Основные виды станков и приспособлений для холодной ковки:
- «Гнутик»
- «Твистер»
- «Улитка»
- «Глобус»
- «Волна»
- «Фонарик»
Приспособление «Гнутик»
Покупной или сделанный самостоятельно «Гнутик» — универсальное приспособление, позволяющее получить дугу или угол из прута. Он представляет собой основание с ползуном, на котором закреплен упор с углом (90° или другим по необходимости) и двумя цилиндрическими неподвижными упорами. Перемещая ползун и угловой упор, прут сгибается под углом.
Приспособление может быть выполнено на горизонтальной или вертикальной платформе.
Аксонометрия приспособления «Гнутик» — вертикальное расположение
Чтобы смасштабировать размеры, приводим чертёж нижней планки этого «Гнутика».
Планка нижняя
Это приспособление — универсальное. С помощью насадок на нем можно не только гнуть, но и резать, и пробивать отверстия. Но это уже будет следующим шагом.
Получение дуги на «Гнутике»
Получение угла на «Гнутике»
Так выглядит самодельный «Гнутик»:
Приспособление «Твистер»
«Твистер» — инструмент для скручивания прутков, в основном квадратного сечения, вдоль продольной оси. Это несложное приспособление может быть ручным и с электроприводом. Принцип действия: закрепляются оба конца прута, потом одно крепление начинает проворачиваться, скручивая металл до необходимой формы.
Внешний вид покупного ручного «Твистера»
Посмотрите фото самодельного «Твистера» с электроприводом, собранного с использованием электрооборудования бывшего в употреблении:
Для изготовления «Фонариков» и «Шишек» существует специальный станок, но для начала можно использовать и «Твистер», как это показано на видео (англоязычное, но всё предельно понятно).
Видео 1. Как сделать заготовку под «Фонарик» на «Твистере»
Приспособление «Улитка»
Инструмент «Улитка» предназначен для получения завитков (или спиралей) и «валют» (S-образных деталей). Встречаются различные конструкции.
Один из вариантов конструкции: 1 — лемех улитки; 2 — основа станка; 3 — прижимной валик; 4 — рычаг для управления прижимным валиком; 5 — крепление основы; 6 — палец для фиксации лемехов; 7 — паз для прижиного валика; 8 — ось рычага управления; 9 — пружина для прижатия валика; 10 — фиксатор для заготовки; 11 — ведущий лемех улитки; 12 — основная ось; 13 — рычаги
В результате должно получиться такое приспособление:
Ещё одна лёгкая конструкция, чтобы гнуть прокат сечением до 12 мм:
1 — сегмент улитки; 2 — эксцентрик; 3 — ручка; 4 — основание; 5 — направляющие полозья; 6 — ось; 7 — ползун; 8 — гайка оси; 9 — ось крепления ролика; 10 — ролик; 11 — приводная ось; 12 — направляющая эксцентрика; 13 — центральный сегмент улитки; 14 — барашек эксцентрика; 15 — основная ножка; 16 — соединительный штифт сегментов улитки; 17 — корректирующий винт; 18 — соединительное ухо сегментов улитки
Часто приспособление «Улитка» делают на опоре, особенно если гнуть нужно толстый прокат.
Несколько полезных видеоматериалов по самодельных станкам «Улиткам».
Вариант с массивным основанием на опоре:
Видео 2. Изготовление основания
Видео 3. Изготовление улитки
Видео 4. Работа станка
Вариант настольного приспособления:
Видео 5. Часть 1
Видео 5. Часть 2
Подробнее о таких конструкциях мы поговорим ниже.
Приспособление «Глобус»
Такое устройство внешне похоже на школьный транспортир и предназначено для изготовления дуг с большим радиусом изгиба из полосы, квадрата, круга или шестигранника. Сначала загибом фиксируется один конец заготовки, потом она изгибается по всей длине по шаблону. Принцип действия чем-то похож на работу закаточной машинки для консервации.
Внешний вид приспособления
Видео 6. Работа на «Глобусе»
Пользуясь исключительно мускульной силой, дугу большого диаметра можно изготовить на шаблоне, прикрученном или приваренном к верстаку. На нём хорошо гнуть полосу, трубу тонкостенную и т. д.
Шаблон
Приспособление «Волна»
Получить волнообразные изделия из заготовки круглого, квадратного, шестигранного сечения или трубки можно на приспособлении «Волна». Деформация заготовки происходит между вертикальными валками прокручиванием.
Приспособление волна и полученные изделия
Видео 7. Приспособление в действии
Приспособление «Фонарик»
На этом станке изготавливают заготовки элементов «Фонарики» или «Шишки», которые могут состоять из 4-х, 6-ти, 8-ми и более прутков. По принципу действия станок похож на «Твистер», но тут заготовки изгибаются вокруг направляющего вала, что формирует более правильную и точную конфигурацию изделия.
Приспособление «Фонарик»
Видео 8. Работа приспособления для изготовления «Фонарик»
Приспособление для холодной ковки элемента «Хомут»
Элемент холодной ковки «Хомут» предназначен для фиксирования между собой других элементов конструкции.
Приспособление для гибки «Хомута» можно выполнить по прилагаемым чертежам.
Приспособления для выполнения «гусиной лапки»
«Гусиная лапка» — расплющивание с нанесением красивых насечек концов заготовок для придания большей изящности конструкции или с целью уменьшения толщины для различных соединений.
Концы элементов оформлены «гусиной лапкой»
Эту операцию можно выполнить при помощи станка с матрицей или приспособлением и тяжелым кузнечным молотом на наковальне. Оба варианта мы даем в виде видеоматериалов.
Видео 9. Станок для изготовления «гусиной лапки»
Видео 10. Приспособления для ковки «гусиных лапок»
youtube.com/embed/HL0aAjztrsI?rel=1&fs=1″ frameborder=»0″ allow=»accelerometer; autoplay; encrypted-media; gyroscope; picture-in-picture»/>
Видео 11. Подробный процесс изготовления штампа
Ниже прокатный станок для выполнения той же операции.
Станок для прокатки «гусиной лапки» (расстояние между вальцами регулируется). Материалы для прокатного станка: шестерни и валы — запчасти от комбайна б/у
Принцип действия
Изготовление «Улитки» с приводом
«Улитка» с электроприводом облегчает изготовление завитков и «валют». Особенно это ценно, когда работа не «для души», а для изготовления большого количества однотипных изделий на потоке при работе на заказ.
Ниже приведены этапы сборки станка для гиба прута максимальным сечением 10х10 мм. Двигатель мощностью 0,5 КВт/1000 об/мин работает при этом на пределе своих возможностей. Выполняет 6 оборотов вала в минуту. Сегменты улитки выточены из круглой болванки Ст.45 без термообработки высотой 25 мм и толщиной 20 мм. Улитка насажена на вал на подшипниках от заднего колеса мотоцикла — 7204. Поддерживающий ролик закреплён жёстко в пазу. Между двигателем и редуктором установлены шкивы.
Ниже приведены чертежи сегментов улитки.
Элемент улитки 1
Элемент улитки 2
Элемент улитки 3
Центральный элемент улитки
Для более массивного прута (от 12 мм) мощность двигателя должна составлять более киловатта. На фотографиях ниже представлен станок с двигателем мощностью 2,2 кВт, 1000 об/мин, дающий выход на валу около 10 об/мин. Это уже станок для профессионального использования. Применён бывший в употреблении редуктор, матрица вырезана из заготовки толщиной 30 мм — самый трудоёмкий процесс.
Для холодной ковки ещё понадобятся наковальня и молот. Горн не нужен, он требуется только для горячей ковки.
Совет! Перед началом работ начертите эскиз будущей конструкции в натуральную величину. Это поможет корректировать элементы и не запутаться при сборке.
рмнт.ру
Станок для холодной художественной ковки своими руками: чертеж, инструкция и видео
Самодельный станок для холодной ковки может пригодиться, если вам нравиться мастерить и вы не прочь сделать своими руками что-то красивое для загородной усадьбы, домашнего интерьера, для подарков близким и родным людям или просто для души.Величественный внешний вид изделий, сделанных способом ковки, манит изящными линиями и завораживает взоры. Издревле, во всех лучших домах, можно было непременно увидеть такие украшения, как металлические ажурные завитушки. Да и сегодня, когда разработано огромное количество всевозможных материалов и технологий, кованые изделия не потеряли своей актуальности.Изделия, изготовленные с помощью ковки, используются в дизайне наряду со стеклянными, пластиковыми и иными элементами декора. Ковка металла происходит холодным или горячим способом. Для выполнения процесса горячей ковки нужно выполнить множество особых условий, потому ей очень сложно заниматься в домашних условиях. Более доступным способом является художественная холодная ковка. Научиться ей намного проще, а при желании можно сделать самодельные станки для холодной ковки своими руками.
Процесс холодной ковки
При холодном варианте ковки потребуется два основных процесса:
Чтобы провести данные мероприятия, не нужно сообщать металлу какую-то температуру. Но определенная термообработка все-таки должна происходить между этапами работ.Необязательно иметь в своем распоряжении полноценные станки для художественной ковки, часто любители изготавливают инструменты своими руками. С помощью самодельного оборудования можно придавать заготовкам всевозможные причудливые формы. Нужно только обзавестись определенными навыками работы. Поэтому готовьтесь к тому, что для того, чтобы согнуть требуемую фигуру, будут необходимы чертежи и немалые усилия. Выполнение работ возможно только с использованием сырья необходимой толщины.
Изделия, которые получаются с помощью самодельного станка для холодной ковки, намного крепче тех, которые выполняются или отливаются с помощью штамповки. Так происходит за счет того, что металлические прутья, которые проходят через оснастку, прессуются вместе с приданием им необходимой формы. При этом способе ковки нужно не допускать ошибок, так как они практически не исправляемы. С приобретением навыков вы сможете создавать своими руками привлекательные и замечательные изделия.
С помощью самодельного станка для холодной ковки, можно изготавливать такие изделия, как:
- элементы вроде балконных козырьков, поручней для лестницы;
- решетки на окна;
- ограды и заборы;
- мебель для дома – столы, стулья, кровати;
- элементы, которые используются в дизайне дома: обрешетки каминов, треноги для цветов.

При обработке большой партии однотипных изделий своими руками все можно сделать при помощи трафаретов и чертежа. Так удается значительно уменьшить трудозатраты и сократить время изготовления. Иногда детали необходимо нагреть, прогревание делают на участках стыков, чтобы не было кривизны. Новичкам рекомендуется перед выполнением работ тщательно продумать план изготовления, нелишним будет видео урок и выполнить чертеж будущего изделия.
Инструменты и оборудование
Ручной станок для выполнения холодной ковки включает ряд элементов. Необходимые приспособления, которые понадобятся для работы:
- твистер;
- улитка;
- гнутик;
- волна;
- глобус;
- фонарик.
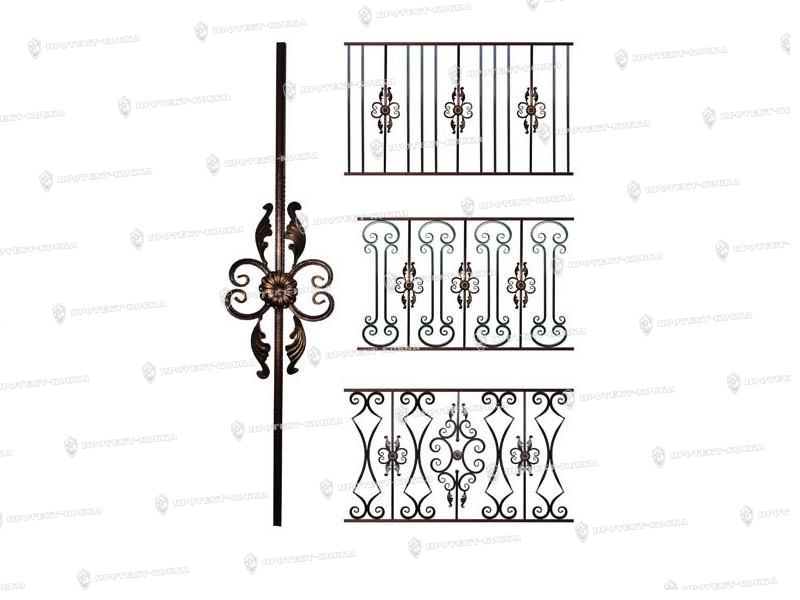
Главным инструментом для работы будет гнутик, который используется для изменения формы металла. Его функция — изгиб детали под необходимым углом или изгиб дуг с различным радиусом.
Улитка используется, как правило, для свивания в спирали стальных прутов. Это оснастка для сгибания прутков, полос, трубок, квадратов и профилей до формы спирали, изделий с различными формами и радиусом. Во время использования этого инструмента можно не ограничивать в радиусе создаваемую спираль и сделать ту величину, которая требуется.
Инструмент «фонарик» необходим для сгибания металлических деталей. С помощью него обрабатывают металлические прутки, сечение которых менее 30 мм, или квадратные профили сечением менее 16 мм.
При помощи такого устройства, как волна, делают волнообразно выгнутые элементы. Применяют его и для обработки труб, которые имеют шестигранное или круглое сечение.
Твистер похож чем-то на фонарик. При помощи этих двух инструментов можно выкручивать прутья вокруг оси.
С помощью глобуса можно выполнить большую дугу из профильного прута толщиной до 12 мм. Причем концы заготовки также плавно сгибаются.
Этот инструмент для холодной ковки абсолютно не сложный, поэтому зачастую можно увидеть и самодельный. Заводскому он почти ни в чем не уступает.
Станки для ковки
Зачастую при работе, сделать станки для холодной ковки своими руками представляется гораздо целесообразней. Так как не каждый элемент можно полноценно обработать с помощью лишь ручного оборудования для ковки. Да и цена этого оборудования довольно большая, даже когда речь идет о простейшем станке улитке.Если домашний умелец сделает какое-то изделие на самостоятельно изготовленном кондукторе, то вещь будет уникальной, хотя по некоторым параметрам и будет уступать той, которая сделана в заводских условиях. Если планируется делать большое количество деталей с помощью холодной ковки, то лучше всего сделать кондуктор с электромотором. Так вы облегчите себе рабочий процесс.
Полезным будет предусмотреть изготовление на станке основных видов работ – вытяжки, гибки и закручиваний. Эти устройства можно объединить во время создания кондуктора своими руками.
Во время вытяжки изделию придается определенная форма. Для чего ее нужно пропустить через валики или пресс, причем сечение исходного сырья уменьшится.
Процесс гибки состоит в том, что деталь гнут под требуемым углом. Выполнить эту операцию можно с помощью шаблонов. Они делаются таким образом: подготавливается чертеж изделия, по которому после делается шаблон. На стальную пластину приварите завитушку, после этот лист крепится на станке в держателе. Окончание заготовки устанавливают в прорезь, второй конец фиксируется. С помощью рычага происходит воздействие на один конец изделия, которое нужно протащить по всем изгибам пластины, используемой в роли шаблона.
Делая шаблон, сварочный шов нужно проводить с внешней стороны, иначе он будет мешать при дальнейшей эксплуатации изделия.
Часто мастера сами собирают простые устройства, с помощью которых можно изготавливать довольно оригинальные изделия. Тут все зависит от опыта мастера. Рассмотрим одну из таких самодельных моделей, чтобы понять сам принцип.
Станок «Улитка» для ковки своими руками
С помощью этого станка домашние мастера выполняют всевозможные кольца и спирали, завитушки, волны. Чтобы сделать этого рода станок, нужно действовать согласно чертежам и технологии, которая включает в себя ряд этапов.Прежде чем делать любые приспособления, ручные инструменты или станки для художественной ковки, требуется выполнение графических изображений, шаблонов, эскизов, чертежей будущего приспособления.
Чтобы более точно получилась разметка, лучше всего пользоваться миллиметровой бумагой. Нарисуйте на ней спираль, у которой постепенно увеличивается радиус витков. Между витками нужно соблюдать одинаковый шаг. Нужно сказать, что это условие необходимо соблюдать только в случаях, если нужна симметричность узоров, как правило, делают не более 4 шт.
Также учитывайте и то, какие будут заготовки, с которым нужно работать. Дистанцию между витками нужно сделать так, чтобы она немного превышала диаметр металлических прутьев, иначе сложно будет доставать из станка готовое изделие.
Для рабочей поверхности будет необходимо листовое железо. Толщина в четыре миллиметра вполне хватит. Определение размеров происходит на основании габаритов необходимых деталей. Чтобы сделать форму, потребуется листовой металл в виде полос толщиной три миллиметра. С этим материалом можно работать с помощью ручных инструментов. Его просто выгибают по шаблону в спираль с помощью плоскогубцев.Чтобы создать полноценный процесс работы, необходимо сделать надежную фиксацию одного конца изделия. Тут понадобится кусок прута, который равен ширине полос. Для фиксации рабочей площадки потребуется верстак. Часто в роли стойки используют кусок толстостенной трубы. Главное – обеспечить максимальную фиксацию, так как при холодной ковке усилия прилагаются довольно большие.
Сборка станка
Чтобы сделать любой станок для холодной ковки, существует множество вариантов. Можно его изготовить разборным, монолитным или сплошным. При монолитной конструкции устройство целиком или части «Улитки» привариваются к площадке.По длине конструкции можно приварить небольшие кусочки прутков с расстоянием 5-6 см, в рабочей площадке для них нужно сделать специальные отверстия. Не забывайте тщательно крепить концы изделий, которые будете выгибать.
Холодная ковка является особенно популярной среди начинающих в кузнечном деле. Для изготовления изделий этим способом не нужно ни хорошо оборудованной мастерской (можно обойтись гаражом или сараем), ни обладания большим опытом, не нужны особые знания о поведении металлов. Что касается приспособлений, то все необходимые станки и инструменты можно изготавливать своими руками в домашних условиях.
размеры, эксплуатация, изготовление своими руками
Люди занимаются обработкой металла не одно тысячелетие. Известно две основных технологии обработки — горячая и холодная ковка. Первый метод требует использования нагревательного оборудования для плавки или разогрева металла. Вторая технология выполняется с помощью специального оборудования. Станки для холодной ковки — это простые конструкции, которые можно изготовить самому.
Станок для холодной ковкиПроцесс холодной ковки
Холодная ковка — простой технологический процесс обработки металла. Кузнец изгибает детали используя ручные установки. Работа проводится с помощью рычагов, которые уменьшают человеческое усилие, передаваемое на материал. На выходе получаются более прочные изделия, чем при отливке. При холодной ковке станок одновременно гнёт и прессует заготовки.
Изменение формы металлических деталей без нагревания применяется при изготовлении:
Оборудование для сгибания металлических заготовок позволяет создавать изделия разной формы. Сложные металлоконструкции изготавливаются из отдельных деталей с помощью сварочного аппарата.
Виды станков
Существуют разные виды кузнечных станков, с помощью которых можно изменять металлические заготовки. Это конструкции рычажного типа, которые можно собрать самостоятельно. Для этого нужно разобраться в принципе работы отдельных моделей.
Улитка
Это ручной агрегат для создания завитков, спиралей из металлического прута. Самодельные станки улитка для холодной ковки присутствуют во многих мастерских. Чтобы сгибать заготовки малого размера, используется специальный кулачковый механизм.
Торсионный
Приспособления для холодной ковки, с помощью которых скручивают металлические прутья разного размера. Кузнец может изгибать по спирали один прут или объединять несколько в один. Представляет собой литое основание, на котором закрепляются два вида тисков. Одни неподвижные с воротом, вторые передвигаются по основанию. Тиски предназначены для закрепления прутьев. Далее кузнец закручивает ворот до нужного положения.
Чтобы скручивать несколько заготовок вместе, используется оборудование с установленными двигателями. Такие конструкции снижают усилия человека при работе с заготовками до минимума. Механизированные агрегаты эффективнее изгибают металлические детали.
Гнутик
Это ручной станок для ковки металла. Считается основным механизмом для сгибания прутьев под разными углами. Конструкция станка для ковки металла представляет собой металлическое основание, на котором закрепляются два неподвижных вала, а между ними подвижная деталь. С помощью подвижного элемента кузнец выбирает угол, по которому будет сгибаться заготовка.
Станок гнутикВолна
Ручное оборудование. Позволяет изгибать металлические заготовки по форме волны. Представляет собой ряд металлических дисков, которые расположены по одной прямой. Расстояние между ними может изменяться зависимо от требуемых изгибов волн.
Пресс
Чтобы делать плоские окончания на металлических изделиях, используется самодельный пресс. Он представляет собой два диска, которые объединяются между собой системой шестерней. Арматура закрепляется одним концом между дисками. Кузнец начинает вращение с помощью ручки.
Изготовление
Сборка самодельных станков для холодной ковки своими руками не доставляет больших трудностей. Сделать станок для холодной ковки своими руками можно в несколько этапов:
- Подготовить чертежи. Если это многофункциональный универсальный станок, схемы отдельных элементов можно найти в интернете. Объединить их на одном рисунке, обозначить места скрепления, проводов.
Нельзя забывать про указание размеров.
- Подготовить инструменты, расходные материалы. Например, для изготовления улитки понадобится кулачковый механизм, спираль из твердосплавного металла. Для волны нужны металлические диски, для торсиона — тиски.
- Следующий этап — сборка конструкции, на которой будут закрепляться другие детали. Чтобы соединить металлические детали, необходимо использовать сварочный аппарат. Швы зачищаются с помощью болгарки, покрываются защитным составом.
- На готовой конструкции закрепляются подвижные элементы, которые будут взаимодействовать непосредственно с заготовкой.
- Прежде чем начинать работать нужно проверить надёжность креплений.
Несмотря на многообразие чертежей и инструкций, часто качество самодельных станков оставляет желать лучшего, а учитывая количество потраченного времени, многие выбирают вариант покупки заводского оборудования.
Цены на станки для холодной ковки сейчас на очень низком уровне благодаря компании Stancraft, которая разработала и запустила в массовую продажу универсальный комплект ручных станков, что бы их мог позволить себе любой дачник.
На их официальном сайте stancraft.ru есть такие станки, как «Улитка», «Торсион+Корзинка», «Гнутик», «Профилегиб». Если Вам хочется максимально быстро начать работать на станках, самый простой способ — заказать на сайте stancraft.ru.
Эксплуатация
Чтобы не испортить материал и оборудование, нужно знать ряд особенностей. Кузнецы дают такие рекомендации:
- Прежде чем начинать работать нужно проверить целостность крепёжных элементов.
- Подвижные детали необходимо периодически смазывать моторным маслом. Это обеспечит надёжную работу оборудования.
- Чтобы проще было изгибать заготовки из металла, можно делать предварительное разогревание материала.
- При сгибании деталей движения должны быть плавными. Самодельные станки не настолько надёжны как покупное оборудование.
- Нельзя надеяться на высокую точность самодельного агрегата.
После сваривания металлических элементов конструкции нужно зачистить швы. Покрыть их антикоррозийным составом. На самодельном оборудовании для холодной ковки изготавливаются отдельные детали металлоконструкции. Кузнец располагает их на рабочем столе так, как они будут расположены в готовом изделии. После этого он должен соединить их с помощью сварочного аппарата.
Самодельные станки для холодной ковки популярны в частных мастерских, гаражах. Кузнецы изготавливают с их помощью разные кованые изделия сложной формы. Для сборки не нужно обладать дополнительными навыками. Достаточно сделать чертёж, подготовить материалы, инструменты, провести поэтапную сборку.
самодельные кондукторы, матрицы и другие инструменты, изготовление из профтруб и не только; гибка, сварка, сборка; видео
Кованая настенная вешалка-полка, украшенная листьями и завитками. Фото Царская Ковка
Кованые завитки являются универсальными декоративными элементами, применяющимися для дополнения дизайна разнообразных по форме изделий. Для изготовления деталей подобного типа используется механизированное оборудование, а также ручные инструменты и приспособления. Некоторое оснащение продается по достаточно высоким ценам. Но существует также возможность изготовления (сборки) оборудования своими руками.
Изготовление самодельных вертикальных устройств из металла, профтрубы и других материалов, видео
Производство станков любого типа своими руками представляет собой сложное дело. Изготовление составных частей устройства, а также сборку следует осуществлять внимательно. Корректность гарантирует качество изготовляемых элементов и предметов из металла.
Как сделать улитку с электропроприводом и без, для холодной ковки и гибки завитков, волют, запятых
- Стол выполняется из стали, к нему с нижней части приваривается труба, к которой в свою очередь крепится подвижный рычаг, сделанный из профильной трубы 45х25, толщина стенок – 1,5 мм.
- Данная часть станка крепится к ножкам, опорам.
- К рычагу крепится дополнительная регулируемая часть, дополнительно усиленная угольником.
- В ровной поверхности, где предварительно сделаны отверстия, крепятся оправки (кондукторы), выполненные из квадратного прутка с сечением в 10 мм. и полосы.
- Изготовление оправок осуществляется по рисунку.
- Несколько отверстий позволяют располагать оправки разным образом, что позволяет гнуть элементы разных конфигураций и размера.
- Мастер демонстрирует процесс изготовления элементов.
Ручные инструменты и приспособления для изготовления кованых завитков
Изготовление ручных инструментов требует меньших затрат времени и расходных материалов. Подобные приспособления имеют более простое строение.
Матрица
- Для изготовления приспособления потребуется кусок швеллера длиной 25 см.: покупная или выточенная самостоятельно петля с диаметром 22 м. с втулкой из двух видов труб и элемента сложной формы, а также еще одной петли.
- Лекало подобного типа позволяет производить волюты разных размеров.
Кондуктор
- Для изготовления кондуктора потребуется полоса длиной 60 см. и шириной – 4 см.; кусок жести 16 на 16 см., толщина – 3 мм.; кусок угольника; небольшие вырезанные из рессоры элементы с закругленными углами и снятыми фасками. Из малых деталей сваривается деталь с углом в 90 градусов, для крепления заготовок при гибке.
- На полосе прорисовывается наклонная линия, часть заготовки позже будет удаляться.
- Полоса слегка гнется, к ней приваривается малый угольник, после этого гибка продолжается.
- Спираль крепится к основанию, к куску жести.
- Кондуктор фиксируется в тисках, лишняя часть обрезается болгаркой.
- С нижней части основания приваривается угольник, обеспечивающий крепление изделия в тисках.
Другое оборудование для ковки
Весь перечень оснащения для холодной ковки следует разделять на четыре отдельные категории, критерием для классификации выступает уровень автоматизации.
- Универсальное оборудование представляет собой автоматические или в некоторых случаях ручные установки, позволяющие обрабатывать заготовки с разным сечением. Такие многофункциональные машины служат заменой целому набору ручных устройств, использующихся для гибки профильных труб, квадратных и круглых прутков.
Важным достоинством подобных машин является возможность выпуска различных по форме элементов.
Станок для ковки Ажур-1М. Фото КовкаПРО
- Станки для холодной ковки предназначены для облегчения ручного труда. В перечень устройств кроме улитки входят гнутик, волна, твистер, глобус. Каждый агрегат предназначен для изготовления определенного вида элементов. Рычажное (ручное) управление позволяет снизить трудозатраты, но не исключить их совсем. Ручные станки применяются мастерами, которые занимаются ковкой в качестве хобби, так как производительность данных устройств не слишком высока. Для улучшения технических характеристик необходимо оснастить агрегат электродвигателем.
Станок для холодной ковки типа Волна
- Инструменты представляют собой простые предметы, ковка выполняется вручную, посредством применения силы. К инструментам относятся тяжелый молоток (кувалда), клещи, вилки.
Вилка кузнечная
- Приспособления являются более сложными предметами, представляют собой механизмы, к которым относятся кондуктор, шаблоны, лекала, оправки.
Самодельные модели, изготовление, как сделать, размеры
Кроме устройства типа улитка возможно также изготовить самостоятельно и другие станки для холодной ковки: фонарик, волна и прочие, в том числе и электрические. Приспособления в большинстве случаев делают своими руками. Самодельные модели разных видов и размеров позволяют осуществлять процесс холодной ковки своими руками и выпускать элементы необходимых конфигураций.
Купить
Исполнители, не уверенные в собственных навыках, имеют возможность приобрести станки для ковки заводского производства. Предприятия предлагают широкий выбор моделей ручных устройств: улитки, волны, фонарики, твистеры, прессы, гнутики, а также универсального оснащения.
Китайская машина для горячей и холодной штамповки, Китайские производители и поставщики станков для горячей и холодной штамповки на Alibaba.com
Механический ковочный пресс с управлением от ПЛК 200тонн с механическим кузнечно-прессовым прессом с ПЛК 200тонн Механический кузнечно-прессовый пресс с ПЛК 200тонн Фотографии Технические характеристики КОД АРТ. 800 1250 Ход слайда S мм 80120140160180 Ход слайда Фиксированный об / мин Время / мин 100 80 70 60 50 Переменный (опционально) об / мин Время / мин 60-100 50-80 45-70 40-60 35-50 Макс.Высота затвора матрицы h4 мм 250 270300320350 Регулировка высоты затвора матрицы t мм 50 60 70 80 90 Глубина горловины C1 мм 210 225 270 310350 Расстояние между колоннами d1 мм 450 515 560 610 670 Размер нижнего салазок FB b мм 250 340 400 460 520 LR a мм 360 410 480 540 620 Диаметр отверстия хвостовика d мм 40 50 50 50 70 Глубина I мм 65 60 70 65 90 Размер надрессорной балки FB D мм 400 440 520 600 680 LR C мм 720 825 930 950 1100 Толщина h5 мм 80 110130140155 Диаметр отверстия в кровати ¢ мм 150150150180200 Габаритные размеры FB A мм 1496 1585 1540 1765 2040 LR B мм 945 1075 1200 1200 1320 Высота H мм 2120 2391 2570 2725 3035 Мощность двигателя кВт 3 5.5 5,5 7,5 11 Вес (приблизительный) кг 2450 3550 5150 6450 9550 КОД АРТ. ЕДИНИЦА Jh41-160 Jh41-200 Jh41-250 Jh41-315 Jh41-400 Номинальная нагрузка Pe кН 1600 2000 2500 3150 4000 Ход скольжения S мм 200 220 220 220 250 Ход слайдов Фиксированный об / мин Время / мин 45 45 30 30 30 Переменный (опционально) об / мин Время / мин 30-45 25-45 20-30 20-30 20-30 Макс.
Высота закрытия штампа h4 мм 400 450 500 500 550 Регулировка высоты закрытия штампа t мм 100 110 120 120 120 Глубина горловины C1 мм 400 430 450 450 490 Расстояние между колоннами d1 мм 736 910 980 980 1050 Размер нижней части скольжения FB b мм 580 650 700 700 750 LR a мм 700880950950 1020 Диаметр отверстия под хвостовик Диаметр d мм 70 70 70 70 70 Глубина I мм 100100130130130 Размер надрессорной балки FB D мм 760840880880950 LR C мм 1175 1390 1500 1540 1700 Толщина h5 мм 165 180 190 190 210 Диаметр отверстия в кровати ¢ мм 220 250 270 270 290 Габаритные размеры FB A мм 2305 2600 2660 2720 2850 LR B мм 1420 1540 1640 1680 1750 Высота H мм 3215 3800 3865 3865 4150 Мощность двигателя кВт 15 18.5 22 30 37 Вес (приблизительный) кг 13600 19200 23200 26600 31600 Описание Ковочный пресс 200тонн Характеристики: 1. Стальной сварной корпус, закалка, высокая жесткость, точность и стабильность; 2. Вертикально расположенный коленчатый вал, компактная конструкция; 3. Коленчатый вал подвергается шлифованию после высокочастотной закалки; 4.
Удлиненная прямоугольная направляющая с поверхностью из бронзовой пластины; 5. Пневматический цилиндр с двойной балансировкой, который уравновешивает ползун и вес штампа для снижения шума и ударов; 6. управление PLC и импортный двойной предохранительный клапан; 7.Мокрое сцепление и гидравлический предохранитель от перегрузки.
Станок для холодной штамповки болта
Машина для холодной штамповки болта
Описание продукта
Применение формирователя холодной штамповки
Машина для холодной штамповки использует метод холодной штамповки, подходит для производства всех видов винтов, Специальная машина для обработки шурупов по дереву, внутренняя шестиугольная, вогнутая шестиугольная заклепочная заготовка. Машина может автоматически завершать подачу, правку, резку, формовку, штамповку.
Характеристики формирователя холодного болта
(1) Идеальный дизайн, простота в эксплуатации.
(2) Конструкция салазок с одной направляющей позволяет машине работать с высокой скоростью, а эффективность производства также высока.
(3) Основной монтажный комплект наших машин изготовлен из высококачественного материала, подвергнутого термообработке с высокой стойкостью к истиранию и низкой деформацией, машина долговечна и долговечна.
(4) Холодная высадка Машина использует систему принудительной подачи масла , чтобы убедиться, что все компоненты машины работают в пленках состояния масла, и машина может быть долговечной в течение длительного времени.
(6) Конструкция для выталкивания наружной формы, которая решает проблему блокировки винтов при спуске.
Поточный процесс станка для изготовления шурупов по дереву
Грубая линия → Проволока → Заголовок → Накатка резьбы → Термическая обработка → Покрытие (цвет) → Упаковка
(1). Протяните грубую линию к необходимому участку линии.(Волочильный станок)
(2). Отрегулируйте, изготовьте и сформируйте головку винта на высадочной машине. (Станок для нарезки резьбы)
(3). Отшлифуйте зуб на резьбонакатном станке и полностью сформируйте винт (Нарезной станок)
(4). Обрабатывайте шнек-полуфабрикат термической обработкой согласно стандарту (печь для термообработки)
(5). В соответствии с требованиями, технологическое покрытие и т. Д. (Цинкование)
(6). Упаковка и с завода
Формовщик холодного болта Подробное шоу:
000 000 000 000 000Упаковка и доставка
Упаковка: В стандартном деревянном ящике для экспорта
в течение 150002 дней после доставки .Условия оплаты :. 30% T / T при предоплате, оставшаяся сумма должна быть оплачена после того, как мы закончим производство. (Мы возьмем для проверки фотографии машин и упаковки)
У нас есть собственный фарвард. Мы можем своевременно проверить информацию о доставке. Вы также можете использовать свой экспедитор. Мы свяжемся с ним как можно скорее.
Информация о компании
Мы производитель, а не торговая компания.
Основанная в 1990 году компания Xingtai JUDU Technology Co., ООО специализируется на производстве всех видов оборудования. В то же время мы можем производить по желанию наших клиентов. Эта продукция экспортировалась в США, Германию, Пакистан и Австралию.
Емкость:
Основные рынки | Общая выручка | |||
Африка | 24% | 9015 9015 Южный Восток 9015 9015 Юг | ||
Южная Америка | 9% | |||
Восточная Азия | 10% | |||
Северо-Восточная Азия | 8% | |||
Европа | 7% |
Основные рынки | Общая выручка | |||
Африка | 24% | 9015 9015 Южный Восток 9015 9015 Юг | ||
Южная Америка | 9% | |||
Восточная Азия | 10% | |||
Северо-Восточная Азия | 8% | |||
Европа | 7% |
чертежи и видео — Обзоры оборудования для бизнеса
Изготавливать предметы холодной ковки не трудно. Нужно лишь приобрести хорошее оборудование из качественной стали, например, такое:
Кроме покупки ручного оборудования для холодной ковки многие задаются вопросом о самостоятельном изготовлении станков. Идея может оказаться удачной, если у вас есть опыт работы с металлическими заготовками, чертежами, качественным материалом для изготовления станков. В пользу самостоятельного изготовления станков для холодной ковки могут выступать и небольшие финансовые затраты на такое производство. Это позволит вам открыть свой бизнес в небольшом помещении, гараже, рядом с домом.
Для последующей работы необходим ряд станков, на которых вы будете скручивать металлические заготовки под углом, волной, улиткой, завитком, сердечком, изготавливать элементы фонарик и т.д. Чаще всего это несколько станков — улитка, гнутик, твистер, волна, объемная, фонарик. Остановимся подробнее на описании станка Твистер для холодной ковки металла и его изготовлении своими руками.
Станок твистер необходим для того, чтобы делать загиб металлической детали вдоль оси. Вот такие детали получаются на ручном станке твистер:
Также с помощью станка Твистер можно делать заготовки «Фонарик» и «Шишка»:
В данном видеоролике представлен универсальный станок для холодной ковки, который может выполнять и функцию скручивания прутка. Оборудование получилось легким и удобным в работе:
Следующее оборудование для производства «корзинок» из четырех заготовок методом скручивания, также может применяться для торсировки металлического прутка. Для работы на таком станке используются пруток металлический диаметром 6 или 8 мм, квадрат 6*6 или 8*8 мм. для изготовления «корзинок». Для торсировки применяют полосу 20*4 мм, квадрат 16*16 мм.
В данном видео вы увидите ручной станок для ковки, сделанный умельцем без токарных работ. Самодельное оборудование для ковки позволяет изготавливать «шишки», «фонарики», «корзинки». Для производства понадобится металлические пруты, уголки, трубки для вращения и скрутки.
Ковка металла своими руками | Строительный портал
Кованые изделия в архитектуре и дизайне интерьера пользуются высокой популярностью с давних пор. Решетки на окна и для каминов, ограда или балясины лестниц, выкованные из металла, всегда выглядят изысканно и привлекательно. Сегодня, несмотря на современные технологии в обработке металлов, металлические изделия ручной ковки популярны как никогда. Конечно, ковка металла своими руками – дело не из легких, и без должной подготовки трудно сделать красивое кованое изделие. Но тем, кто хочет овладеть этим древним ремеслом и готов к тяжелой физической работе, придется ознакомиться с видами и технологией ковки металла, разбираться в металлах для ковки, понимать процесс ковки и уметь обращаться с инструментом кузнеца.
- Ковка металла
- Металл для ковки
- Инструмент для ковки металла
- Ковка металла своими руками
Ковка металла
Ковкой металла называется процесс обработки металлической заготовки с целью придания ей определенной формы и размера. Фактически существует два вида ковки – холодная и горячая. Выполняя ручную ковку металла необходимо разбираться в обоих видах ковки, так как каждый обладает своими преимуществами и недостатками.
Горячая ковка
В процессе горячей ковки заготовка подвергается нагреванию до определенной температуры, при которой металл теряет свою прочность и становится пластичным. Высокая пластичность является основным плюсом горячей ковки. Она позволяет легко придать металлической заготовке определенную форму и размер. Также горячая ковка позволяет использовать большинство технологий самой ковки, что выгодно сказывается на разнообразии вариантов работ.
Но нагрев металла имеет и свои недостатки. В первую очередь это необходимость обустройства специального кузнечного горна и затраты на топливо для него. Это может стать реальной проблемой для тех, кто хочет заниматься горячей ковкой металла своими руками в городских условиях. К тому же, работа с огнем достаточно опасное занятие и требует повышенной пожарной безопасности. Еще одним фактором, который может существенно повлиять на выбор вида ковки, являются специфические знания по температурным режимам для ковки металла.
Холодная ковка
В отличие от горячей ковки, холодная ковка металла не требует обустройства горна для нагрева металла. Вся суть холодной ковки заключается в придании формы металлической заготовке путем её изгибания, опрессовывания и сварки. Холодна ковка несколько проще по выполнению, и для обустройства мастерской не требуется много места. Весь процесс создания готового изделия не требует использования высоких температур, что весьма положительно сказывается на общей безопасности.
Но холодная ковка имеет один существенный недостаток. Все работы приходится выполнять с определенными заготовками-полуфабрикатами без возможности исправить свою ошибку. Конечно, это касается не всех работ холодной ковки, но в большинстве случаев испорченная заготовка годится разве что для металлолома или учебного пособия.
В любом случае, в независимости от вида ковки, придется достаточно плотно ознакомиться с рядом важных моментов. Во-первых, это касается металлов и температурных режимов для их плавки и ковки. Во-вторых, необходимо знать и разбираться в технологиях ковки металла. Ниже мы рассмотрим, какие технологические приемы используются для ковки и как они применяются в работе.
Металл для ковки
Ручная ковка металла – достаточно трудоемкое и сложное занятие, требующее использования определенных металлов, а точнее, металлов с определенными характеристиками. Для ручной холодной или горячей ковки наиболее важной характеристикой является пластичность металла, ведь именно от нее зависит простота и удобство изменения формы заготовки. Но стоит отметить, что пластичность и прочность металла взаимосвязаны между собой. При увеличении одной из этих характеристик вторая уменьшается. Поэтому так важно разбираться в характеристиках металла и знать о составе заготовки.
Важно! Существуют и другие, не менее важные характеристики металлов. Но так как мы рассматриваем ковку декоративных изделий, таких как решетки каминов, балясины, оградки и прочее, то нет необходимости сосредотачиваться на устойчивости к износу, красностойкости и прочем, а также на легирующих элементах.
![]()
Для декоративной ковки используют следующие металлы: медь, латунь, дюралюминий, сталь, а также другие медные, магниевые, алюминиевые и никелевые сплавы. По сути, для ручной ковки используют мягкий ковкий металл, который можно легко согнуть или придать ему определенную форму. Для того чтобы подобрать наиболее легкий ковкий металл, необходимо заглянуть в Марочник Стали и Сплавов. В нем можно найти детальное описание всех металлов и сплавов с их характеристиками и составом.
Несмотря на то, что самый ковкий металл – это медь и её сплавы, мастера предпочитают использование черных металлов для холодной и горячей ковки. Такая позиция обусловлена высокой стоимостью цветных металлов. Ведь на ковку металла цена в большей степени зависит от стоимости изначальной заготовки, и не каждый может позволить себе приобрести ограду или балясины из меди. Выбирая мягкий черный металл для ковки, необходимо ориентироваться на стали с минимальным содержанием углерода, порядка 0,25 %. А также с минимальным количеством вредных примесей, таких как хром, молибден, сера и фосфор. Кроме этого следует избегать конструкционных и инструментальных сталей с высоким содержанием углерода от 0,2 % до 1,35 %. Такие стали наименее пластичны и плохо поддаются сварке.
Выбирая тот или иной металл, необходимо использовать Марочник Стали и Сплавов. Но если доступа к нему нет, то можно воспользоваться приведенными ниже таблицами для определения содержания углерода в стали. Сам процесс определения довольно прост, достаточно поднести заготовку к работающему точилу и посмотреть на сноп искр, а затем сравнить его с показателями в таблице.
Сегодня благодаря промышленному производству металла отпала необходимость в создании заготовок для ковки своими руками. Современные кузни используют уже готовую заводскую продукцию для холодной ковки. Наиболее часто используемые размеры заготовок следующие: 30х45 мм, 40х45 мм, 10х10 мм, 12х12 мм, пруты сечением 10 мм, 12 мм, 16 мм, 25 мм, 30 мм, 50 мм, листовой металл толщиной от 3,5 до 6 мм, круглые трубы 1/2″, 3/4″, 1″, профильные трубы от 20х20 мм до 30х30 мм.
Инструмент для ковки металла
Выполнение любых работ по ковке металла невозможно без специального инструмента. Кузнечный инвентарь для горячей ковки достаточно разнообразен и включает в себя наковальню, горн, различные молоты, клещи и прочее. Инструмент для холодной ковки несколько попроще и состоит из нескольких специальных станков. Конечно, современный инструмент, такой как сварочный аппарат, болгарка и шлифмашинка, используется как в холодной, так и в горячей ковке. Зная о назначении того или иного инструмента, можно правильно выполнять любые работы.
Инструмент для горячей ковки
- Горн. Без него в горячей ковке никак не обойтись. Ведь именно в нем заготовка может нагреваться до температуры 1400 °C. В большинстве своем горн представляет собой печь, рассчитанную на высокие температуры и с поддувом.
- Наковальня. Этот инструмент является опорой, на которой выполняется ковка.
Сама наковальня имеет несколько видов, среди которых наиболее популярной является двурогая наковальня весом 200 кг. Но вес может колебаться от 150 до 350 кг.
- Шпераки. При выполнении различной художественной и декоративной ковки используются именно шпераки. Они имеют множество различных видов, и каждый мастер может изготавливать их под себя. Общей чертой любого шперака является то, что они вставляются в квадратное отверстие наковальни или закрепляются в деревянное бревно. На фото ниже приведены наиболее распространенные шпераки.
- Кувалда и Ручник. Это основной инструмент кузнеца. Кувалда весит от 4 до 8 кг и служит для нанесения сильных ударов. В зависимости от типа работ и толщины заготовки подбирается и вес кувалды. Ручник весит от 0,5 до 2 кг. Используется для придания окончательной формы изделию.
- Клещи. Горновые клещи второй по значимости инструмент. Без них невозможно удержать горячую заготовку для обработки.
Существует несколько видов горновых клещей под определенный профиль и размер заготовки. На приведенном ниже фото изображены горновые клещи различной формы.
- Фасонные молотки. При выполнении художественной ковки требуется создавать загнутые заготовки или заготовки определенной формы. Для этого используются фасонные молотки. Они могут быть как нижними, на которых производится обработка, так и верхними. Вариантов фасонных молотков множество и у каждого мастера они свои. На фото ниже изображен основной вспомогательный инструмент.
Кроме описанных выше, используются различный измерительный инструмент, такой как обычная рулетка, двойной кронциркуль, кузнечный наугольник, шаблоны и калибры. Выбор кузнечного инструмента огромен, весь перечислить представляется затруднительным, поэтому у каждого мастера есть свой набор лишь необходимого и часто используемого инструмента.
Инструмент для холодной ковки
- Гнутик (фото ниже). Это базовый инструмент холодной ковки. Как следует из названия, он позволяет гнуть металлическую заготовку под определенным углом. В дополнение гнутик позволяет создавать дуговые элементы определенного радиуса.
- Улитка. Название говорит само за себя. При помощи улитки можно создавать различные спиралевидные декоративные элементы. Спираль выполняется под определенный шаблон, который при необходимости можно сменить на другой, с меньшим или большим радиусом.
- Фонарик. Этот станок предназначен для создания декоративного элемента с одноименным названием.
- Волна. Позволяет создавать волнообразные элементы. При протаскивании прута через этот станок на выходе получается красивая синусоидальная заготовка.
- Твистер. По принципу работы этот станок схож с Фонариком, но в отличие от него твистер лишь скручивает заготовку вдоль оси.
- Станок для колец. Как во всех предыдущих станках название говорит за себя.
Кроме описанных выше существуют еще универсальные станки для клепки, резки, опрессовки и придания объема. Все описанные выше станки можно изготовить как самостоятельно, так и приобрести в магазине. Конечно, самодельные приспособления для холодной ковки будут несколько уступать по качеству заводским, но это компенсируется уникальностью созданных с их помощью элементов. Для изготовления станков холодной ковки чертежи можно найти как в свободном доступе, так и купить у специалистов.
Важно! Станки для холодной ковки могут быть ручными или снабжены электродвигателями. Несмотря на наличие передаточных шестерен, ручная холодная ковка довольно трудоемкое и долгое занятие, и для получения больших объемов кованых элементов лучше оборудовать станок электродвигателем.
Отдельно стоит отметить промышленные станки для холодной ковки. На подобные станки холодной ковки цены порядка 6000 у.е., но один такой станок может выполнять практически все технологические операции холодной ковки. Примером может служить станок Мастер 2 компании «МАН». На демонстрирующем холодную ковку видео можно увидеть возможности этого станка.
Ковка металла своими руками
В процессе ковки для придания заготовке определенной формы используются различные приемы и методы ковки. Для выполнения каждого из них используется определенная технология и инструмент для ковки металла. Технология ковки металла горячим и холодным методом существенно отличается. Как уже отмечалось, для горячей ковки требуется нагрев заготовки для изменения её формы, а при холодной ковке заготовка лишь изгибается. На основании этого и выделяются основные технологические приемы, зная которые можно смело браться за ковку металла своими руками.
Холодная ковка металла своими руками
Выполняется холодная ковка своими руками достаточно легко и особых усилий не требуется. Все работы разбиты на несколько этапов: создание эскиза или чертежа будущего изделия, закупка материалов и сам процесс ковки металла.
Чертеж можно создать в специальной компьютерной программе, приобрести уже готовый или нарисовать от руки. Можно найти для холодной ковки чертежи бесплатно. Для этого достаточно обратиться к мастерам, которые уже не первый год занимаются ковкой, и попросить один или два чертежа для тренировки. По сути, чертеж преследует несколько целей. Во-первых, чтобы знать какие элементы потребуется изготовить путем холодной ковки. Во-вторых, имея на руках такой проект, можно рассчитать количество и тип металлических заготовок, таких как пруты, профильные трубы и прочее. В-третьих, чертеж потребуется для сборки всех элементов в единое целое.
Отдельно необходимо рассмотреть элементы холодной ковки, из которых состоит проект. Сегодня можно найти довольно много различных кованых элементов, но их все можно объединить в несколько классических групп.
- Лапки. Этот элемент представляет собой раскатанный в какой-либо форме конец металлического прута. В эту группу входят так называемые Пики. Несмотря на заостренный конец, Пики изготавливаются по схожей технологии.
- Завитки. В эту группу входит несколько распространенных элементов: волюта, червонка и улитка. Волюта или Баранка представляет собой прут, концы которого загнуты в одну сторону. Червонка – прут, концы которого загнуты в разные стороны. Этот элемент иногда называют «долларом» из-за его схожести со знаком американской валюты. Запятая или Улитка – простой завиток, один конец которого загнут, а второй прямой.
- Кольца. Создается этот элемент довольно просто: на болванку станка накручивается прут круглого или квадратного сечения, в результате получается пружина, которую затем разрезают на отдельные кольца.
- Торсион. Этот элемент довольно легко узнать по винтовому скручиванию вдоль оси. Вариантов торсионов довольно много и одним из самых распространенных является такой элемент, как Фонарик, а также простой винтообразный прут для решетки или ограды.
Весь процесс изготовления элементов холодной ковки основывается на следующих общепринятых технологиях ковки – гибка, закручивание, вытяжка.
Вытяжка – это технология, которая заключается в увеличении длины заготовки путем уменьшения её сечения. В холодной ковке используется один из вариантов вытяжки – раскатка. Именно с её помощью создаются различные лапки и пики. Для создания лапок используется специальный раскаточный станок. Конец заготовки заводится внутрь и затем запускается механизм раскатки, в результате конец получается расплющенным с рельефом или без него. Для изготовления пик используют прессовочный станок. Процедура та же, но в результате конец получается раскатанный и опрессованный в определенной форме.
Гибка. Эта технология ковки заключается в загибании концов либо другой части заготовки под определенным углом. Сама гибка выполняется практически на всех станках холодной ковки. Процесс гибки можно проследить при изготовлении заготовки на станке Улитка. Вначале конец заготовки помещается внутрь специального шаблона и затем загибается под определенным углом. Эти работы выполняются на станке Улитка.
Закручивание. Эта технология ковки подразумевает скручивание заготовки вдоль своей оси. В холодной ковке этот процесс можно наблюдать при использовании станка Твистер, на котором создаются различные торсионы. Для этого один конец заготовки помещается в тиски, а второй конец проворачивается вдоль оси. Отдельно стоит выделить элемент Фонарик. Для него используют два и более прута, которые вначале скручивают вдоль оси, а затем вдоль оси сжимают, в результате прутья в определенном месте расходятся в стороны.
Сборка всех элементов в единую конструкцию выполняется при помощи сварки на специальном сборочном столе. Сегодня сварочный аппарат общедоступен и является обязательным инструментом современных кузнецов. Самодельная холодная ковка довольно распространена среди начинающих мастеров и частных предпринимателей. Она не требует особых знаний, навыков и больших помещений для работы.
Холодная ковка своими руками: видео-урок
Горячая ковка металла своими руками
По сравнению с холодной, ручная горячая ковка намного сложнее и требует от мастера опыта в обращении с инструментом и хорошей физической подготовки. Работы выполняются в несколько этапов: создание эскиза или чертежа, закупка материалов и ковка.
По сути, разница между горячей и холодной ковкой заключается в технологических процессах обработки металла. Во-первых, это касается способа обработки. Во-вторых, для горячей ковки можно использовать практически любые металлические заготовки. Но для удобства принято использовать уже готовые пруты квадратного и круглого сечения. В-третьих, в художественной горячей ковке отсутствуют какие-либо рамки для элементов готового изделия. Конечно, можно придерживаться создания классических элементов ковки – завитков, лап, пик и прочего, но горячая ковка позволяет использовать весь потенциал воображения мастера, что раскрывает неограниченные возможности. Все изделия из металла ковки горячим способом создаются с помощью следующих технологий обработки металла: осадка, вытяжка, гибка, закручивание, разрубка, насечение рисунка и набивка рельефа.
Осадка применяется при ковке металла для увеличения поперечного сечения всей заготовки или её части. При ковке в зависимости от необходимости проводится полный или местный нагрев заготовки для осадки.
Вытяжка заключается в увеличении длины заготовки путем уменьшения её сечения. Это можно выполнять как путем нанесения ударов кувалдой или ручником, так и с помощью раскатки металла между валов на станке. В отличие от холодной ковки создание пик при помощи вытяжки требует точных и аккуратных ударов.
Гибка. Эта операция выполняется для придания заготовке загнутой формы. При этом следует учесть, что гибка толстых заготовок может повлечь их искажение и для придания первоначальной формы необходимо выполнить осадку. Для гибки заготовки применяют различные шпераки, рог наковальни, фасонные молотки и кондукторы.
Закручивание. Данная технология ковки подразумевает скручивание заготовки вдоль своей оси. Как и в холодной ковке, заготовку зажимают в тиски и проворачивают. Но в отличие от холодной ковки, можно нагревать заготовку локально, что дает возможность легко делать локальное закручивание.
Такие технологии ковки как разрубка, насечение рисунка и набивка рельефа применяются в художественной ковке с использованием зубил. Края горячих заготовок, в зависимости от проекта, рассекаются и закручиваются клещами. Также пока заготовка раскаленная, на её поверхности набивается различный узор.
При горячей ковке металла важно знать температурные режимы нагрева. Это поможет более качественно обрабатывать металл. Ковка черного металла выполняется при 800 – 1250 °C. Конечно, измерять градусником раскаленную заготовку будет невозможно и для определения температуры придется ориентироваться по её цвету. В приведенной ниже таблице указаны температуры и цвет заготовки из черных металлов.
Горячая ковка металла: видео-урок
Ковка металла своими руками – дело довольно увлекательное, требующее постоянного совершенствования. Это касается в первую очередь создания различных художественных и декоративных элементов. Тем, кто только начал заниматься ковкой, придется немало потрудиться, чтобы их работы имели идеальную форму и высокое качество.
Комбинированная глубокая вытяжка и холодная ковка: процесс волочения [20]; a.
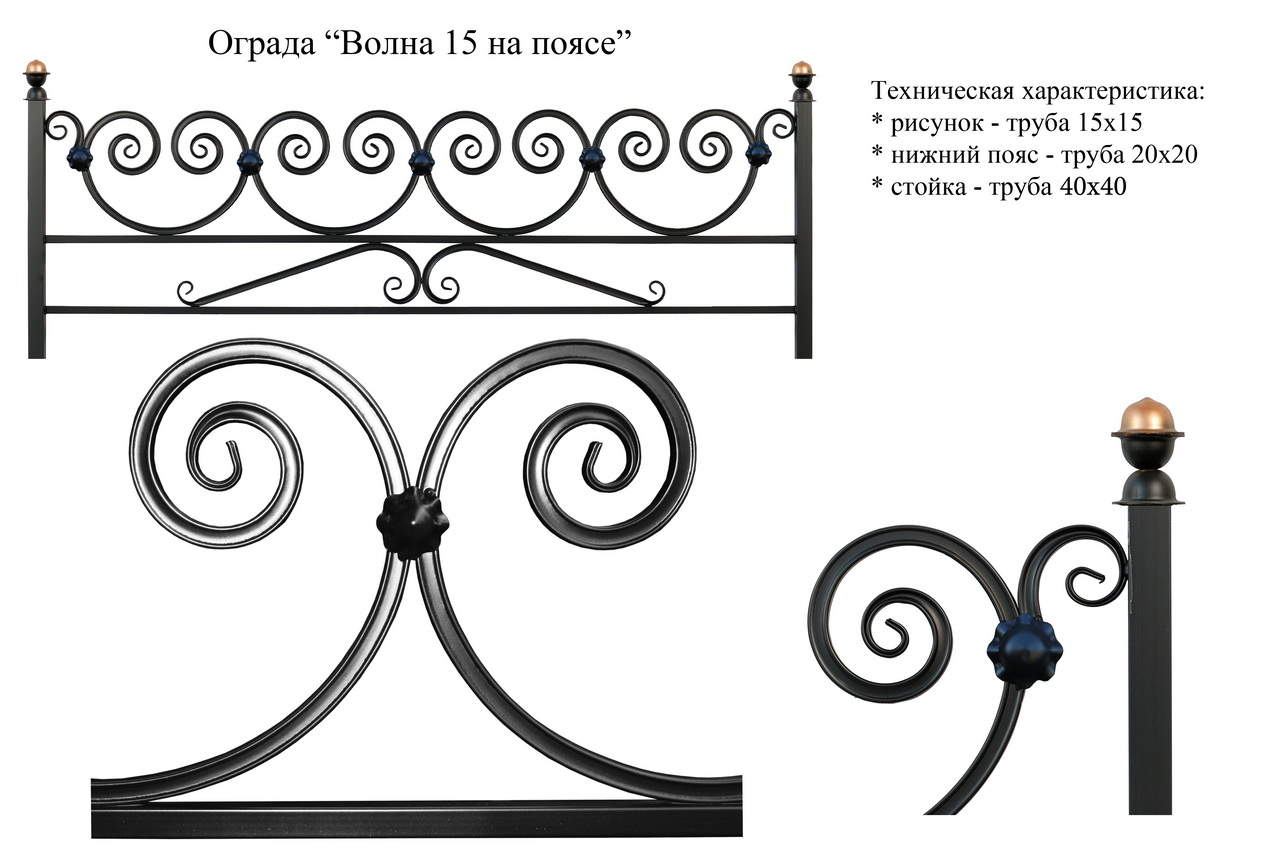
Context 1
… для изготовления многокомпонентных компонентов представлен Napierala et al. [20]. Окончательный комбинированный процесс глубокой вытяжки и обратного формования [19] состоит из двух частей: холодного экструдированного внутреннего сердечника и внешней оболочки, которая состоит из глубокой вытяжки и перетянутой чашки. Основной технологический принцип этой комбинации процессов показан на рис. 7. На рис. 7 d B — диаметр заготовки; t B – толщина заготовки; d C – диаметр сердечника; r C – радиус края сердцевины; r DD – радиус волочильного штампа; C — жесткость пружины; d K – диаметр контейнера; dDL — диаметр гребенки матрицы; α — угол заплечика штампа; коэффициент глубокой вытяжки…
Контекст 2
… производство многокомпонентных компонентов представлено Napierala et al. [20]. Окончательный комбинированный процесс глубокой вытяжки и обратного формования [19] состоит из двух частей: холодного экструдированного внутреннего сердечника и внешней оболочки, которая состоит из глубокой вытяжки и перетянутой чашки. Основной технологический принцип этой комбинации процессов показан на рис. 7. На рис. 7 d B — диаметр заготовки; t B – толщина заготовки; d C – диаметр сердечника; r C – радиус края сердцевины; r DD – радиус волочильного штампа; C — жесткость пружины; d K – диаметр контейнера; dDL — диаметр гребенки матрицы; α — угол заплечика штампа; коэффициент глубокой вытяжки…
Контекст 3
… середина поверхности листа. Лист помещается между инструментом глубокой вытяжки и держателем заготовки. Усилие держателя заготовки можно регулировать с помощью пружин держателя заготовки. Процесс инициируется процессом глубокой вытяжки, при котором стержень, действующий как пуансон для глубокой вытяжки с заданным радиусом кромки, проталкивается пуансоном вниз, как показано на рис. 7б. За процессом глубокой вытяжки следует процесс соединения, инициируемый контактом перетянутой чашки и заплечика экструзионной головки, как показано на рис.7с, при этом лист снова подвергают глубокой вытяжке, а сердцевину подвергают холодной штамповке. Путем глубокой вытяжки перфорированного стального листа и последующего выдавливания стержня вперед даже произвольные участки вала могут …
Контекст 4
… пружины. Процесс инициируется процессом глубокой вытяжки, при котором стержень, действующий как пуансон для глубокой вытяжки с заданным радиусом кромки, проталкивается пуансоном вниз, как показано на рис. 7б. За процессом глубокой вытяжки следует процесс соединения, инициируемый контактом перетянутой чашки и заплечика экструзионной головки, как показано на рис.7с, при этом лист снова подвергают глубокой вытяжке, а сердцевину подвергают холодной штамповке. Путем глубокой вытяжки перфорированного стального листа и последующей экструзии стержня вперед даже произвольные участки вала могут быть покрыты материалом оболочки. Например, детали из стальной заготовки и цилиндрического алюминиевого сердечника могут удовлетворять высоким требованиям к поверхности …
Чертежи шаблонов для холодной штамповки.

Архитекторы и дизайнеры часто используют в своей работе кованые элементы.Элегантно и благородно смотрятся ажурные металлические решетки, закрывающие камины, или красивые балясины на лестнице.
Если вы умеете выполнять ковку и научитесь этому ремеслу, то сможете сами создавать оригинальные изделия.
Этот урок подходит для всех, кто любит заниматься физическим трудом и готов ознакомиться с технологией и особенностями выбора металла.
Что нужно знать о ковке?
Ковка — это процесс обработки специальной заготовки.Его цель – придать металлу необходимые размеры с формой. Различают горячую ковку и холодную.
Мастеру необходимо ознакомиться с обеими разновидностями, чтобы знать преимущества и недостатки каждой.
Метод горячей штамповки
При горячем способе металлическая заготовка сильно нагревается. В результате металл становится пластичным. Горячая ковка придает заготовке нужные размеры и нужную форму. Мастеру доступны различные варианты работы.
Нагрев металлической заготовки имеет и недостатки. В первую очередь необходимо оборудовать специальное помещение. Вам нужно будет купить кузнечный горн, для которого вам придется купить топливо.
Необходимо соблюдать правила пожарной безопасности, важно, чтобы мастер умел работать с огнем.
Имея представление о температурных режимах, применяемых в процессе ковки, вы без труда подберете нужный вид поковки.
Метод холодной ковки
Холодная ковка – трудоемкий процесс. Для того чтобы добиться той формы, которая требуется от металлической заготовки, ее изгибают, обжимают и сваривают. Техника выполнения немного проще по сравнению с горячим методом.
Мастерская не требует много места, а для ее обустройства не нужно будет приобретать специальный рожок, достаточно купить кузнечный станок.
Процесс изготовления изделия предполагает работу со сборными полуфабрикатами. Если была допущена ошибка, то исправить ее невозможно.
Выберите металл
Для ручной ковки подходят металлы с определенными свойствами. Чем пластичнее металл, тем легче изменить его форму. Однако пластичность неразрывно связана с прочностью.
Увеличение показателя одной характеристики неизбежно влечет за собой снижение другой. Покупая заготовку, мастер должен точно знать, каков ее состав.
Мастера изготавливают элементы декоративной ковки из меди, стали, дюралюминия или латуни.Кроме того, могут также использоваться сплавы. Информацию о легко поддающихся ковке металлах можно найти в Марочнике стали и сплавов.
Какие инструменты нужны для ковки?
Инвентарь варьируется в зависимости от метода ковки. Кузнечный горн с наковальней, молотки с клещами понадобятся для горячей ковки.
Для холодного метода понадобится инструмент Гнутик, позволяющий сгибать заготовку под углом, и станок Улитка для ковки, который можно сделать своими руками. Последний станок позволяет создавать декоративные элементы с формой в виде спирали.
Внимание!
Кроме основных инструментов для холодного метода также можно использовать «Фонарик», «Волна», «Твистер», станок для колец и другие.
Современный рынок предлагает промышленные машины, предназначенные для выполнения технологических операций. На фото ковки вы видите изделие, изготовленное на станке Мастер 2 от МАХ.
Ручная ковка
Для того, чтобы заготовка приобрела нужную форму, мастер должен применять в своей работе различные приемы и методы. Вам нужно будет приобрести различные инструменты и освоить различные технологии.
Метод холодной ковки не требует от мастера особых усилий. В работе выделяют следующие этапы:
- создание рисунка или зарисовка декоративного элемента;
- заготовка заготовок;
- процесс ковки.
Сегодня чертеж можно сделать с помощью компьютерной программы самостоятельно или заказать у профессионалов. Проект позволит перед началом работ рассчитать, сколько нужно закупить металлических заготовок.
Внимание!
Основные кованые элементы представлены следующими группами:
- Лапы. Концу металлического стержня придается определенная форма.
- Локоны. Концы стержня могут быть изогнуты в одном или двух направлениях.
- Кольца.Элементы декора изготавливаются из прутьев квадратного или круглого сечения.
- Торсион. Для него характерно винтовое закручивание вдоль оси.
Используются 3 общепринятые технологии: волочение, гибка и скручивание.
- Вытяжка позволяет увеличить длину металлической заготовки, уменьшив величину ее поперечного сечения.
- Гибка позволяет сгибать любую часть заготовки под углом.
- Скручивание — технология, при которой заготовку скручивают вдоль оси.Для скручивания используется машина Twister.
Все элементы собираются и фиксируются сваркой. Эти операции выполняются на специальной таблице. Самодельная холодная ковка не требует особых навыков.
Фото ковки своими руками
Внимание!
Люди давно заметили, что нагретому в горне металлу можно придать практически любую форму. Кованые изделия прекрасно смотрятся в любом интерьере.Они могут быть элементом декора как деревянного, так и каменного коттеджа.
Среди владельцев частных домов вряд ли найдется человек, который не хотел бы иметь кованый забор, перила или лестницу. Но, несмотря на множество достоинств, изделия, полученные с помощью горячей ковки — процесса, при котором металл становится пластичным под воздействием высокой температуры, доступны далеко не всем из-за высокой цены. Есть альтернатива – холодная ковка металла. Главное его преимущество – не только низкая цена, но и доступность техники для самостоятельного повторения.
Холодная ковка металла — процесс, при котором металл не подвергается нагреву, а форма изделию придается за счет его гибки, опрессовки и сварки из нескольких заготовок.
Некоторые специалисты считают название «холодная ковка» не совсем корректным. По их мнению, ковкой можно назвать только процесс пластической деформации горячего металла. Но название этого метода металлообработки прижилось. Более того, пользователи считают, что в некоторых случаях холодная ковка металла может стать достойной заменой горячей ковке.Так ли это на самом деле мы расскажем в сегодняшней статье.
Особенности холодной штамповки
Существует расхожее мнение, что изделия, полученные гибкой, получаются однообразными, больше похожими на заводскую штамповку, насаженную на резьбу. Однако практика показывает, что при должном подходе с помощью холодной ковки можно создавать настоящие авторские произведения.
Чаще всего методом холодной ковки делают:
- оконные решетки;
- элементов козырьков, поручней и козырьков для входной группы;
- декоративные элементы для ворот и ворот;
- фигурные ножки для столов и стульев;
- элементов декора: подставки для цветов, решетки для камина, обрамление картин, зеркала и т.
д.
Для художественной — горячей штамповки металла выпускаются изделия, полученные холодной деформацией на специальном оборудовании, впоследствии сваренные в одно целое: элементы забора, ограждения или калитки. Более того, непосвященный человек не сразу поймет, как было подделано это изделие.
Гоблин 2 пользователь FORUMHOUSE
На мой взгляд, кованые элементы, изготовленные методом холодной деформации (гибки), выглядят не хуже, чем такие же элементы, изготовленные вручную — горячей ковкой.И они дешевле.
Холмофф пользователь FORUMHOUSE
Холодная ковка металла позволяет с помощью достаточно простого набора оборудования создавать типовые элементы — торсионы, катаные пики, улитки, пространственные гибочные элементы. А затем, комбинируя этот набор (примерно из 10-15 видов типовых элементов) создавать сложные узорчатые изделия. Освоить процесс гибки может любой человек, владеющий слесарным инструментом, было бы желание.
Обычные геометрические фигуры в сочетании с завитками и волнами могут очень красиво смотреться в металле, ведь любой самый сложный рисунок состоит из множества простых элементов.
Существенным преимуществом холодной штамповки металла перед горячей ковкой является высокая производительность. Для работы не требуется много места. Нет необходимости снаряжать и разжигать рог, ковать, молотить на наковальне. Меняя только фурнитуру, можно быстро создавать самые разные элементы, но для соединения узлов потребуется хорошее владение сварочным делом.
Холмофф пользователь FORUMHOUSE
Я когда-то делал холодную ковку и научился варить полуавтомат за два дня.
Для получения хорошего результата процесс холодной штамповки металла следует разделить на ряд последовательных этапов:
- Идея и постановка задачи.
- Концептуальные зарисовки идей от руки на бумаге.
- Точный рисунок продукта от руки или в графической программе.
- Разбивка всего изделия на отдельные простых элементов .
- Начертить или распечатать на принтере единицы продукции в натуральную величину.
Некоторые принтеры поддерживают печать плакатов, то есть печатают части большого изображения на листах формата А4, потом их можно только склеить между собой.
- Расчет количества необходимого материала.
- Изготовление отдельных элементов.
- Шлифовка и сборка (сварка) отдельных элементов в единую конструкцию.
Несмотря на кажущуюся простоту, практика холодной ковки металла требует вдумчивого подхода и грамотного расчета всех деталей будущего изделия.Эксперты FORUMHOUSE советуют — для визуализации идеи предварительно изготовьте отдельные блоки из провода реального размера . Это поможет понять, как различные элементы будут сочетаться друг с другом и вовремя исправить ошибки, либо найти более удачное сочетание узоров и отдельных элементов.
К основным элементам, полученным методом холодной ковки металла, относятся:
- Лапы и пики. Эти элементы выкатываются из металлического прутка.
- Кудри.Включает в себя: улитку, червячка и улитку. У волюты, или, как ее еще называют бублики, концы загнуты в одну сторону. Маленький червяк выглядит как знак $. Улитка напоминает запятую.
- Кольца изготавливаются из стержня круглого или квадратного сечения, намотанного на специальную оправку. Получается своеобразная металлическая пружинка, которую потом разрезают на кольца.
- Торсион. Один из самых распространенных элементов. Получается скручиванием одного или нескольких стержней.
Все вышеперечисленные элементы можно выполнить, объединив всего три технологических процесса.
1. Капюшон. Благодаря этому процессу за счет уменьшения поперечного сечения заготовки увеличивается ее длина. Таким образом обычно получают лапы и пики, для чего металл помещают в специальный прокатный или обжимной станок. Пропуская заготовку через валки и постепенно уменьшая расстояние между ними, материал раскатывается. Также на валики могут быть нанесены рельефные насечки, придающие поверхности заготовки определенную фактуру.
2. Торсион. Металл (полосы или стержни) скручены вдоль своей оси. Можно скрутить одну, две, три и более заготовок. Для этого один конец заготовки (или заготовок) помещают в тиски, а другой начинают проворачивать по оси. Если скрутить несколько стержней, а затем сжать их, прикладывая усилие по оси, то они разойдутся по дуге. Получается утолщение из сплетенных прутьев под названием «Фонарик» или «Корзинка».
3. Гибка.Металл гнут на специальном станке по шаблонам.
Для гибки металла в разных плоскостях необходимо простейшее оборудование и простые станки. На рынке представлено множество станков для холодной ковки. Но из-за высокой цены их приобретение оправдано только в том случае, если планируется дальнейшая прибыль. У начинающего мастера, занимающегося холодной ковкой «для себя», вполне может получиться гнуть металл.
На первых порах можно обойтись простыми кондукторами и оправками, вставляемыми в обычные слесарные тиски.Можно сделать торсион, зажав конец заготовки в тисках, затем надеть на него трубу, и, используя хомут, закрутить заготовку вдоль ее оси.
Alexei62 пользователь FORUMHOUSE
Все инструменты для холодной ковки (кроме сварочного аппарата) можно изготовить из подручных средств.
Наиболее часто для холодной ковки металла применяют следующие инструменты:
- Гнут. С его помощью заготовка сгибается под определенным углом.
- Улитка.С его помощью заготовка сгибается по спирали. Меняя шаблоны, можно изменить радиус изгиба.
- Фонарик. Он напоминает токарный станок.
Этим инструментом металлические заготовки переплетаются друг с другом, чтобы получить одноименный элемент.
- Волна. Принцип работы этого инструмента понятен из названия. С его помощью металлу придается волнистая поверхность. Расстояние между «гребнями» волн и их высоту можно регулировать в зависимости от настроек машины.
- Твистер. Скручивает полосу или стержень вдоль продольной оси.
Принцип работы всех вышеперечисленных машин очень прост. Он основан на приложении через рычаги к заготовке определенного усилия, приводящего к деформации металла. Гибка металла на станках ручная. Для облегчения труда некоторые машины оснащаются электродвигателями, что удорожает их. Многие домашние умельцы предпочитают изготавливать станки для холодной ковки своими руками.Также с появлением опыта и увеличением сложности изделий необходимо комплектовать станки разнообразной фурнитурой — шаблонами, кондукторами, упорами, упорами.
Большой простор для творчества. Каждый мастер делает приспособления под свои задачи. Важно соблюдать принцип разумной достаточности. Самые красивые изделия можно сделать, используя минимум приспособлений.
Секреты холодной ковки
Один из главных вопросов начинающих мастеров: «Какой металл подходит для холодной ковки.По мнению форумчан, нужно не жалеть времени и обойти местные металлобазы, и ознакомиться со списком, который они предлагают. Для холодной ковки используется самый обычный «черный» металл. Ходовой размер для полос шириной 14 и 16 мм, толщиной 2-4 мм.Брусок — квадрат со стороной до 10 мм.Такой материал легче согнуть.Более толстый материал, полоса 20х4 мм и т.д. подрезать
Горячая ковка известна человеку с тех пор, как он начал обрабатывать и применять в своей жизни металлы.До изобретения штамповочных и металлорежущих станков горячая ковка и литье были единственными способами изготовления инструментов и оружия, домашней утвари и украшений.
Чтобы освоить традиционное кузнечное дело, нужно было долго учиться и набираться опыта. Изделия кузнеца получались очень трудоемкими и уникальными, это несомненное преимущество для искусства и столь же очевидный недостаток там, где требуется большое количество одинаковых изделий.
Недостатки горячей штамповки, такие как:
- высокая трудоемкость
- высокие требования к квалификации мастера,
- низкая повторяемость изделий.
Недостатков лишен метод холодной ковки. В его основе лежит свойство металлов изменять свою форму в определенных пределах под действием механической силы. Технология применима для круглого и квадратного проката, металлической полосы, труб и проката различного профиля. Несколько основных операций, таких как
- изгиб заготовки под заданным углом и заданным радиусом,
- формирование завитков и спиралей,
- скручивание одной или нескольких заготовок вдоль продольной оси
и сочетание полученных деталей позволяет создавать ажурные ограждения, беседки, скамейки, предметы декора и быта в разумные сроки и по доступной цене, в разы, а то и в десятки раз ниже, чем при использовании горячей ковки .
Кроме того, все элементы будут абсолютно одинаковыми по форме и размеру, что особенно важно при формировании из них узоров и орнаментов.
Для получения основных элементов используйте специальные станки.
- Гнутик — один из самых популярных. Он позволяет изгибать брусок под заданным углом и по заданному радиусу, в том числе в виде волны.
- Улитка предназначена для скручивания конца стержня или трубы в спираль
- Торсион предназначен для скручивания стержня вдоль его продольной оси.
Если вы планируете производить большие серии изделий, то вам понадобится станок для промышленного производства. Обладает высокими характеристиками, достаточным ресурсом, оснащен электроприводом достаточной мощности, сочетающим в себе гноут, улитку и торсион. Передовые производители оснащают свои агрегаты полуавтоматическими приставками, а роль работника сводится к установке необходимой оправки, закреплению заготовки и запуску программы.
Система сама контролирует скорость подачи, усилие прижима формующего ролика, начало и конец формовки.
Если для начала вы планируете просто ознакомиться с технологией холодной ковки, потрогать ее руками, то можно сделать устройство начального уровня самостоятельно, сэкономив значительные суммы, так как промышленные агрегаты приближаются к цене автомобиля.
Станок
Одна из простых конструкций самодельного гнутика состоит из следующих деталей:
- Массивное основание с пазом.
- Подвижный упор, перемещаемый по пазу червячной передачей
- Два неподвижных фиксатора упора, закрепленные на основании.
Приспособление «Гнутик»
Ролики на неподвижных упорах взаимозаменяемы для возможности гибки стержней и труб под разными углами и радиусами. На подвижном упоре также фиксируется съемный ролик или клин, в зависимости от желаемой формы изгиба.
Пока прямую заготовку зажимают неподвижными упорами и, вращая привод червячного механизма изгиба, подводят к ней подвижный упор — клин или ролик.
Продолжая вращать диск, согните заготовку на нужный угол.
Изготовить комар для холодной ковки своими руками вполне возможно, достаточно строго следовать чертежу, соблюдая размеры и припуски.
Трудности в домашней мастерской могут возникнуть при фрезеровании высокопрочной стали и при сверлении в ней отверстий.
Если такого оборудования в мастерской еще нет, то лучше оформить заказ на основные детали гайки в производстве — дрелью и лобзиком этого не сделать.
Соединение и покраска деталей
Для сборки деталей в желаемый дизайн необходимо предусмотреть ровное свободное пространство — на полу или на столе, в зависимости от размера. Заготовки лучше отшлифовать, чтобы удалить ржавчину, и очистить поверхность перед сваркой и покраской. Пескоструйный агрегат можно изготовить и самостоятельно из использованного газового баллона, пары насадок и кранов. Для насадки можно использовать керамический корпус бывшей в употреблении свечи зажигания.
Для этого достаточно владеть навыками сварки и слесарного дела.
После пескоструйной обработки детали раскладываются на месте сборки. Для удобства работы можно использовать бруски-вагонки. После того, как детали размещены, стоит еще раз проверить соответствие их расположения чертежу. Далее, зафиксировав струбцинами ключевые элементы конструкции, точечная сварка должна прихватить их друг к другу. В последний раз, когда вы проверили размеры, углы и взаимное расположение, можно переходить к сварке всех необходимых швов.
После сварки окалину необходимо очистить проволочными щетками, закрепленными в дрели, а в труднодоступных местах вручную.Дизайн готов к покраске. В зависимости от выбранных грунтовок и финишных покрытий, а также от способа нанесения сборка укладывается на амортизирующие брусья или монтируется вертикально с временными упорами.
Конструкции с большой плотностью деталей удобно красить из краскопульта, для редкой решетки для уменьшения потерь краски придется вооружиться кистью.
Изделия холодной ковки
Методом холодной ковки изготавливаются разнообразные изделия.Это, в первую очередь, элементы решеток и ограждений – как сами прутья, так и поперечины, навершия, украшения. С расстояния нескольких метров его сложно отличить от кованой решетки. Любую решетку оживят завитки и спирали, складывающиеся в замысловатые узоры и орнаменты. Таким образом, обычный забор, помимо своего утилитарного назначения, приобретает еще и художественную ценность. Для этого потребуется гайка, улитка и торсион.
Кованые подставки для фонарей, перила для мостиков через пруды, навесы и веранды, столики и скамейки прекрасно смотрятся на придомовой территории.А саму беседку неплохо сделать из кованого бруса. Неожиданную для сурового металла легкость и воздушность ему придадут завитки и спирали, а витые опоры подчеркнут стремление подняться.
Сегодня также широко распространены кованые мангалы-барбекю, которые также дополняют бытовое назначение эстетическим впечатлением.
Сама жаровня теряется среди навеса, узорчатых стен и опор, украшенных завитками крыши.
Детали балюстрад, перил лестниц и балконов также очень популярны.Здесь также широко используются завитки и спирали, причем не только как украшение, но и как конструктивный элемент. Очень уместно смотрится перекрученная по продольной оси балясина, а угловые опоры часто делают из нескольких скрученных между собой прутьев. Также на торсионе делают так называемый «фонарик» — несколько изогнутых спиралью стержней, соединенных концами при помощи сварки.
Следующая область применения холодной ковки – детали отделки помещений и мебели.Дверные ручки и защелки, каминный инвентарь и вешалки, стойки для зонтов и карнизы для штор и портьер – здесь широко используются мелкие завитки и витые перекладины.
Мебель изготавливается как садовая, не боящаяся осадков и смены времен года, так и домашняя, сочетающая металл с деревом и тканью.
Кованые изделия в архитектуре и интерьере давно пользуются большой популярностью. Решетки на окна и для каминов, ограждения или балясины лестниц, выкованные из металла, всегда смотрятся изысканно и привлекательно.Сегодня, несмотря на современные технологии обработки металла, изделия из металла ручной ковки популярны как никогда. Конечно, ковка металла своими руками – дело непростое, и без должной подготовки сложно сделать красивое кованое изделие. Но тем, кто хочет овладеть этим древним ремеслом и готов к тяжелому физическому труду, предстоит познакомиться с видами и технологией ковки металлов, разобраться в металлах для ковки, понять процесс ковки и уметь обращаться с кузнечным инструментом.
Поковка металлическая
Ковка металла — это процесс обработки металлической заготовки с целью придания ей определенной формы и размера. На самом деле существует два вида ковки – холодная и горячая. Выполняя ручную ковку металла, необходимо разбираться в обоих видах ковки, так как каждый имеет свои преимущества и недостатки.
При горячей ковке заготовку нагревают до определенной температуры, при которой металл теряет прочность и становится пластичным. Высокая пластичность является основным преимуществом горячей штамповки. Он позволяет легко придать металлической заготовке определенную форму и размер. Также горячая ковка позволяет использовать большинство технологий ковки, что благоприятно сказывается на многообразии вариантов работы.
Но есть у металлического отопления и недостатки. Прежде всего, это необходимость обустроить специальный кузнечный очаг и стоимость топлива для него. Это может стать настоящей проблемой для желающих заняться горячей ковкой металла своими руками в городских условиях.Кроме того, работа с огнем является достаточно опасным видом деятельности и требует повышенной пожарной безопасности. Еще одним фактором, который может существенно повлиять на выбор вида поковки, является специфическое знание температурных режимов поковки металла.
В отличие от горячей ковки, холодная ковка металла не требует оснащения очага для нагрева металла. Весь смысл холодной ковки заключается в формировании металлической заготовки путем гибки, опрессовки и сварки. Холодная ковка несколько проще в исполнении, а для оснащения мастерской не требуется много места.Весь процесс создания готового продукта не требует применения высоких температур, что очень положительно сказывается на общей безопасности.
Но у холодной ковки есть один существенный недостаток. Все работы приходится производить с определенными сборными полуфабрикатами без возможности исправить их ошибку. Конечно, это касается не всех работ по холодной ковке, но в большинстве случаев поврежденная заготовка годится разве что на металлолом или методичку.
В любом случае, вне зависимости от вида поковки, необходимо довольно внимательно ознакомиться с рядом важных моментов.Во-первых, это касается металлов и температурных режимов их плавки и ковки. Во-вторых, нужно знать и понимать технологию ковки металла. Ниже мы рассмотрим, какие технологические приемы используются для ковки и как они используются в работе.
Поковка металлическая
Ручная ковка металла — довольно трудоемкая и сложная работа, требующая использования определенных металлов, а точнее, металлов с определенными характеристиками. Для ручной холодной или горячей ковки важнейшей характеристикой является пластичность металла, ведь именно от нее зависит простота и удобство изменения формы заготовки.Но стоит отметить, что пластичность и прочность металла взаимосвязаны. При увеличении одной из этих характеристик вторая снижается. Поэтому так важно разбираться в характеристиках металла и знать о составе заготовки.
Важно! Есть и другие, не менее важные характеристики металлов. Но поскольку речь идет о ковке декоративных изделий, таких как решетки каминов, балясины, заборы и т. д., то нет необходимости ориентироваться на износостойкость, красностойкость и так далее, а также на легирующие элементы.
Для декоративной ковки используются следующие металлы: медь, латунь, дюраль, сталь, а также другие медные, магниевые, алюминиевые и никелевые сплавы. На самом деле для ручной ковки используют мягкий ковкий металл, которому легко можно гнуть или придавать определенную форму. Для того, чтобы выбрать самый легкий пластичный металл, нужно заглянуть в Марочник Стали и Сплавы. В нем можно найти подробное описание всех металлов и сплавов с их характеристиками и составом.
Несмотря на то, что самым ковким металлом является медь и ее сплавы, мастера предпочитают использовать черные металлы для холодной и горячей ковки. Такое положение обусловлено высокой стоимостью цветных металлов. Ведь на поковку из металла цена больше зависит от стоимости исходной заготовки, и не каждый может позволить себе приобрести забор или балясины из меди. При выборе мягкого черного металла для ковки необходимо ориентироваться на сталь с минимальным содержанием углерода около 0.25%. А также с минимальным количеством вредных примесей, таких как хром, молибден, сера и фосфор. Кроме того, следует избегать конструкционных и инструментальных сталей с высоким содержанием углерода от 0,2% до 1,35%. Такие стали наименее пластичны и плохо поддаются сварке.
При выборе того или иного металла необходимо использовать Марочник Стали и Сплавов. Но если доступа к нему нет, то для определения содержания углерода в стали можно воспользоваться приведенными ниже таблицами. Сам процесс определения достаточно прост, достаточно поднести заготовку к работающему точилу и посмотреть на сноп искр, а затем сравнить его с показателями в таблице.
Сегодня, благодаря промышленному производству металла, уже нет необходимости создавать заготовки своими руками. Современные кузницы используют готовые заводские изделия для холодной ковки. Наиболее часто используемые размеры заготовок следующие: 30х45 мм, 40х45 мм, 10х10 мм, 12х12 мм, стержни сечением 10 мм, 12 мм, 16 мм, 25 мм, 30 мм, 50 мм, листовой металл с толщиной от 3,5 до 6 мм, трубы круглые 1/2″, 3/4″, 1″, профильные трубы от 20х20 мм до 30х30 мм.
Инструмент для ковки металла
Любые работы по ковке металла невозможны без специального инструмента.Кузнечное оборудование для горячей ковки достаточно разнообразно и включает в себя наковальню, горн, различные молоты, клещи и прочее. Инструмент для холодной ковки несколько проще и состоит из нескольких специальных станков. Безусловно, современный инструмент, такой как сварочный аппарат, болгарка и болгарка, используется как при холодной, так и при горячей ковке. Зная назначение инструмента, можно правильно выполнить любую работу.
Инструмент для горячей штамповки
- Звуковой сигнал . Без него не обходится горячая ковка. Ведь именно в ней заготовку можно нагреть до температуры 1400°С.По большей части печь представляет собой печь, рассчитанную на высокие температуры и с дутьем.
- Наковальня . Этот инструмент является опорой, на которой выполняется ковка. Сама наковальня имеет несколько видов, среди которых наиболее популярна двурогая наковальня весом 200 кг. А вот вес может колебаться от 150 до 350 кг.
- Шпера . При выполнении различной художественно-декоративной ковки используют шпере. Они имеют множество различных видов, и каждый мастер может сделать их для себя.
Общим признаком всех шпереков является то, что они вставляются в квадратное отверстие наковальни или закрепляются в деревянном полене. На фото ниже представлены самые распространенные шперсы.
- Кувалда и Ручной тормоз . Это основной инструмент кузнеца. Кувалда весит от 4 до 8 кг и используется для нанесения тяжелых ударов. В зависимости от вида работ и толщины заготовки подбирается и вес кувалды. Ручник весит от 0.от 5 до 2 кг. Используется для доработки продукта.
- Клещи . Клещи Горна – второй по важности инструмент. Без них невозможно удержать горячую заготовку для обработки. Существует несколько видов клещей-клещей для определенного профиля и размера заготовки. На фото ниже представлены клещи различной формы.
- Фасонные молотки . При выполнении художественной ковки требуется создание криволинейных заготовок или заготовок определенной формы.Для этого используются фигурные молотки.
Они могут быть как нижними, на которых производится обработка, так и верхними. Вариантов фигурных молотков много и у каждого мастера он свой. На фото ниже показан основной вспомогательный инструмент.
Помимо описанных выше, используются различные измерительные инструменты, такие как обычная рулетка , двойной штангенциркуль , кузнечный уголок , шаблоны и калибры . Выбор кузнечного инструмента огромен, все перечислить сложно, поэтому у каждого мастера свой набор только необходимых и часто используемых инструментов.
Инструмент для холодной штамповки
- Гнутик (фото ниже). Это основной инструмент для холодной ковки. Как следует из названия, он позволяет сгибать металлическую заготовку под определенным углом. Кроме того, гайка позволяет создавать дуговые элементы определенного радиуса.
- Улитка . Имя говорит само за себя. С помощью улитки можно создавать различные декоративные элементы спиралевидной формы.
Спираль делается по определенному шаблону, который при необходимости можно поменять на другой, с меньшим или большим радиусом.
- Фонарик . Эта машина предназначена для создания одноименного декоративного элемента.
- Волна . Позволяет создавать волнообразные элементы. При протягивании стержня через этот станок на выходе получается красивая синусоидальная заготовка.
- Твистер . По принципу работы этот станок похож на Фонарик, но в отличие от него твистер только закручивает заготовку по оси.
- Кольцевая машина . Как и во всех предыдущих машинах, название говорит само за себя.
Помимо вышеперечисленных есть еще универсальные станки для клепки, резки, опрессовки и придания объема. Все описанные выше станки можно сделать как самостоятельно, так и приобрести в магазине. Конечно, самодельные приспособления для холодной ковки будут несколько уступать по качеству заводским, но это компенсируется уникальностью созданных с их помощью элементов. Для изготовления станков холодной ковки чертежи можно найти как в свободном доступе, так и купить у специалистов.
Важно! Станки для холодной ковки могут быть ручными или оснащены электродвигателями. Несмотря на наличие зубчатых передач, ручная холодная ковка – занятие довольно трудоемкое и длительное, и для получения больших объемов кованых элементов станок лучше оснастить электродвигателем.
Отдельно стоит упомянуть промышленные станки для холодной ковки.На аналогичные станки холодной ковки цены составляют около 6000 у.е., но один такой станок может выполнять практически все технологические операции холодной ковки. Примером может служить машина Master 2 компании MAN. На видео, демонстрирующем холодную ковку, можно увидеть возможности этого станка.
Ковка из металла своими руками
В процессе ковки используются различные приемы и приемы ковки для придания заготовке определенной формы. Для выполнения каждого из них используется определенная технология и инструмент для ковки металла. Технология ковки металла горячим и холодным способами существенно отличается. Как уже отмечалось, горячая ковка требует нагрева заготовки для изменения ее формы, а при холодной ковке заготовка только гнется. Исходя из этого выделяют основные технологические приемы, зная которые можно смело браться за ковку металла своими руками.
Ковка из металла своими руками
Холодная ковка своими руками выполняется достаточно легко и особых усилий не требуется. Все работы разбиты на несколько этапов: создание эскиза или чертежа будущего изделия, закупка материалов и сам процесс ковки металла.
Рисунок можно создать в специальной компьютерной программе, приобрести готовый или нарисовать от руки. Вы можете найти чертежи для холодной ковки. Для этого достаточно обратиться к мастерам, которые занимаются ковкой уже несколько лет, и попросить один-два чертежа для обучения. На самом деле рисунок преследует несколько целей. Во-первых, для того, чтобы знать, какие элементы нужно будет изготовить методом холодной ковки. Во-вторых, имея на руках такой проект, можно рассчитать количество и тип металлических заготовок, таких как стержни, профильные трубы и так далее.В-третьих, потребуется чертеж, чтобы собрать все элементы в единое целое.
Отдельно необходимо рассмотреть элементы холодной ковки, из которых состоит проект. Сегодня можно найти довольно много различных кованых элементов, но все они могут быть объединены в несколько классических групп.
- Лапы . Этот элемент представляет собой раскатанный в какой-либо форме конец металлического стержня. В эту группу входят так называемые Пики. Несмотря на заостренный конец, козырьки выполнены по похожей технологии.
- Кудри . В эту группу входит несколько общих элементов: завитки, сердечки и улитки. Улитка или Бублик представляет собой стержень, концы которого загнуты в одну сторону. Червячок — стержень, концы которого загнуты в разные стороны. Этот элемент иногда называют «долларом» из-за его сходства со знаком американской валюты.
Запятая или Улитка — простой завиток, один конец которого загнут, а второй прямой.
- Кольца . Этот элемент создается достаточно просто: на заготовку станка накручивается стержень круглого или квадратного сечения, в результате получается пружина, которую затем разрезают на отдельные кольца.
- Торсион . Этот элемент довольно легко узнать по закручиванию винта вдоль оси. Вариантов торсионов очень много и одним из самых распространенных является такой элемент, как Фонарик, а также простой винтообразный стержень для решетки или забора.
Весь процесс изготовления элементов холодной ковки основан на следующих общепринятых технологиях ковки — гибка, скручивание, волочение.
Вытяжка — Это технология, заключающаяся в увеличении длины заготовки за счет уменьшения ее поперечного сечения. При холодной ковке используется один из вариантов волочения – прокатка. Именно с его помощью создаются различные лапы и пики. Для создания лапок используется специальный станок для раскатки.Вводят конец заготовки и затем запускается механизм прокатки, в результате торец сплющивается с рельефом или без него. Для изготовления козырька используют пресс-машину. Процедура та же, но в результате конец раскатывается и прессуется в определенной форме.
Гибка . Эта технология ковки заключается в загибании торцов или другой части заготовки под определенным углом. Сама гибка производится практически на всех станках холодной ковки.Процесс гибки можно проследить при изготовлении заготовки на станке Улитка. Сначала конец заготовки помещается внутрь специального шаблона, а затем загибается под определенным углом. Эти работы выполняются на станке Улитка.
Скручивание . Данная технология ковки предполагает скручивание заготовки вдоль ее оси. При холодной ковке этот процесс можно наблюдать при использовании станка Twister, на котором создаются различные кручения. Для этого один конец заготовки помещают в тиски, а второй конец вращают по оси. Отдельно стоит выделить элемент Фонарик. Для него используют два или более стержня, которые сначала закручивают по оси, а затем сжимают по оси, в результате чего стержни в определенном месте расходятся в стороны.
Сборка всех элементов в единую конструкцию выполняется сваркой на специальном сборочном столе. Сегодня сварочный аппарат общедоступен и является незаменимым инструментом современных кузнецов. Самодельная холодная ковка достаточно распространена среди начинающих мастеров и частных предпринимателей.Он не требует специальных знаний, навыков и большого помещения для работы.
Холодная ковка своими руками: видеоурок
Ковка из металла своими руками
По сравнению с холодной, ручная горячая ковка намного сложнее и требует от мастера опыта обращения с инструментом и хорошей физической подготовки. Работа ведется в несколько этапов: создание эскиза или чертежа, закупка материалов и ковка.
На самом деле разница между горячей и холодной ковкой заключается в технологических процессах обработки металла. Во-первых, это касается способа обработки. Во-вторых, для горячей ковки можно использовать практически любую металлическую заготовку. Но для удобства принято использовать готовые прутья квадратного и круглого сечения. В-третьих, в художественной горячей ковке нет каркасов для элементов готового изделия. Конечно, можно придерживаться создания классических элементов ковки – завитков, лапок, пики и прочего, но горячая ковка позволяет использовать весь потенциал фантазии мастера, открывающий безграничные возможности.Все изделия горячей штамповки создаются с применением следующих технологий обработки металла: осадка, волочение, гибка, скручивание, резка, насечка, чеканка.
Чертеж используется для поковки металла для увеличения поперечного сечения всей заготовки или ее части. При ковке в зависимости от необходимости осуществляют полный или местный нагрев заготовки для осадки.
Вытяжка заключается в увеличении длины заготовки за счет уменьшения ее поперечного сечения. Это можно сделать как ударами кувалдой или ручным тормозом, так и прокаткой металла между валами на станке. В отличие от холодной ковки, создание козырька с помощью вытяжки требует точных и аккуратных штрихов.
Гибка . Эта операция выполняется для придания заготовке криволинейной формы. Следует иметь в виду, что изгибание толстых заготовок может привести к их деформации, и для придания первоначальной формы необходимо выполнить черновую. Для гибки заготовок применяют различные шпереки, наковальни, фасонные молотки и кондукторы.
Скручивание . Данная технология ковки предполагает скручивание заготовки вдоль ее оси. Как и при холодной ковке, заготовка зажимается в тисках и проворачивается. Но в отличие от холодной ковки, вы можете локально нагревать заготовку, что позволяет легко делать локальную скрутку.
Технологии ковки, такие как резка , насечка и рельефная набивка , используемые в художественной ковке с применением долот. Края горячих заготовок в зависимости от проекта рассекают и закручивают клещами.Также, пока заготовка горячая, на ее поверхности печатается различный рисунок.
При горячей штамповке металла важно знать температурный режим нагрева. Это поможет лучше обрабатывать металл. Ковка черного металла производится при температуре 800 — 1250°С. Конечно, измерить горячую заготовку термометром будет невозможно и для определения температуры придется ориентироваться по ее цвету. В таблице ниже приведены температура и цвет заготовки из черного металла.
Горячая ковка металла: видеоурок
Ковка металла своими руками – достаточно увлекательное занятие, требующее постоянного совершенствования. Это касается в первую очередь создания различных художественно-декоративных элементов. Тем, кто только начал заниматься ковкой, придется потрудиться, чтобы их работа имела идеальную форму и высокое качество.
Любой мастер, оборудуя домашнюю кузницу, приобретает минимальный набор инструментов и принадлежностей. Но, как правило, самые простые технологические операции с металлическими заготовками делают только на первом этапе.
С приобретением опыта работы с «железом» появляется и желание, и необходимость заниматься художественной ковкой – это и украшение жилища, и дополнительный заработок. К сожалению, станка для придания образцам спиралевидной формы — улитки — в продаже почти не бывает. Так или иначе, но домашние умельцы, как правило, изготавливают его своими руками. Особенности самостоятельного изготовления и сборки мотков для холодной ковки – тема данной статьи.
Особенности улитки
Автор специально решил обратить внимание читателя на ряд моментов.Это поможет избежать некоторых ошибок в будущем. Например, разобравшись с устройством улитки и принципом ее функционирования, кто-то захочет собрать свое устройство, отличное от тех, чертежи которых будут представлены ниже.
Такое приспособление вполне (если речь идет о самодельном оборудовании) позволит гнуть образцы сечением (стороной квадрата) не более 10 — 12 мм. Имеется в виду модель улитки с «ручным управлением». С более размерными образцами в быту практически никто не имеет дело.Машину можно усовершенствовать, установив привод и электродвигатель.
Но насколько это рационально для небольшой домашней кузницы?
- Холодная штамповка осуществляется на малых скоростях. Резкое изменение геометрии металла приводит к появлению трещин (надрывов).
- Вам предстоит подобрать не только мощность электродвигателя, но и передаточное число редуктора. Плюс смонтировать схему автоматики с установкой соответствующих элементов (кнопки, пускатель и так далее).Все это сильно усложняет изготовление машины.
Вывод — для домашней кузни достаточно улитки, с помощью которой можно гнуть металлические изделия вручную. Любой, кто будет разбираться во всех нюансах его конструкции и хоть что-то понимать в электротехнике, сможет самостоятельно установить на него электропривод.
Изготовление улиток
Показаны несколько устройств. Примерно так (в основе) и должно получиться.
Сборка улитки своими руками – это один из вариантов самостоятельного проектирования, когда нет смысла давать рекомендации с указанием точных параметров всех комплектующих.Здесь нужно ориентироваться на собственное представление о том, что и как будет гнуться (радиусы, количество витков спирали и так далее). Но если станет понятна суть процесса изготовления, то и сама сборка не вызовет затруднений.
Настольное устройство
Процесс холодной ковки требует больших усилий. Если у вас уже есть готовый верстак, то, возможно, вам придется его укрепить. При изготовлении улитки с нуля каркас стола делается только из металла – швеллера, уголка, толстостенной трубы.
Понятно, что столешница тоже должна быть металлической. В процессе работы улитка будет подвергаться как статическим, так и динамическим нагрузкам. Поэтому обычный лист железа не подходит. Только пластинчатые, и не менее 4 мм.
Маркировка и установка «навесного» оборудования
Пожалуй, самый творческий этап работы. Все можно сделать своими руками. Но как, учитывая перспективы или ограничиваясь производством подобных образцов?
Вариант 1.Самый легкий. Смысл операции в том, что на столешнице рисуется спиральный контур.
По сути, это эскиз будущих фигурных деталей, например, из бруска. После этого достаточно вырезать несколько отрезков из толстого полосового железа, согнутого по радиусу. Они приварены к столешнице, и механизм для сгибания в основном готов.
Кому-то такое исполнение покажется более привлекательным — со сплошной полосой.
Но практика показывает, что работать с такой улиткой сложнее.Например, при снятии с него готового изделия возникнут определенные трудности.
Вариант 2. То же, но рисуется несколько контуров. Вдоль каждого просверливаются отверстия, в которых нарезается резьба. Осталось только подготовить шаблоны стоп-сегментов. Своими руками их делают, как правило, из плотного картона или фанеры.
изготавливают колодки, в которых после очередной разметки также сверлят отверстия, соответствующие посадочным «гнездам» в пластине.Такая конструкция позволит организовать производство спиральных заготовок с разным радиусом на одном столе. Вам останется только, в зависимости от формы изгиба, установить в определенных местах соответствующие сегменты. Крепление их к основанию болтовое. Вы можете поступить иначе. Вместо таких упоров поставьте цилиндрические.
Для фиксации притягиваются болтами (снизу плиты) или делаются сразу ножками (+резьба) и вкручиваются в столешницу. С ними гораздо удобнее.А если есть своя, то сделай сам — за пару часов.
Вариант 3. Подготовьте несколько съемных модулей, которые следует менять по мере необходимости.
Улитка в сборе
Установлен лемех, прикреплены рычаги, боковой упор. Все это хорошо видно на рисунках.
В дело пойдет все, что есть в сарае (гараже, на чердаке) — отрезки труб, прутья, уголки и тому подобное. Если принцип работы улитки понятен, то никаких подсказок уже не нужно.
Медицинский осмотр
Это всегда подразумевается, поэтому без комментариев.
В принципе сделать улитку для холодной ковки не так уж и сложно. Более того, единого стандарта для таких устройств не существует. Кто-то скажет — не проще ли купить заводскую модель? Во-первых, как уже было сказано, искать придется долго. Во-вторых, не факт, что его возможности совпадают с фантазиями мастера. В-третьих, необходимо будет облегчить кошелек примерно на 19 000 (механическая) и 62 000 (электрическая модель) рублей, как минимум.
Удачи в изготовлении улитки своими руками!
Влияние моделирования на конструкции холодной штамповки | 2017-08-03 | Кузнечный журнал
Прогностическая ценность моделирования процессов и изделий с помощью моделирования методом конечных элементов помогла в холодной штамповке крепежных изделий. При этом пуансон, применяемый в поковке колесного болта, был пересмотрен и переработан для исключения «застревания» пуансона в полом сечении поковки.
Возможности конечно-элементного моделирования в нашей отрасли возросли за последнее десятилетие из-за их высокой прогностической способности во всех прикладных дисциплинах, особенно в операциях обработки металлов давлением.Моделирование обработки металлов давлением используется для разработки уникальных методов обработки, исключая большое количество лабораторных испытаний, необходимых в таких исследованиях, но они также широко используются для прогнозного обнаружения возможных отказов материала, определения усилия ковки, правильной конструкции штампа и оптимизации топологии в индустрия.
Хотя моделирование влияет на затраты, оно также облегчает работу людей на производстве. Например, увеличение срока службы штампов по результатам численного моделирования в офисе приводит к уменьшению количества операций по смене штампов, выполняемых рабочими.
По сравнению с горячей ковкой течение материала при холодной ковке менее текучее. Следовательно, проектирование штампа требует большого опыта и способности прогнозировать возможные проблемы с помощью моделирования методом конечных элементов на этапе проектирования. В этой статье показано, что, несмотря на все усилия, могут возникать непредсказуемые сбои процесса, даже если полная разработка процесса была связана с моделированием методом конечных элементов. Поразительно, однако, что причины этих неудач снова были решены с помощью моделирования, показывающего влияние инженерного программного обеспечения на кузнечную промышленность.
Неожиданная проблема при ковке колесных болтовПроцесс холодной штамповки имеет важное значение в производстве болтов из-за сильной пластической деформации, придаваемой заготовке прессами, что значительно упрочняет материал без потери материала в виде стружки. Однако материал заготовки находится при комнатной температуре, а кованый материал может находиться на критической линии прочности на излом во время деформации. Хотя во всех учебниках упоминаются такие проблемы с ковкой материалов, отказы также можно рассматривать как часть всей системы штампов.Пример тому — тема данной статьи.
При производстве колесных болтов М12х1,5х12 на четвертом этапе ковки был обнаружен отказ пуансона, что заставило нас увеличить количество пуансонов, необходимых для выполнения указанного крепежа. Шестигранная форма головки болта изготавливается на третьем этапе, а окончательный размер шестигранника и полого сечения головки формируются одновременно на четвертом этапе ковки (рис. 1). Здесь было видно, что пуансон застрял в сформированном полом участке, вероятно, во время извлечения пуансона в последовательности ковки, и он сломался (рис. 2).
Система кузнечных штампов включает стационарные и подвижные штампы. Система подвижного штампа включает в себя пружину штампа, которая позволяет деформировать шестигранную головку болта и перемещать пуансон через полуболт. В конце деформации шестигранная матрица и пуансон движутся одновременно в противоположных направлениях, чтобы вырваться. Здесь очень важно понимать поток материала во время процесса. Многие пакеты программного обеспечения для моделирования обработки металлов давлением включают в свои библиотеки пружины ковочных штампов, но точное моделирование движения пружины невозможно.Однако сложные движения штампа можно смоделировать проще, задав определенные движения штампа как функцию времени.
Конечно-элементное моделирование: быстрое открытиеБыло подготовлено конечно-элементное моделирование этого четырехэтапного процесса ковки. Сначала операции формообразования и вытягивания на четвертом этапе ковки моделировались без пуансона для определения величины уменьшения диаметра отверстия (рис. 3).
Шестигранная матрица состоит из деформирующей и релаксационной частей.В то время как деформирующая часть выковывает материал, стенка матрицы была наклонена, чтобы уменьшить трение между текущим материалом и матрицей в релаксационной части. Это позволило материалу течь легче. Было видно, что деформирующая часть выталкивала материал при вытаскивании, однако это приводило к уменьшению диаметра отверстия болта на поковке колесного болта. В результате указанный диаметр отверстия от 11,01 до 11,05 мм был уменьшен примерно до 10,62 мм. Это привело к значительному увеличению контактного давления между пуансоном и материалом.
После критической точки пуансон становится неспособным двигаться в полости из-за повышенного давления и ломается в результате высокого напряжения растяжения. Чтобы устранить это, геометрия пуансона была изменена из-за заданного уменьшения диаметра отверстия, как показано на рисунке 4. Поэтому было предсказано, что контактное давление между материалом и пуансоном уменьшилось.
Подтверждение решенияМоделирование методом конечных элементов дает разработчикам поковок возможность проверить свои решения без проведения проб и ошибок в цеху.Чтобы доказать предлагаемое решение, новый пуансон может быть разработан в программном обеспечении САПР и легко адаптирован к моделированию. Как упоминалось ранее, геометрия пуансона была изменена из-за проведенного нами моделирования ковки.
Лучший способ сделать правильный вывод — повторить моделирование с измененными конструкциями и сравнить важные механические переменные (например, силы ковки и возникающие напряжения) с предыдущими результатами. Эта методология была выполнена, и усилия ковки текущей и пересмотренной конструкций сравнивались, как показано на рисунках 5a и 5b.Можно предположить, что заклинивание пуансона в отверстии полуболта обусловлено силами ковки в направлении осей х и у. Как видно на рисунках 5a и 5b, хотя ревизия не изменила историю усилий во время формирования болта, силы, действующие на пуансон, были уменьшены во время вытягивания. Это свидетельствует о том, что модифицированный пуансон не будет испытывать высоких нагрузок на отрыв, что приводит к пластической деформации и разрушению.
Благодаря передовому программному обеспечению для моделирования можно легко проводить анализ напряжения на определенном компоненте штамповой системы.Как мы знаем, моделирование формовки с помощью эластичных штампов требует больших вычислительных мощностей и длительного процессорного времени. Однако в промышленности время является критической переменной и не может быть потрачено впустую.
В программном обеспечении для моделирования пользователям не нужно запускать трехмерное моделирование с эластичными штампами для определения распределения напряжений на штампах и пуансонах. Специальные модули нагрузки штампа позволяют пользователям применять силы ковки, рассчитанные на основе предыдущих симуляций, проведенных с жесткими штампами, и применять эти нагрузки к эластичным штампам.Таким образом, процессорное время значительно сокращается.
С помощью этого модуля были определены максимальное и минимальное основные распределения напряжений на обновленном пуансоне, которые были сопоставлены с текущей конструкцией, как показано на рисунках 6a и 6b. Значения напряжения собирались по пути по окружности поверхности пуансона. Эти распределения очень важны для определения усталостной долговечности пуансона. Видно, что оба напряжения значительно уменьшились при разработке нового пуансона.
ЗаключениеВажность и эффективность конечно-элементного моделирования, используемого в приложениях холодной ковки, были проиллюстрированы в этой статье путем представления уникальной проблемы, которая возникла во время ковки колесных болтов. Небольшое время, затраченное на подготовку и запуск моделирования, устранило большие трудозатраты и затраты на проектирование, потерю времени на неработающих ковочных прессах, потребляемую энергию и затраты на испытания. На основании полученных численных результатов были изготовлены новые пуансоны и проведены испытания штамповки, которые показали, что результаты моделирования соответствуют фактическому применению.Колесный болт был успешно выкован в холодном состоянии за один день численной работы. Кроме того, срок службы пуансона был увеличен в четыре раза по сравнению с предыдущей конструкцией.
Ведущий автор Д-р Дженк Кылычаслан является специалистом по исследованиям и разработкам компании Norm Fasteners Co., крупнейшего производителя крепежа в Турции. С ним можно связаться по телефону +90 232 376 76 10 или по электронной почте [email protected]
Виды ковки. Что такое горячая ковка и холодная ковка?
В нашем руководстве по основам ковки я объяснил, что такое ковка и как работает основной процесс ковки.В этой статье вы ознакомитесь с классификацией поковок, холодной и горячей ковки и различных типов поковок.
Как известно, ковка имеет широкое применение в различных отраслях машиностроения. Если вы едете на велосипеде, мотоцикле, автомобиле, путешествуете в общественном транспорте или самолете, сидите дома или в офисе, в нем найдется один или несколько предметов, сделанных из ковки.
Классификация процессов ковки
В зависимости от прикладываемых усилий сжатия и деформации металла процесс ковки можно разделить на два типа:
- Схема процесса ковки.
- Процесс ковки с осадкой.
Процесс ковки
В этом процессе ковки поперечное сечение заготовки уменьшается с одновременным увеличением длины. Сила сжатия прикладывается перпендикулярно направлению удлинения или течения металла.
Процесс ковки с осадкой
В этом процессе ковки при приложении сжимающей силы происходит увеличение поперечного сечения заготовки за счет высоты.Сила сжатия прикладывается по высоте заготовки.
Процесс ковки может представлять собой процесс вытягивания, процесс осадки или их комбинацию.
Процессы ковки далее классифицируются как:
- Ковка в открытых штампах или кузнечная ковка.
- Ковка в закрытых штампах
Горячая штамповка против холодной штамповки
В чем разница между процессами горячей и холодной штамповки?
Процесс горячей штамповки
Вы можете осуществлять процесс горячей штамповки, нагревая металл заготовки до температуры рекристаллизации.Когда металл горячий, у вас есть преимущество в его повышенной пластичности, и вы можете выковать металл в желаемую форму с меньшим усилием. Горячекованые детали не подвергаются наклепу, однако поверхность имеет окалину и качество отделки оставляет желать лучшего.
Благодаря температуре рекристаллизации и приложенной силе сжатия атомы металла достигают своего уровня высокой энергии и инициируют образование более мелких кристаллов. Это процесс рекристаллизации, и новообразованные кристаллы не имеют деформации или наклепа.
Горячая штамповка может производиться в одну или несколько стадий.
Процесс холодной штамповки
Процесс холодной ковки можно проводить при комнатной температуре. При холодной штамповке получаются поковки с тонкой обработкой поверхности и формой, близкой к чистой. Однако холоднокованые детали подвергаются деформационному упрочнению, и во многих случаях требуется немедленный отжиг. Кроме того, процесс холодной ковки требует более высокой силы сжатия по сравнению с процессом горячей ковки.
Холодная штамповка производится в один или несколько этапов.
Однако во многих случаях операция ковки выполняется путем нагрева металла заготовки до температуры ниже температуры рекристаллизации, и это называется теплой ковкой (некоторые люди включают это также в холодную ковку).
Холодной ковкой могут подвергаться следующие металлы: медь, золото, серебро, латунь, платина, чистый титан и некоторые низкоуглеродистые стали.
В следующей сравнительной таблице подробно объясняются различные аспекты горячей и холодной штамповки.
ГОРЯЧАЯ КОВКА | ХОЛОДНАЯ КОВКА |
Потребность в отоплении | |
Металл заготовки нагревают до температуры рекристаллизации. | Обычно делается при комнатной температуре. Однако в некоторых случаях металл заготовки может нагреваться ниже температуры рекристаллизации. |
Сила сжатия, необходимая для ковки | |
Меньше по сравнению с холодной ковкой. | Высокая по сравнению с горячей ковкой. Кроме того, кузнечный молот или пресс должны быть более прочными. |
Отделка поверхности и контроль размеров | |
Поверхность покрыта чешуей, поверхность плохо обработана.Контроль размеров уступает холодной штамповке. | Чистота поверхности хорошая, без окалины. Размерный контроль хороший, и некоторые кованые детали имеют сетчатую или почти сетчатую форму. |
Деформационное упрочнение | |
Без деформационного упрочнения. | Холоднокованые детали подвергаются деформационному упрочнению и могут нуждаться в термической обработке. |
Состояние заготовки перед ковкой | |
Не большая проблема. | Металл заготовки должен быть чистым и иметь хорошее качество поверхности. |
Зернистая структура после ковки | |
Происходит рекристаллизация, и крупные зерна металла заготовки рекристаллизуются в более мелкозернистую структуру. | Холодная штамповка вызывает необратимую деформацию металла, что приводит к дислокации зерен и деформационному упрочнению. Рекристаллизация зернистой структуры происходит при отжиге кованой детали. |
Остаточное напряжение в кованой детали. | |
Ноль или маргинальный. | Остаточное напряжение существует. |
Обработка | |
Необходима особая осторожность, так как заготовка горячая. | Безопасен в обращении, так как заготовка холодная. |
Срок службы штампов | |
Меньше по сравнению с холодной ковкой. | Больше по сравнению с горячей ковкой. |
Экологичность | |
№ | Да |
Производительность | |
Низкий по сравнению с холодной ковкой, так как используется нагрев. | Высокая по сравнению с горячей ковкой из-за отсутствия нагрева. |
Сложность форм | |
Небольшие сложные формы могут быть выкованы, так как горячий металл пластичен и может течь в сложную полость под давлением. | Можно выковать только простые формы. Металл начинает упрочняться и становится менее пластичным. Следовательно, не может течь в замысловатые полости. |
Открытая штамповка или кузнечная ковка
Кузнечно-штамповочная ковка — это процесс ковки в открытых штампах. При нагреве металла заготовки и ковке многократными ударами молота металл в пластическом состоянии деформируется и течет. Течение и деформация могут быть ограничены с помощью штампа с полостью или с помощью плоского штампа.При использовании штампа с полостью металл в пластическом состоянии принимает форму полости штампа.
Когда штамп плоский (без полости), кузнец/рабочий манипулирует горячим металлом и придает ему желаемую форму с помощью повторяющихся ударов молота, и, поскольку используется плоский штамп, этот процесс известен как ковка в открытых штампах. Название «открытая матрица» указывает на то, что в матрице нет полости, ограничивающей пластическое течение металла.
Когда ковка в открытых штампах выполняется вручную с использованием наковальни и ручного молота, это называется ручной ковкой, а когда это делается с помощью молота, это называется силовой ковкой.В обоих случаях кузнец манипулирует заготовкой вручную.
1. Ручная ковка
Предположим, что заготовка представляет собой плоский металл шириной 3 дюйма, длиной 18 дюймов и толщиной 1/2 дюйма, и кузнец хочет выковать меч. Кузнец нагревает металлическую заготовку и кладет ее на наковальню, многократно молотит и манипулирует заготовкой в пластическом состоянии, чтобы получить желаемую форму. Точность готовой поковки зависит от мастерства оператора.
Процесс ручной ковки
Чтобы сделать меч, необходимо увеличить длину металла, и кузнец сделает это, многократно забивая грань плоскости по ее длине.А ударами молота кузнец может создать слегка изогнутую форму на одном конце, а также сделать одну сторону ширины тоньше другой.
Теперь сечение лыски на другом конце надо увеличить (для ручки), кузнец будет стучать по стороне (толщине) лыски в нужном месте и сечение увеличится (на стоимость ширины) из-за осадки. Кузнец бьет молотком с обеих сторон плоскости, чтобы переместить металл к центру, чтобы ручка оказалась в центре ширины.
Читая описанный выше процесс, мы с вами думаем, что это простая работа, однако для ее выполнения требуются опыт и навыки.
Зубчатая, фуллерная и кромочная
Это техника ручной ковки, и кузнец использует эту технику для создания кузницы сложной формы. Во время ручной ковки или силовой ковки можно использовать зубчатую, долевую и окантовочную обработку.
Зазубренность при свободной штамповке указывает на непрерывную деформацию заготовки по ее длине. Фуллеринг — это еще один процесс ковки в открытых штампах, в котором используются выпуклые открытые штампы для уменьшения (тонкости) поперечного сечения заготовки.
После достижения необходимой толщины зубчатой кромкой для достижения необходимой ширины. Кромка выполняется открытой матрицей вогнутой формы. Кромка названа так потому, что операцию кромки обычно выполняют на концах (кромках) заготовки.
2. Силовая ковка (ковка в открытых штампах с использованием молота)
Ковка в открытых штампах часто называется кузнечной ковкой, потому что она частично выполняется вручную. При открытой штамповке горячую заготовку металл кладут на неподвижную наковальню и молотом многократно ударяют по ней, чтобы деформировать заготовку.Кузнец непрерывно перемещает и манипулирует горячей заготовкой, придавая ей нужную форму.
Штампы, используемые при открытой штамповке, обычно плоские, однако для некоторых специальных применений могут использоваться штампы вогнутой или выпуклой формы. Кузнец использует специальные инструменты, чтобы пробить отверстие в поковке.
Процесс ковки в открытых штампах является важным методом производства и очень полезен, когда размер поковки большой, а количество меньше. Немногие кузнечные цеха могут делать поковки весом более 100 тонн и длиной более 50 футов.
Поковки в открытых штампах возможны во многих формах, а именно. прямые и ступенчатые валы, валы с фланцами, круги и кольца большого диаметра, поковки шестигранного сечения и несколько нестандартных форм. Точность формы и размера зависит от мастерства кузнеца. Много раз кузнец использует вилочный погрузчик с манипулятором для перемещения тяжелой заготовки во время ковки. Кузнец может использовать вилочный погрузчик, чтобы переместить заготовку в печь для повторного нагрева и снова вернуть ее к молоту.
Сила сжатия, приложенная вдоль оси заготовки, увеличит площадь поперечного сечения (за счет высоты), а сила сжатия, приложенная перпендикулярно оси заготовки, уменьшит площадь поперечного сечения (с увеличением длины) .
Кузнец использует такие приемы, как зубчатая обработка, долбление и окантовка, когда необходимая ковка требует поэтапного подхода. `
Преимущества свободной штамповки
- Существующие дефекты литья, такие как поры и пустоты, сведены к минимуму или устранены.
- Улучшение металлургической структуры и более мелкое зерно.
- Поток зерна непрерывен.
- Повышенная прочность и сопротивление усталости.
Ограничения поковок в открытых штампах
- Горячую заготовку необходимо постоянно манипулировать для достижения желаемой формы. Эта задача становится сложной для тяжелых поковок.
Ковка в закрытых штампах
Существует в основном три различных типа процессов штамповки в закрытых штампах.Они:
- Штамповка
- Поковка прессовая
- Машинная ковка
Давайте подробно рассмотрим каждый из этих процессов ковки.
1. Ковка
Для штамповки требуется набор штампов (верхний штамп и нижний штамп). Нижний штамп крепится к нижней балке или платформе ударного молота. Верхняя матрица крепится к подвижному ползунку.
Нагретую до температуры рекристаллизации заготовку укладывают на неподвижную матрицу и прикладывают повторную силу удара молотком 3-4 раза.
Более локальная деформация имеет место в верхнем и нижнем слоях заготовки. Поверхность будет тверже, чем металл заготовки. Деформация неравномерна по толщине металла.
Поскольку используется закрытая матрица, этот процесс можно использовать для изготовления изделий сложной формы. Однако для сложных форм требуется набор последовательных штампов. Сложные формы можно сделать за следующие шаги:
Матрица 1 Fullering : Уменьшите поперечное сечение заготовки до желаемого размера.
Матрица 2 Кромка : Кромка обеспечивает легкий поток металла в полость матрицы.
Матрица 3 Изгиб : Это изгибает заготовку, чтобы приблизить ее к окончательной форме.
Матрица 4 Блокировка : Это один шаг до окончательной формы, металл затекает в полость и принимает форму, очень близкую к окончательной форме.
Матрица 5 Чистовая обработка : Окончательная форма детали достигается, и немного дополнительного металла, содержащегося в заготовке, выходит из матрицы в виде заусенцев.Заусенец обычно обрезается штампом или может быть удален путем ручной шлифовки
2. Прессовая ковка
Ковка на прессах также использует закрытую матрицу (комплект из верхней и нижней матриц). Однако, в отличие от штамповки (где сила удара применяется многократно), штамповка на прессе использует постоянное увеличение давления для выполнения операции сжатия. Металл непрерывно сжимается между верхней и нижней матрицей до тех пор, пока металл не потечет и не заполнит полость. Металл заготовки принимает форму полости, когда матрица закрывается.Возможно формирование вспышки.
Как и при штамповке, при штамповке на прессах нижний штамп закреплен, а верхний штамп прижат к подвижной балке. Используемый пресс может быть механическим или гидравлическим, однако гидравлический пресс обеспечивает большее давление сжатия.
Благодаря высокому давлению происходит однородное и равномерное течение металла и обеспечивается равномерная деформация по толщине. Поверхность кованой детали более гладкая, чем полученная при штамповке.
Сила, используемая при ковке на прессах, достаточно высока и может более чем в два раза превышать силу штамповки.Из-за того, что требуется высокое давление, штамповка используется для деталей сравнительно меньшего размера.
Ковка на прессе может быть холодной или горячей ковки.
Преимущества штамповки
- Высокая производительность.
- Более высокий уровень контроля допусков на размеры.
- Процесс можно автоматизировать.
Ограничения
- Стоимость штампа и пресса выше, чем у штамповки.
- Обычно этот процесс ограничивается деталями небольшого размера из-за требуемой высокой силы сжатия.
3. Машинная ковка
Машинная ковка также известна под названием высадочная ковка. Несмотря на то, что вы используете машину для штамповки, а также для штамповки, в кузнечной промышленности «ковка с осадкой» известна под названием «машинная ковка».
Машинная ковка используется для процесса ковки с осадкой, обычно для формирования головок болтов, головок заклепок, а также может использоваться для автомобильных шпинделей и осей, которые необходимо осадить.
Это горизонтальная ковочная машина.
Ниже кратко описан пошаговый процесс:
Установка имеет неподвижную матрицу и подвижную матрицу и пуансон.
Горячая заготовка проталкивается между неподвижной и подвижной матрицей (нагревается только длина осадки). Подвижная матрица поднимается и смыкается со стационарной матрицей и захватывает заготовку.
Неподвижный штамп и подвижный штамп вместе образуют полость или форму штампуемой головки. В некоторых конструкциях штампов пуансон может иметь полость (в форме головки).
Пуансон движется с усилием, завершая процесс осадки поковки. После осадки подвижная матрица перемещается вниз и вынимается кованая деталь.
Как и в случае штамповки, осадочная штамповка осуществляется в несколько этапов. Заготовка перемещается с одного этапа на другой для завершения осадочной ковки.
Примерами машинной или высаженной поковки являются клапаны двигателей, муфты, болты, винты, автомобильные оси и другие крепежные детали.
Осадочная ковочная машина
Поковки с высадкой обычно изготавливаются на высокоскоростных кривошипных прессах.Ориентация этого станка горизонтальная, что позволяет легко перемещать заготовку с одного этапа на другой. Однако осадочный пресс может быть и вертикальным (кривошипный пресс или гидравлический пресс). Некоторые машины могут осаживать прутья диаметром до 25 сантиметров.
В этих станках используются разъемные штампы с несколькими полостями, а заготовки можно перемещать из одной полости в другую. Этот процесс можно автоматизировать с помощью роботизированных рук. Разъемная матрица закрывается после того, как заготовка загружена, и пуансон или вырубной инструмент перемещаются в продольном направлении, прижимают прут и выполняют осадку поковки, чтобы заполнить полость.Все полости можно использовать одновременно, и при каждом ходе пресса выходит одна часть.
Преимущества высаженной поковки
- Высокая производительность
- Возможна автоматизация.
Бесшовная прокатная кольцевая поковка
Производство поковок бесшовных катаных колец осуществляется на прокатных станах. Немногие прокатные станы способны производить кованые кольца диаметром до 15 футов. Бесшовное кованое кольцо изготавливается в следующие этапы:
Металл заготовки нагревают и увеличивают диаметр ее поперечного сечения до нужного размера осадкой.В центре пробито отверстие. Эта операция выполняется на молотке/прессе с открытым штампом.
Теперь заготовка выглядит как горячий пончик.
Заготовка после осадки и прошивки еще горячая и может быть взята на прокат. При необходимости его можно подогреть.
Заготовка помещается на пресс-оправку. Установка состоит из основного ролика и двух направляющих роликов, которые удерживают заготовку во вращении. Прижимная оправка движется радиально наружу под давлением, толкая и увеличивая диаметр кольца (увеличивается внешний и внутренний диаметр заготовки в форме пончика).Происходит уменьшение толщины кольца. Два конических ролика поддерживают движение кольца на лицевой стороне и помогают уменьшить толщину.
Еще немного о поковках
Припуски на ковку – Разработчик штампа должен учитывать следующие допуски при проектировании штампа (i) ковка производится при температуре рекристаллизации, и когда поковка достигает комнатной температуры, будет происходить усадка, и, следовательно, штамп должен обеспечивать допуск на усадку (ii) штамп подвергается износу из-за работы при высокой температуре и высоком давлении, и, следовательно, поверхность штампа изнашивается постепенно, следует учитывать этот износ штампа и (iii) припуск на механическую обработку.
Ковкость
Способность металла к ковке – это максимальная деформация, которую он может испытать до разрушения или растрескивания. При выборе металла для ковки детали важным фактором является кузнечная способность металла. Есть несколько тестов, чтобы узнать способность металла ковать.
Осмотр
Поковки должны быть осмотрены, прежде чем они будут перемещены для дальнейшей обработки. Дефектами поковки могут быть трещины, неправильно сформированные участки, коробление и др.
Смазка
Силы трения существуют между заготовкой и штампом во время процесса ковки и смазочных материалов, таких как вода, минеральное масло, графит и т. д.служат для уменьшения трения.
Автоматизация процесса горячей штамповки
Процесс горячей штамповки был автоматизирован в связи с необходимостью большого количества поковок. Автоматизация помогает значительно увеличить скорость производства и снизить удельную стоимость поковок.
Типичный автоматизированный процесс горячей штамповки может представлять собой загрузку стальных стержней стандартной длины (при комнатной температуре) на одном конце и получение кованых деталей на другом конце. На промежуточных этапах автоматизированная система обеспечивает резку прутка до необходимого веса, нагрев вырезанной заготовки до температуры рекристаллизации, перемещение ее на ковочный пресс для этапов ковки, обрезку заусенца, охлаждение поковки и ее выталкивание. .
Имеются конвейерные системы между этапами и может быть устройство для проверки размеров поковок. Ручного труда, затрачиваемого на этот процесс, очень мало. В некоторых процессах заусенцы устраняются, что увеличивает экономию металла.
Примерами деталей, изготовленных методом автоматизированной горячей штамповки, являются заготовки зубчатых колес, обоймы конических роликоподшипников, фланцы из нержавеющей стали и т. д.
Трубы бесшовные, Трубы бесшовные, Горячая и холодная штамповка
Ковка — это производственный процесс, при котором заготовке придается форма путем приложения к ней сжимающих усилий.По температуре, при которой выполняется ковка, классифицируется на «горячую», «теплую» и «холодную». В наиболее распространенных конфигурациях используются молотки или прессы для сжатия и деформации материала в высокопрочные детали.
Необходимо отметить, что процесс изготовления поковки полностью отличается от процесса литья, при котором расплав заливается в форму. Еще одно существенное отличие от других методов производства, таких как литье и механическая обработка, заключается в том, что ковка улучшает механические свойства материала, улучшая его зернистую структуру и делая его более жестким и прочным.
Горячая ковка означает ковку заготовок выше температуры проведенной рекристаллизации.
Особенности: снижает сопротивление деформации металлов, тем самым уменьшая усилие плохой ковки, необходимое для деформации материала, что значительно снижает тоннаж кузнечного оборудования; изменение структуры слитков, отлитых в процессе ковки, после рекристаллизации становится грубой литой структуры, новой организации мелких зерен, а также уменьшение дефектов литой структуры для улучшения механических свойств стали; Повышение пластичности затруднено для некоторых более хрупких при низких температурах поковок из высоколегированной стали, что важно.Применимо большое сопротивление деформации при комнатной температуре, плохой металл пластиковый материал. Диапазон температур ковки горячего металла относится к температуре, и температура начала ковки находится в некотором интервале между концом температуры ковки, чтобы предотвратить перегрев, сжигание необходимо правильно определить начальную температуру ковки и конечную температуру ковки. Основной подход заключается в определении температуры нагрева стальной основы, на которой изображено равновесие железа и углерода.
Холодная ковка производится ниже температуры рекристаллизации формовочного материала, ковка осуществляется при температуре ниже ответной.Производство, принятое на черновую негорячую ковку, можно назвать холодной ковкой. При холодной ковке температурная деформационная стойкость материала в основном невелика, пластик и некоторые алюминиевые сплавы лучше, а некоторые медные сплавы, малоуглеродистая сталь, углеродистая сталь, низколегированная сталь. Холодная ковка хорошее качество поверхности, высокая точность размеров, может заменить часть резки. Холодная ковка металла позволяет укрепить и повысить прочность деталей. Технология холодной ковки должна быть выше, чем температура прецизионной ковки и ковки, область прецизионной штамповки имеет свои уникальные преимущества.Процесс холодной ковки с использованием улучшенной обработки канала ствола, точности размеров, прочности поверхности, продления срока службы ствола, точности стрельбы, что соответствует увеличению пистолета, и простоте обработки конического ствола, качество может быть снижено.
Необходимо отметить, что процесс изготовления поковки полностью отличается от процесса литья, при котором расплав заливается в форму. Еще одно существенное отличие от других методов производства, таких как литье и механическая обработка, заключается в том, что ковка улучшает механические свойства материала, улучшая его зернистую структуру и делая его более жестким и прочным.
Холодная ковка
Производственный процесс холодной штамповки
Производственный процесс холодной штамповки осуществляется при комнатной температуре. Заготовка зажимается между двумя штампами до тех пор, пока не примет их форму. Чтобы получить законченный, готовый к установке компонент, метод включает прокатку, вытяжку, прессование, вращение, экструзию и высадку.
Преимущества холодной штамповки
Производители могут предпочесть холодную ковку горячей ковке; поскольку холоднокованые детали требуют очень мало отделочных работ или вообще не требуют их, что снижает затраты.Вторым существенным преимуществом является экономия материала, достигаемая за счет прецизионных форм. Экономических преимуществ в сочетании с высокой производительностью и длительным сроком службы штампа более чем достаточно, чтобы убедить многих производителей в том, что холодная штамповка является для них лучшим вариантом.
Недостатки холодной штамповки
В зависимости от требований производителя некоторые характеристики холодной штамповки могут оказаться недостатками; например можно формировать только простые формы в больших объемах. Поэтому, если заказчик ищет конкретный индивидуальный компонент, холодная ковка не будет лучшей альтернативой.Второй более существенный недостаток заключается в том, что холоднокованые металлы менее пластичны, что делает их непригодными для определенных конфигураций. Кроме того, из-за зернистой структуры, придающей материалу прочность, могут возникать остаточные напряжения.
Горячая штамповка
Производственный процесс горячей штамповки
Производственный процесс горячей штамповки осуществляется при экстремально высоких температурах (до 1150 °С для стали, от 360 до 520 °С для алюминиевых сплавов, от 700 до 800 °С для медных сплавов).Эта температура необходима для того, чтобы избежать деформационного упрочнения металла при деформации.
Преимущества горячей штамповки
Горячекованые детали обладают повышенной пластичностью, что делает их желательными для многих конфигураций. Кроме того, горячая ковка как метод является более гибким, чем холодная ковка, поскольку можно изготавливать детали по индивидуальному заказу. Превосходное качество поверхности позволяет выполнять широкий спектр отделочных работ, таких как полировка, покрытие или покраска, в соответствии с конкретными потребностями клиентов.
Недостатки горячей штамповки
Менее точный допуск на размеры является возможным недостатком горячекованых деталей по сравнению с холодноковаными. Процесс охлаждения также должен осуществляться в особых условиях; в противном случае существует риск деформации. Кроме того, структура зерна кованых металлов может быть разной, и всегда существует возможность реакции между атмосферой и заготовкой.
Горячая ковка против холодной ковки: заключение
Основное различие между горячей и холодной ковкой можно резюмировать следующим образом: Производственный процесс холодной ковки увеличивает прочность металла за счет деформационного упрочнения при комнатной температуре.Напротив, производственный процесс горячей штамповки предотвращает деформационное упрочнение материалов при высокой температуре, что приводит к оптимальному пределу текучести, низкой твердости и высокой пластичности.
Наконец, производитель предпочел бы один процесс другому из соображений экономии, а не качества. Решение основывается на требуемых функциях желаемого компонента, отрасли, а также на том, идет ли речь о массовом производстве или небольшом объеме деталей, изготовленных по индивидуальному заказу.
Setforge производит холодную и горячую ковку, которые выполняются в отличных условиях на современном оборудовании для достижения отличных результатов.Мы тесно сотрудничаем с нашими клиентами, чтобы понять их конкретные потребности и найти наилучшее возможное решение.
Что такое ковка? • Аэростар Производство
Новичок в ковке? Вот разбивка:
Согласно справочнику IQS:
Что такое ковка?
«Древнее искусство ковки делится на две отдельные категории — горячую и холодную, где горячая ковка существовала веками, а холодная ковка появилась только во время промышленной революции 19 века.Хотя это совершенно разные процессы, конечные результаты одинаковы. Ковка — это метод деформации металла в заданную форму с использованием инструментов и оборудования, где деформация достигается с помощью процессов горячей, холодной или теплой ковки. Выбор процесса зависит от металла и желаемой формы конечного продукта.
Горячая штамповка и принцип ее работы
«Горячая ковка происходит, когда кусок металла перегревается выше точки кристаллизации. Средняя температура, при которой это происходит, зависит от типа металла, где сталь кристаллизуется при температуре до 1150°С, сплавы алюминия от 360°С до 520°С и сплавы меди от 700°С до 800°С.Необходимая температура должна поддерживаться выше точки рекристаллизации или точки, при которой металл начинает остывать. Рекристаллизация может привести к образованию микроскопических кристаллов, которые деформируются при повторном нагреве металла, вызывая его «деформационное упрочнение», что делает его непригодным для обработки.
«Факторы окружающей среды могут влиять на процесс горячей штамповки, когда контакт с атмосферой может вызвать окисление. Чтобы избежать этого, ковка может быть завершена в камере с контролируемой средой или изотермической ковкой, аналогичной вакууму.
«Главное преимущество горячей штамповки — прочность металла. Горячекованые металлы обладают высокой пластичностью, способностью значительно деформироваться и изменять форму, что придает им большую устойчивость к растягивающим напряжениям. Детали, изготовленные методом горячей ковки, прочнее, потому что в процессе ковки изменяется внутреннее зерно детали, изменяя ее форму и прочностные характеристики.
Что следует учитывать при выборе горячей штамповки
«Горячая ковка используется при производстве нескольких различных компонентов и деталей, поскольку этот процесс позволяет получать изделия высокой точности и сложной формы.Он идеально подходит для металлов, которые обладают высокой формуемостью или легко деформируются. Металлы, сформированные при горячей ковке, набирают прочность и становятся более прочными. Это гибкий процесс, позволяющий производить индивидуальные детали. Превосходное качество поверхности горячештампованных деталей позволяет использовать различные способы отделки и полировки.
«Некоторые из уникальных результатов горячей штамповки включают в себя возможность легкого изготовления отдельных деталей, точность от низкой до средней, образование окалины на металле, низкий уровень напряжения металла с более низкими температурами деформационного упрочнения, гомогенизацию зерна, более высокие уровни пластичности и устранение химических несоответствий в металле.
Отрицательные факторы горячей штамповки:
«Независимо от того, насколько производительна горячая штамповка, у нее есть определенные недостатки, которые необходимо учитывать. В процессе охлаждения всегда существует вероятность того, что металл может деформироваться и стать хрупким. Есть некоторые металлы, которые не следует использовать в горячей ковке, поскольку это может привести к менее точным допускам, а также к отклонениям в структуре зерна.
«Хотя у горячей ковки есть недостатки и недостатки, она хорошо подходит для производства аэрокосмической продукции и деталей самолетов.Мягкость, создаваемая металлами, позволяет легко придавать им форму и создавать сложные узоры, необходимые в этих отраслях.
Преимущества холодной штамповки или штамповки
«Холодная ковка относится к процессу формообразования и деформации металла, который выполняется при комнатной температуре или немного выше ее, при этом температура поддерживается на уровне около трех десятых точки рекристаллизации металла. Сжатие, изгиб, резка и волочение являются наиболее распространенными методами холодной ковки. Мягкие металлы, такие как алюминий или медь, идеально подходят для этого процесса.
«Метод холодной ковки использует силу сжатия для придания заготовке формы вручную или на станке. Во многих случаях металл проталкивают в форму, имеющую форму конечного продукта. Это дешевле, чем горячая ковка, и позволяет производить готовые изделия, которые практически не требуют отделки. Что касается алюминия, то после холодной ковки его подвергают термообработке для повышения прочности, процесс, известный как «закалка».
Уникальный процесс холодной ковки
«Наиболее распространенными металлами при холодной ковке являются стандартные или легированные углеродом стали.Он используется для производства небольших изделий большого объема, таких как крепежные детали, такие как гвозди, шурупы, заклепки и тому подобное. Отсутствие потребности в тепле делает его недорогим и эффективным. Типы используемых методов холодной ковки во многом зависят от металла и требуемой формы. Ниже приведены описания некоторых распространенных процессов холодной ковки.
Штамповка штампованная
«Распространенной формой холодной ковки является штамповка штампом, при которой металл помещается в штамп, прикрепленный к наковальне. По металлу ударяют молотком, чтобы он вошел в матрицу.В зависимости от продукта молоток может падать несколько раз подряд.
Сжатие
«Сжатие, также известное как проклейка, минимизирует толщину металла за счет приложения давления, которое определяется площадью проклейки, типом металла и необходимым изменением толщины металла. Обычно это делается для придания точности размеров кованой детали.
Холодная прокатка
«Холодное профилирование позволяет получить более привлекательные готовые поверхности с более жесткими допусками в различных формах, которые можно легко оцинковывать, красить или покрывать порошковым покрытием.Тонкие листы металла, обычно стали, прокатывают в такие формы, как панели пола и крыши, формы C или Z.
Чертеж
«Чертеж использует силы растяжения для вытягивания или растяжения металла до определенной формы или толщины. Существует две формы волочения – листовой металл и проволока, стержень или трубка. Чертеж можно наносить только на определенные виды металла или материалов, обладающих достаточной прочностью на растяжение. Хотя это может показаться похожим на холодную прокатку, оно отличается величиной и положением приложенной силы.
«Холодная ковка имеет другие процессы, предназначенные для придания формы металлам. Перечисленные здесь являются общими, но лишь немногие из многих, которые используются. Это популярный процесс среди производителей автомобилей для производства деталей рулевого управления и подвески, некоторых тормозных систем, осей и многих других автомобильных деталей.
Что следует учитывать при выборе холодной штамповки
«Холодная штамповка имеет несколько преимуществ. Во-первых, это делается при комнатной температуре и не требует нагрева металла, что позволяет свести стоимость отдельных деталей к минимуму.Все оборудование, связанное с горячей ковкой, такое как доменные печи и промышленные печи, не является необходимым.
«Детали, изготовленные методом холодной ковки, изготавливаются быстро и однородно с превосходным контролем размеров, что делает его привлекательным для компаний, которые имеют большие объемы производства и требуют быстрых сроков выполнения работ. С использованием компьютеризации каждый изготовленный компонент абсолютно одинаков во всех деталях и сложности. Штампы, используемые для холодной ковки, служат дольше, так как им не приходится выдерживать нагрузку и износ горячих металлов.
«Процесс холодной ковки более точен и позволяет производить прецизионные детали с высокими допусками. Соответствие проектным спецификациям повышает однородность каждой детали с меньшей вероятностью дефектов или ошибок, которые потребуют повторения производственных циклов, а детали имеют превосходную структуру зерна.
«В эту эпоху заботы об окружающей среде важным фактором является экологичность холодной ковки, поскольку детали формуются и формируются под высоким давлением при комнатной температуре.В отличие от других процессов, холодная ковка гарантирует, что в заготовке не останется пузырьков воздуха или других деформаций.
«Некоторые из других преимуществ холодной ковки включают более эффективное использование материалов, более низкие затраты энергии и практически полное отсутствие отделки. В условиях роста стоимости энергии и нехватки материалов холодная ковка является решением для производства деталей, эффективно снижающим влияние этих факторов».
Оригинальный источник
Отличия горячекатаного, холоднокатаного и кованого прутка
В мире пруткового проката существуют разные способы производства прутка, и при покупке прутка следует учитывать несколько различных моментов.Часто время выполнения заказа, количество и качество являются определяющими факторами при принятии решения о покупке батончика. Конечное применение также может играть важную роль и может варьироваться от продукта, который использует всю длину 20-футового стержня, до частей стержня, отрезанных и обработанных до уникальной геометрии. В этом блоге мы обсуждаем варианты, которые могут предоставить покупателям как большие, так и малые количества: горячекатаный пруток, холоднокатаный пруток и кованый пруток. (Обратите внимание: существует еще один процесс, при котором расплавленный стержень проталкивается через пресс-форму, называемый горячим волочением или экструдированием.Этот метод не идеален для закупок в небольшом количестве.)
Итак, горячекатаный против холоднокатаного и кованого проката
Прокатка и ковка прутка сводятся к одному и тому же фундаментальному процессу уменьшения толщины или изменения площади поперечного сечения металла под действием сжимающих усилий. Другими словами, большой кусок металла, известный как заготовка, прессуется до размера, формы и длины, необходимых для проекта. Этот процесс не только придает стержню форму, но также придает стержню свойства прочности.
Что такое горячекатаный прокат?
Это процесс нагрева заготовки до температуры более 1000 градусов по Фаренгейту, выше фазы рекристаллизации металла, чтобы она стала пригодной для обработки, а затем прокатки ее через строгальный стан или ролики, чтобы придать ей форму. Нагрев металла жизненно важен, потому что изменение молекулярной структуры металла образует дендриты (нитевидные спорадические структуры) в зерна (организованные блочные структуры), что происходит только тогда, когда металл находится в ковком состоянии. Создание более прочного металла происходит не только за счет образования зерен, но и за счет направленного потока зерен, достигаемого при прокатке прутка.
Плюсы и минусы Горячекатаный стержень
Горячекатаный пруток изготавливается быстро и легко изготавливается из одной или нескольких деталей. К сожалению, где горячекатаный пруток не соответствует требованиям, так это в допусках на размеры. Когда металл остывает, он сжимается, что приводит к деформации, областям различной толщины и шероховатой поверхности, а это означает, что требуется механическая обработка, если важна точность размеров или тип отделки. Наконец, для горячекатаного проката время решает все. Если цикл прокатки пропущен, время выполнения заказа увеличивается, поскольку дополнительный пруток не будет производиться до следующего прохода стана.
Что такое холоднокатаный прокат?
Этот процесс берет все, что мы только что обсуждали в отношении горячекатаного проката, и добавляет один шаг. Когда пруток достигает температуры, близкой к комнатной, его протягивают через штампы или повторно прокатывают в процессе прогрессивной прокатки. Этот дополнительный этап по своей сути добавляет стержню деформационное упрочнение, поскольку он обрабатывается после рекристаллизации. Деформационное упрочнение может упрочнить металл только настолько сильно, что основная часть упрочнения достигается во время молекулярной реструктуризации, обеспечиваемой горячей прокаткой, в зависимости от марки.
Плюсы и минусы Холоднокатаный стержень
Холоднокатаный прокатимеет лучшие размеры, прямолинейность и повышенный предел текучести. Он, опять же, используется для требований к одной или нескольким деталям. Но с дополнительным этапом или повторной прокаткой холоднокатаный пруток требует много времени и может увеличить время выполнения заказа. Однако, в отличие от горячекатаного прутка, дополнительная обработка для повышения точности не требуется, а отделка не такая масштабная.
Что такое кованый стержень?
В этом процессе, подобно горячекатаному прутку, берется заготовка и нагревается до тех пор, пока она не станет ковкой.Здесь процессы различаются, вместо прокатки прутка, чтобы получить его по размеру, ковки либо молотков, либо прессования прутка до требуемых грубых размеров. Операция дает стержню минимальный коэффициент обжатия 3: 1, что означает, что размер зерна намного меньше и плотнее в кованом стержне, и он консолидирует центры, если есть какие-либо проблемы с трубами. Затем, в зависимости от диаметра прутка, его пропускают через строгальный станок, придавая ему гладкую округлую поверхность.
Плюсы и минусы Кованый стержень
Процесс кованого проката
использует лучшее из горячекатаного и холоднокатаного проката и достигает этого быстро и эффективно.Эти стержни сохраняют размеры и прямолинейность по мере охлаждения, но при этом имеют еще более высокий предел текучести из-за уникальной способности поковок создавать центры звука на этапе ковки. Минимальное уменьшение 3:1 помогает устранить любые проблемы с неуплотнением центральной линии, которые влияют на качество стержня. В отличие от дополнительного этапа холодной прокатки, дополнительный этап прокатки после ковки выполняется, пока пруток горячий, поэтому после охлаждения не тратится время на дополнительные процессы. Кованый стержень может использоваться для одно- или многокомпонентных требований и производиться по запросу.Другим существенным преимуществом являются большие диаметры. Прокатный стержень изготавливается определенного максимального размера, при этом кованый стержень имеет более широкий диапазон диаметров.
Если вы новичок в ковке или хотите сравнить качество прутков, команда Scot Forge Bar готова помочь вам с выбором. Свяжитесь с нашей командой Scot Forge Bar для получения дополнительной информации о кованых стержнях. Ковка не всегда может быть лучшим вариантом для вашего проекта, и если это так, мы будем рады указать вам направление поставщиков, которых мы знаем и которым доверяем.
.